How can fertiliser distribution along field boundaries be optimised? Deula Nienburg has compared longstanding side-mounted border spreading systems with ones using a central deflector.
KEEPING IT BRIEF
- Farmers should check the accuracy of their border spreading system with trays/mats.
- In the profi test, Deula Nienburg tested various border spreading methods with and without such a central plate.
- Border spreading can be optimised by ensuring the settings are correct.
No matter how hard manufacturers of fertiliser broadcasters try, it’s nearly impossible to spread granules at full rate right up to the edge of the field using a side-mounted boundary spreading system and expect zero application beyond the edge of the crop. However, there is an alternative: a central deflector and one extra pass along the boundary could be the solution to maximising yield up to the field edge while still being environmentally mindful.
We wanted to review whether this relatively recent boundary spreading technology does indeed bring a real and tangible improvement to fert distribution accuracy. So, we brought together three fertiliser spreaders that use a central deflector for this test comparison. The test machines were an Amazone ZA-TS 4200 ProfisPro Hydro with 36m working width, a Bogballe M35W Dual Dynamic with a 27m spreading width and a Kuhn (Rauch) Axis H 30.2 with a 30m working width.
Since there is more potential to fire fertiliser beyond the intended area at larger working widths we opted to stay within the 27-36m band.
Once out in the test field, we measured the distribution while using the traditional side border spreading method and then with the central deflector, each with different settings. The results are plotted in the graphs on the following pages.
THE TEST CONDITIONS
All three makes were supplied and set up by the manufacturers to spread at a rate of 150kg/ha at a forward speed of 12km/hr.
The fertiliser used in the test was rolled potash (48% K2O) from K+S which was supplied in factory-filled big bags. Unlike most other potash fertilisers, it is not compacted and angular but granulated. This means the rolled potash offers similarly good storage and spreading characteristics as calcium ammonium nitrate (CAN), for example.
Before we cracked on with our tests, we asked the manufacturers to test the fertiliser for its physical properties, including granule size spectrum and granule hardness, and then compared this data with our own lab results. Incidentally, we recommend every farmer to do this and send in a sample of their fertiliser. By checking the fertiliser quality, we were able to optimise the machine settings before we actually started the tests.
As we were not interested in comparing the different makes with each other it didn’t matter that the spreading widths were not identical and neither did wind conditions play a part. Our focus was purely on the benefits of the central deflector.
In order to determine the distribution across the width, we placed four trays in 17 rows at a width that was equivalent to one and a half tramlines. In addition to that, we lined up more trays in two rows next to the field boundary.
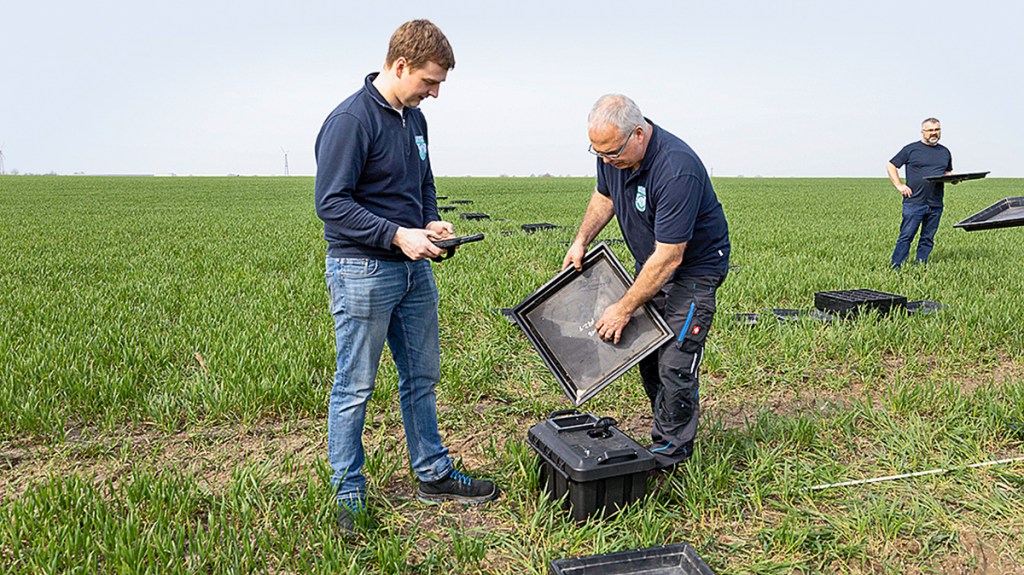
AMAZONE WITH AUTO-TS AND BORDER-TS
Amazone decided to send a 36m broadcaster to the test, hence was the largest width in the group. Its standard border spreading system (AutoTS) produced good results in the first and ‘regular spreading’ test run. However, the rate dropped drastically on the last 6 metres along the border and granules could be found outside the boundary (blue bars shown in the graph ‘Amazone: standard border spreading system’).
