Almost unnoticed by the world, a small manufacturer in Denmark is quietly working away building trailed tub-grinders for straw, grain, wood and silage. The rotor crushes any type of biomass – provided the tractor has sufficient power.
KEEPING IT BRIEF
- Gronning Smede designs and manufactures the I-Grind processor.
- In addition to straw and grain, the I-Grind deals with other organic substrates such as chicken manure or wood chips.
- Being built in Europe should make for better back up and service for the solidly built machine.
- Minimum power input is 200hp but the rotor can handle up to 500hp.
It’s only been in the last 15 to 20 years that the concept of using tub-grinders to process straw and forage has really taken off in the UK and Europe. An idea originally conceived in the US, the basic principle is simple – ground almost to dust, straw is more absorbent than when it is simply chopped. It also makes mucking out sheds a whole lot easier.
For anaerobic digesters there’s a big benefit to feedstocks that are ground to a fine pulp yield more gas and are easier to stir. More and more Scandinavian biogas producers also like to mill wet grain straight from the field. By adding propionic acid, they can store the grain for a long time without incurring high drying costs.
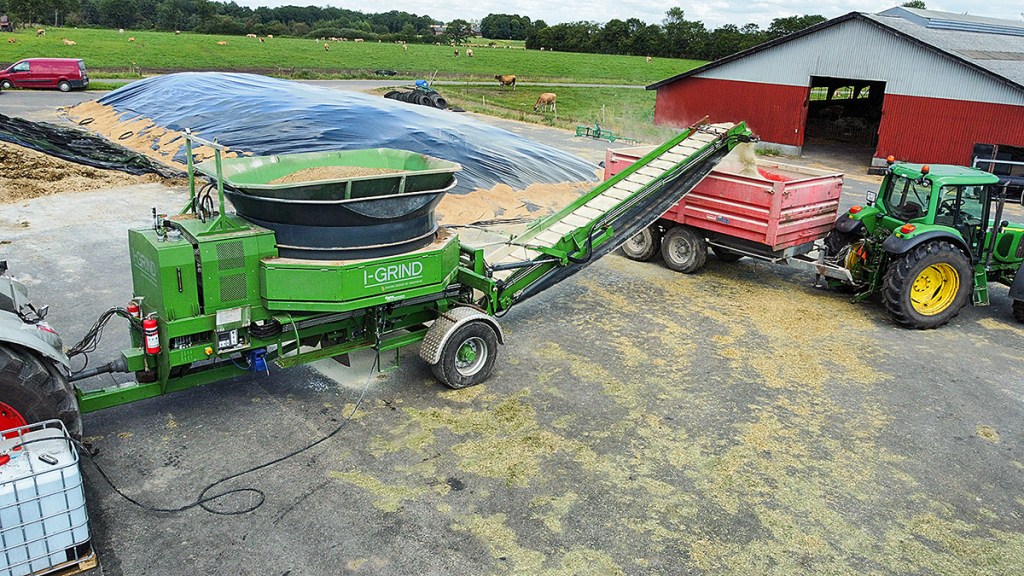
From an importer to a manufacturer
The I-Grind is actually a newcomer to the market of trailed mills. Based in the north west of Denmark, Gronning Smede is a specialist manufacturer of agricultural machinery. 15 years ago, the company was importing straw processors from the other side of the Atlantic. But in a move to develop a machine more suited to European customers, in 2015 the Scandinavian company took matters into its own hands and started building tub grinders at its own manufacturing facility in the US.
Supply problems during the coronavirus era and fluctuating exchange rates when the war in Ukraine started made importing machinery from the States to Europe increasingly difficult and in 2022 production was shifted from the USA to Denmark.
From a practical perspective the big benefit of this move was a shift from imperial to metric nuts, bolts and fittings. In addition, hydraulic and electronic components made on this side of the water makes more sense to those mechanics more used to ‘European logic’.
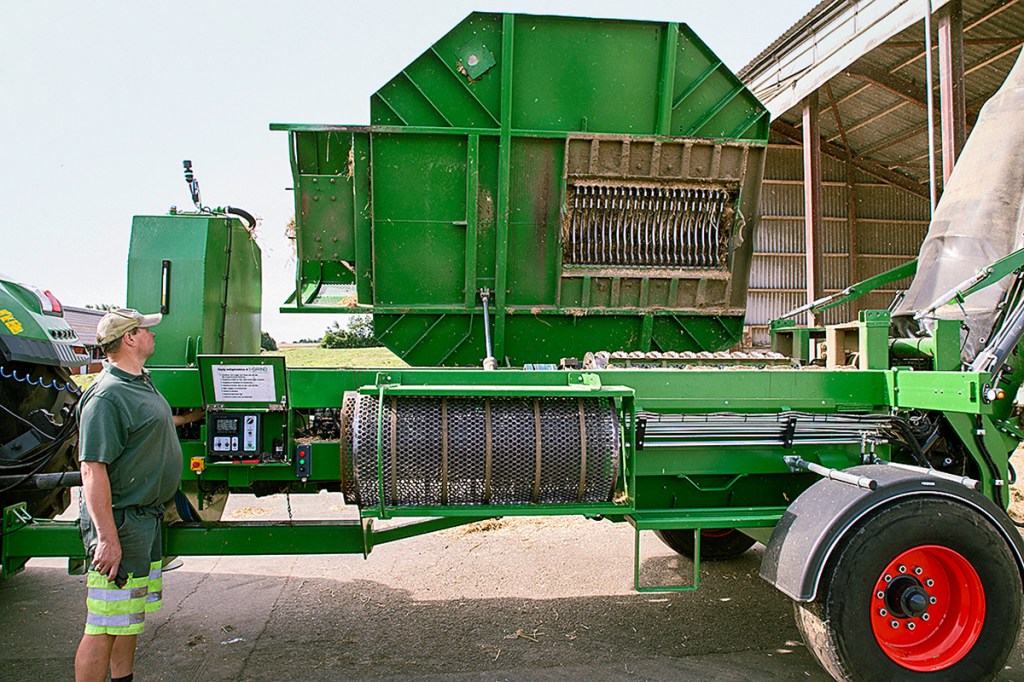
According to Gronning Smede, the components are selected according to their reliability and durability. Therefore, the rotor shaft is somewhat over-engineered. All the major moving parts benefit from an autolube system although there are another 30 nipples need to be located and greased manually.
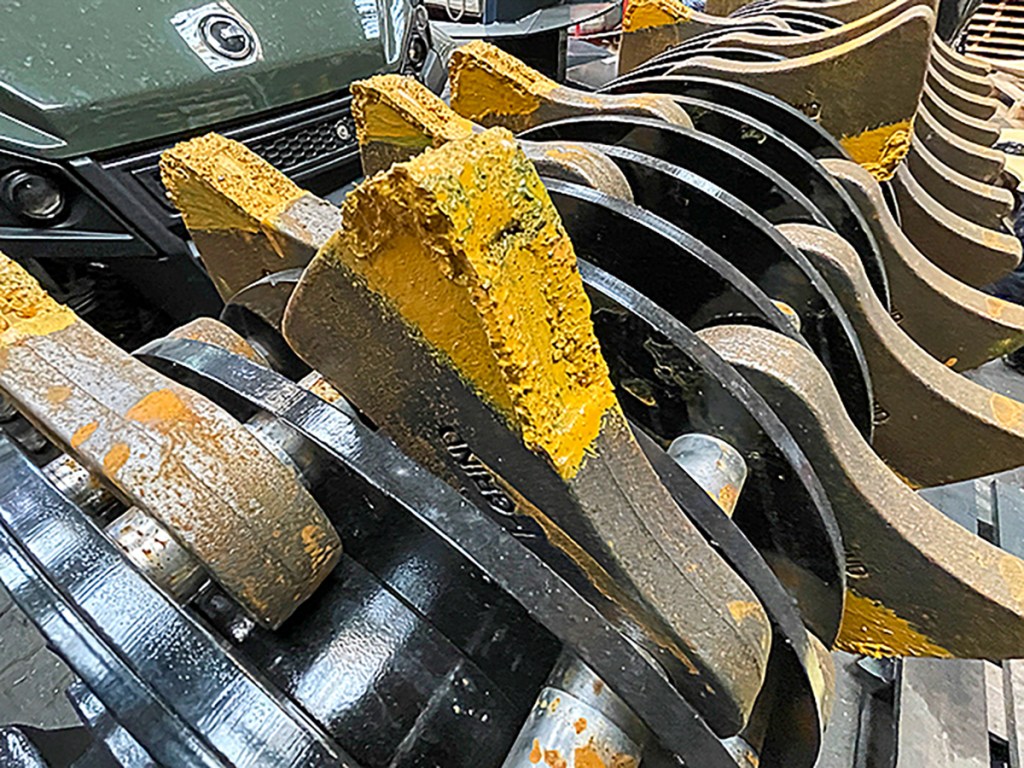
High standards
At the heart of the I-Grind is a 120cm long rotor with 88 flails arranged in eight rows. In the heaviest-duty version, one single hammer weighs 3.5kg. The screens come in various mesh sizes to control how finely the material is ground. The smallest mesh diameter is 0.5mm and there is no upper limit. You can even grind without a sieve in place.