The second test run focussed on maximising crop yield. For this, we altered the speed of the spreading disc against the border, changing it from 900rpm to 970rpm. Now the granules were thrown closer to the border; but at the same time and as expected, more granules landed on the road (see the green bars in the graph ‘Amazone: standard border spreading’). If the disc speed had been reduced, the arc would have moved farther to the left relative to the reduction in speed. This would have been more environmentally friendly but crop yield would have been lower.
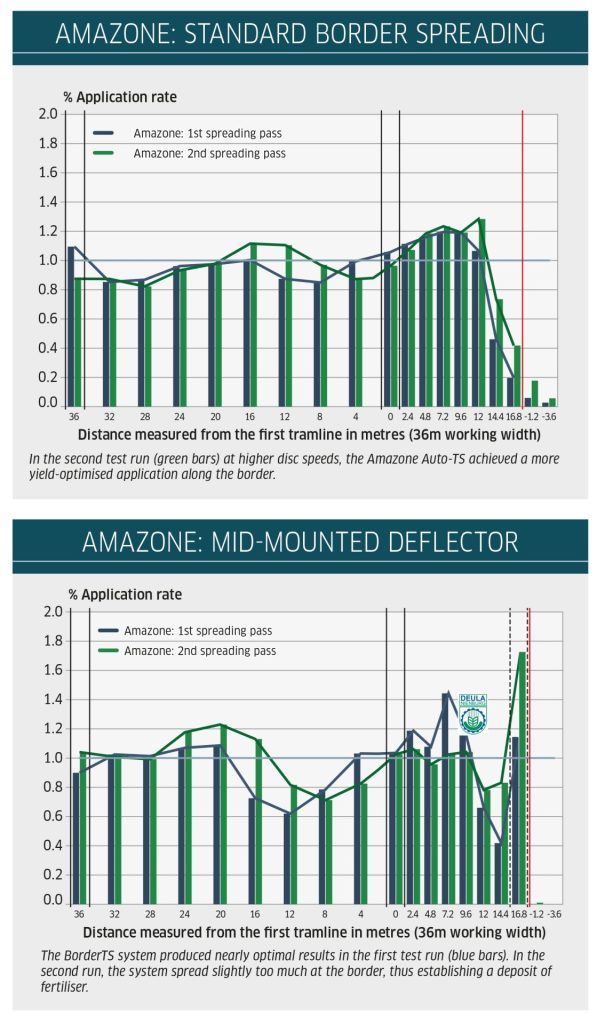
Half-width spreading and central deflector
When using the ‘BorderTS’ central deflector for border spreading, the first pass is carried out by travelling right along the border and spreading at half width using the BorderTS deflector. You do need to cut the application rate to 50% for this pass. The remaining 50% is applied in the next pass, running in the first tramline with AutoTS activated.
The only setting that is done to the BorderTS deflector is the distance to the border. This distance is measured from the middle of the tractor and the setting range is between 1.0m and 3.0m.
On the terminal of the ZA-TS 4200 ProfisPro Hydro, the driver can easily see whether the BorderTS border spreading system is enabled. The on-board computer looks after all of the needed changes to the disc speed and delivery system automatically, which stops any user setting errors. The only time the operator has to watch out is when using section control. This must be disabled for border spreading with the central deflector, as the spreader has to apply the 50% rate twice. If it is left on, the spreader thinks that the area has already been covered even though it has only received half the rate. To overcome this, you have to delete the area covered or create a new job after completing the pass with the BorderTS system enabled.