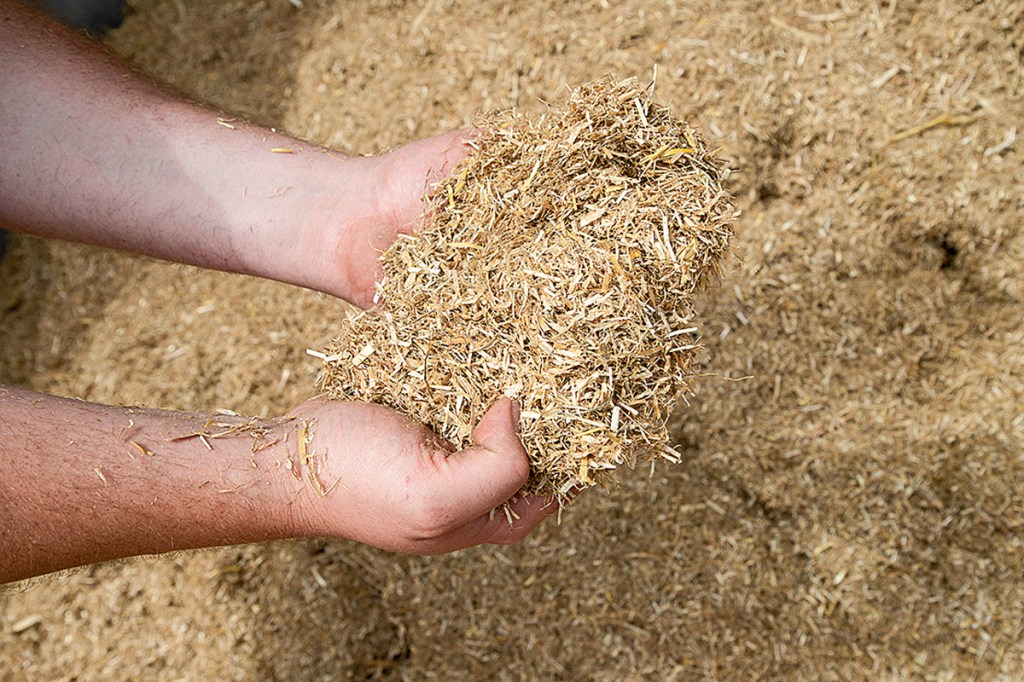

Swapping screens takes less than two minutes and is done without tools. The most time-consuming part is tilting the hopper, which is handled by the on-board hydraulic system.

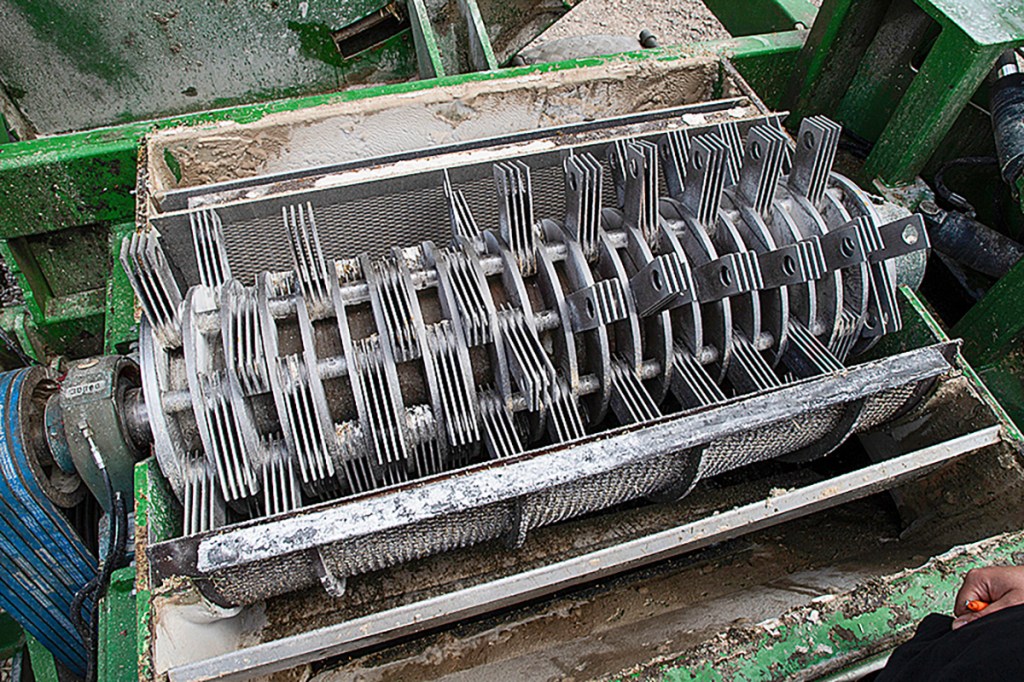
Proven principle
The operating principle of the I-Grind is similar to that of well-known tub grinders from the USA. For example, the rotor is firmly integrated into the base frame of the grinder so that the flails protrude into the hopper when the rotor is spun up on the tractor pto. The tub, which measures 3.00 to 3.30m in diameter, rotates during the grinding process thereby ensuring that the material is constantly pressed against the rotor.
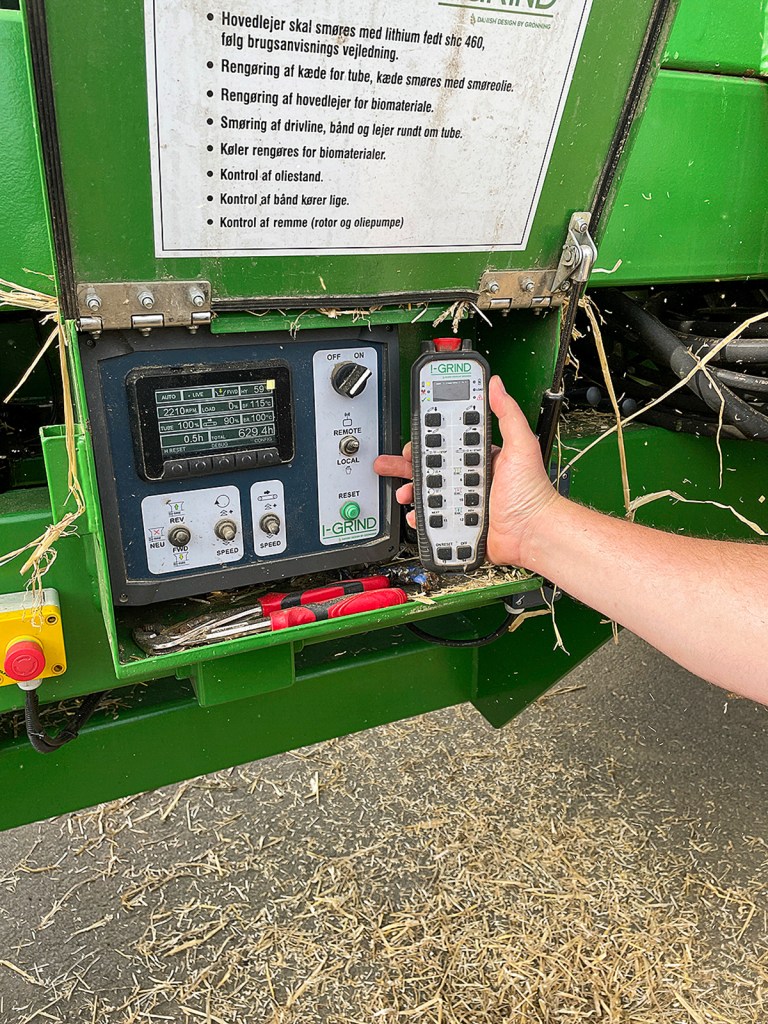
An automatic system controls the cyclical speed of the 3.00m high hopper while sensors detect the current load on the rotor and tractor. If the rotor speed drops below 1,800rpm, the hydraulically driven tub turns more slowly or even stops. As such, the grinder and the tractor are always running at their optimum and the risk of bunging up is reduced.
Theirs is no mechanical intervention in material feed, it’s simply governed by gravity and the speed of the tub rotation.
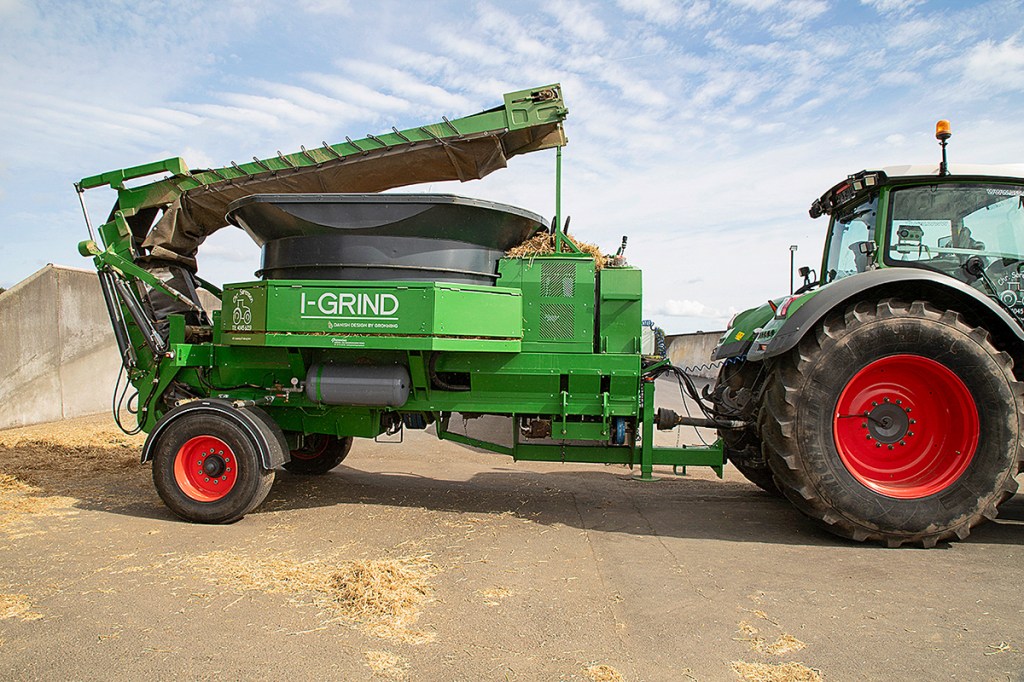
The ground material drops into a chute in which an auger or optional conveyor feeds it towards the unloading belt. The discharge conveyor reaches out to 7.30m and has a minimum 4.00m overhead-unloading height. Using the machine’s remote controls, it can be pivoted left to right. For travel on the road, it folds down in the middle reducing the transport height to less than 4.00m. The total width is 3.00m.
Compressed air and 40km/hr
The 300-litre hydraulic oil reservoir is perched over the drawbar between the tractor and the hopper. There is also an extra oil cooler that, according to Gronning Smede, ensures the oil will never overheats, not even under continuous high loads. Tractor power is transmitted to the rotor by a driveshaft with an overrun clutch. Ten belts run to the rotor shaft.
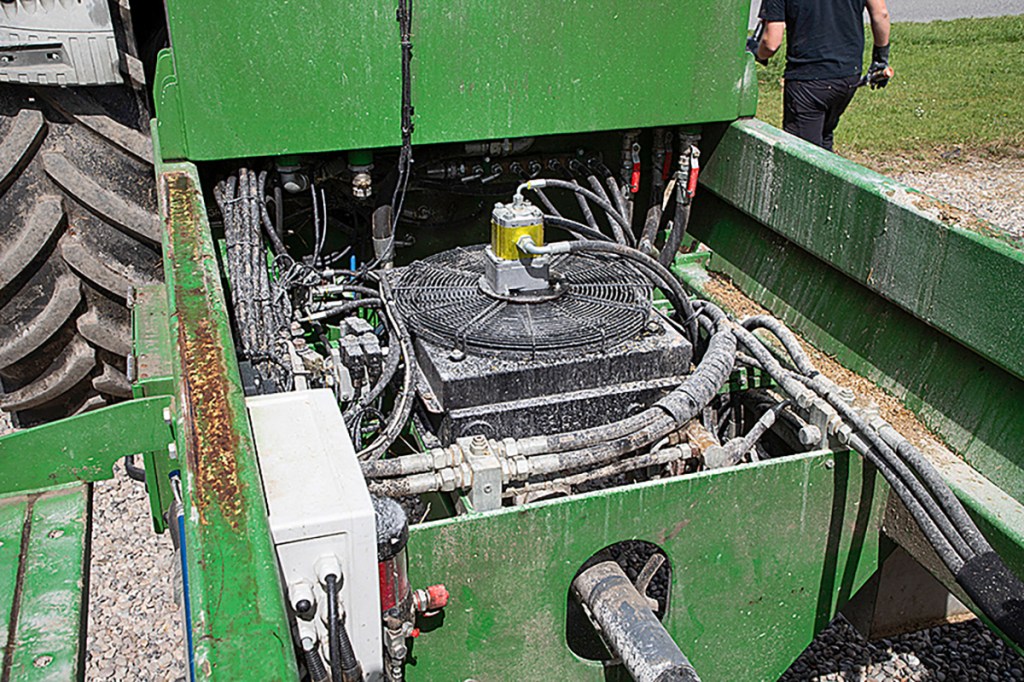
The entire construction is supported and held by a steel frame mounted on the drawbar. As the discharge belt shifts the machine’s centre of gravity rearwards when it unfolds – the axle is positioned as far back as possible. The good news: despite its weight of 8.6t, the grinder is approved for 40km/hr road travel courtesy of dual-circuit air brakes and 385/65- 22.5 tyres.
The field test
We had the opportunity to use a refurbished 2018 I-Grind from US production for milling straw and a 2022 I-Grind built in Denmark for grinding grain. The US-made machine is owned by Christian Sørensen from Kjellerup (Denmark). As a contractor, he clocks up about 700 hours a year grinding straw for dairy farmers. These customers are up to 80km away from his base and use the fine material primarily for bedding cubicles.
Sørensen operates his mill with a 500hp Fendt 1050 Vario which can be seen to visibly struggle as it squeezes dry square straw bales through the screen.
“With the 15mm mesh, the Vario guzzles 50 to 60l/hr of diesel, sometimes even 80l/hr when the straw is wet,” says Christian Sørensen, summing up the power requirements of his mill.
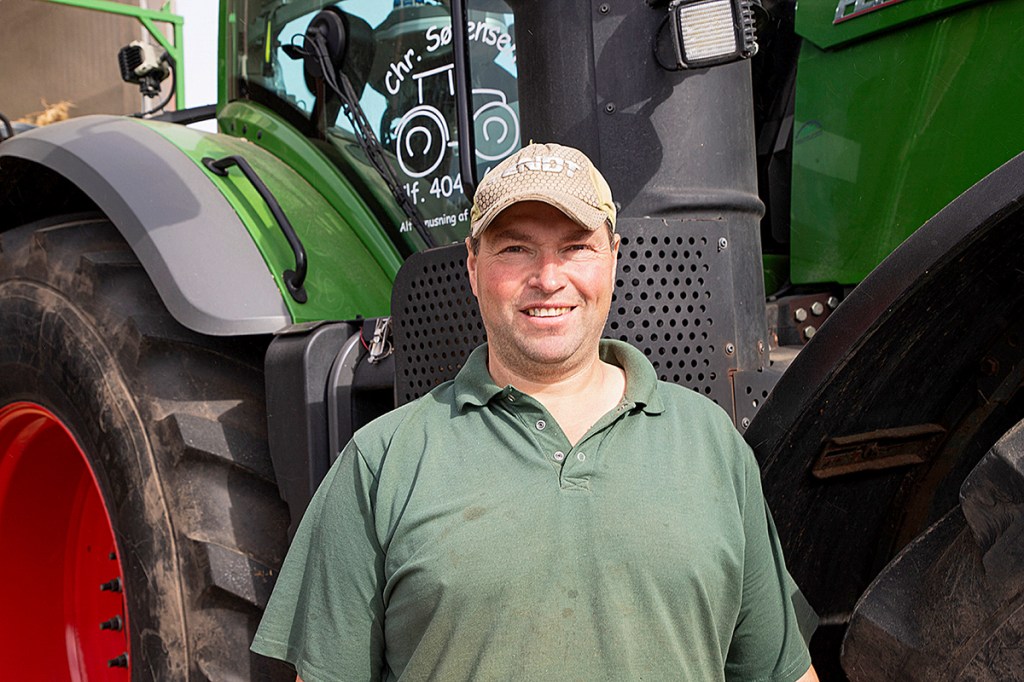
In 2023, a foreign object in a bale caused sparks and the mill caught fire. It was rebuilt and repainted 639 hours before our test. As a preventative measure, I-Grind has now equipped the machine with infrared cameras for fire detection and an automatic fire extinguisher system.
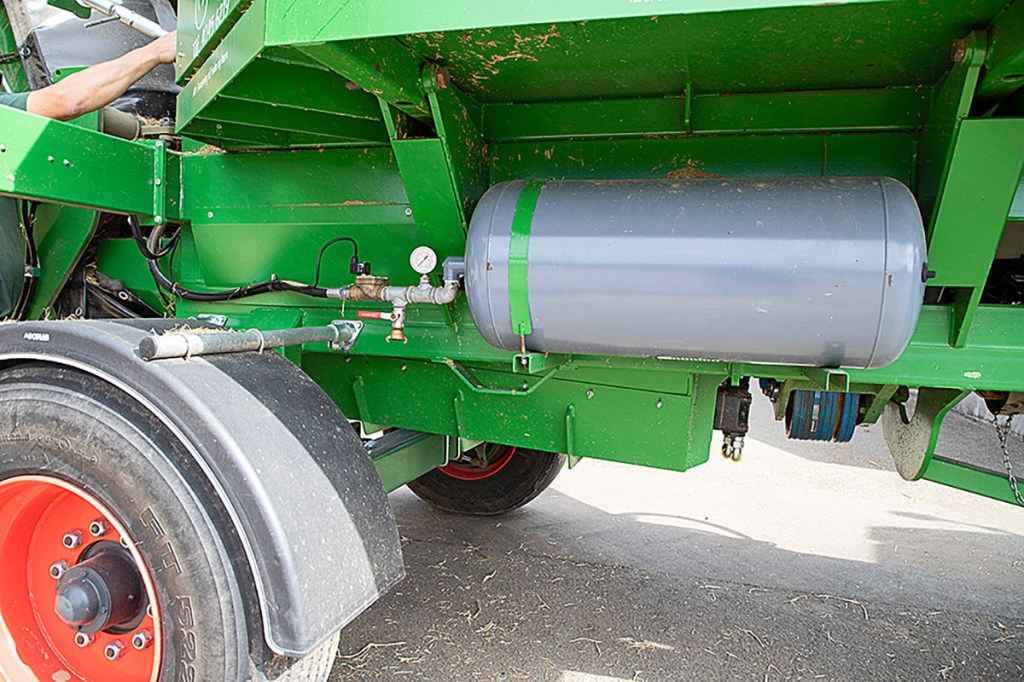
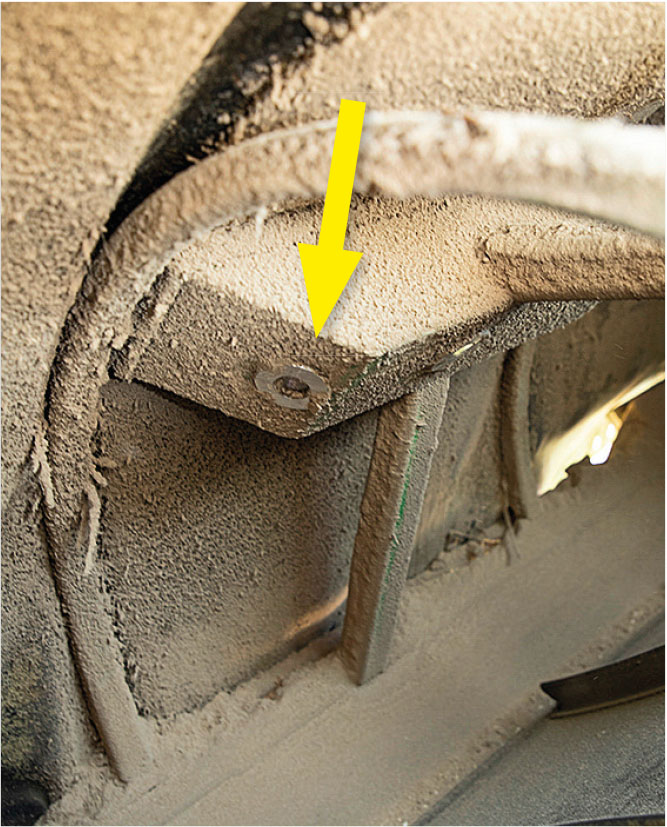
Since 2018, his machine has clocked 3,000 hours. The contractor estimates the service life of the 3.5kg carbide-coated flails to be 1,200 operating hours. To ensure they wear evenly, he swaps them after 600 hours – the outer ones move to the centre of the rotor and vice versa.
With the I-Grind running, ear plugs in and remote control in hand, Christian can be up to 150m away from the machine and still monitor and tweak all the major functions. A small display on the handheld control box provides him with key data on the current load or the oil temperature.
It takes five minutes to grind a 640kg bale of straw – that translates into 7.7 tonnes of material processed every hour. Wet straw and the size of the screen are the limiting factors for the machine.
“My customers want the straw to be very finely ground. If coarse grinding were sufficient, I could process 30 to 35 tonnes per hour,” Sørensen explains. Consequently, the degree of grinding has an immense influence on throughput, power requirement and wear.
Grinds up to 40t/h of grain
We took a close look at the 2022 machine while grinding grain. As you walk around the mill, you notice a few small design changes to the US version – for example, a different configuration of the hydraulic pumps. Build quality, too, was upped which is particularly evident in the welding.
The manufacturer offers an additional grain package which consists of small perforated screens, narrow flails, a 3.0m3 funnel to be fixed in the hopper and a propionic acid dispenser.
The machine ground rye that was harvested wet. Clearly, the powering Fendt 939 was never bored – especially when rapeseed was ground alongside the rye. We therefore have to rely on the manufacturer’s specifications at this point. These claim grinding capacities of 25t/hr in dry rye and 40t/hr in dry barley or wheat.
The costs
Gronning Smede currently offers only the one model described here. The base specification 40km/hr machine with 7.00m discharge belt and remote control is list priced at €230,000. The fire extinguisher system coupled with an infrared camera costs an extra €13,000. If you also want to process grain with the I-Grind you’ll need various extras including the acid dosing system. You can expect to pay another €15,000 for all of that.
Summary
The I-Grind is a tub grinder that has clearly been designed for the European market. Simply because it has metric threads and uses components manufactured in Europe, the Danish built straw and grain mill far more straightforward to repair and source parts for than machines made in the USA. Initial experience with units that have clocked over 3,000 hours suggest it’s a solid and durable design. We liked the automatic load control and the remote control which allows the I-Grind to be operated easily and independently of the tractor.
We found no gripes with grind quality. This said, the power requirement of the I-Grind is remarkable – although it is specified for a minimum of “200hp” it may well swallow 500hp and more.
Martin Zäh
For more up-to-date farming news click here and subscribe now to profi and save.