With the spreader set up according to the setting chart and the central deflector enabled, it produced a very even pattern in the first test run: no granules were thrown beyond the border; at the same time the target application rate was achieved from about 1m away from the border (blue bars in the graph ‘Amazone border spreading with central deflector’).
In order to optimise fertiliser distribution and reduce the incidents of under-applications in some areas, we increased the disc speeds by 80rpm during the AutoTS run.
For the BorderTS run, we reduced the speed by 100rpm and feed rate to increase the rate along the border. This would allow the farmer to operate with the standard side-mounted border spreading system from the tramline when doing the second nitrogen application and means the now more mature crop is not having to be driven on which could break the stems and ultimately lead to a reduction in crop yield.
One frustration with the BorderTS central deflector is that the Amazone-developed mySpreader app doesn’t gives any information on the settings. These are calculated by the onboard software. Another niggle goes to the fact that up to now it is not possible to have the border spreading application verified automatically. Distribution across the working width needs to be verified with rubber mats and the Amazone EasyCheck app.
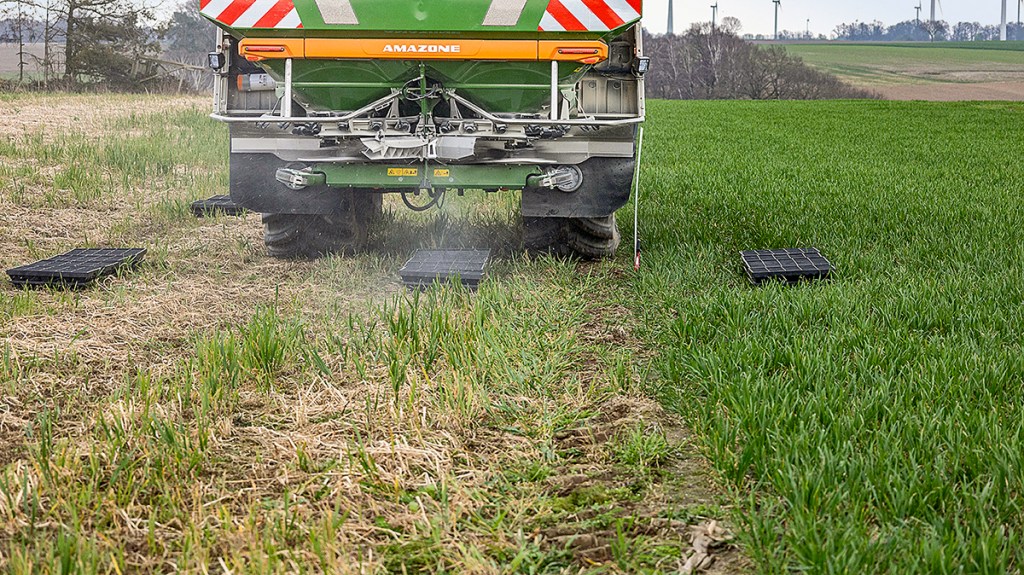
BOGBALLE DYNAMIC
For years, Bogballe has relied on changing the spin direction of the discs for its boundary spreading system. In normal spreading mode the discs rotate from the outside to the inside for a double overlap of the full working width.
But with its new Dynamic border spreading system, you no longer need to reverse the disc rotation from a working width of 27m or more. Instead, the operator simply alters the delivery points on both sides and reduces the speed of the discs. This is done on the move rather than having to hop down and pull the gearbox direction lever.
This Dynamic boundary spreading system produced an excellent and environmentally-oriented lateral distribution in the first border spreading run. Only a few granules landed on the road and the target rate was reached after about 5m into the field.
Yet, in the field area between the first two tramlines the overlapping zone showed a slight underapplication (blue bars in the graph ‘Bogballe: standard border spreading’).
To improve the spread pattern, we upped the spreading width. To do this, we increased the inclination of the spreader from the 4 degrees (specified in the spreading chart) to 6 degrees. We also increased the pto speed by 50rpm.
Furthermore, to end up with a more yield-optimised cross distribution, we upped the application rate by 10% on the side facing the border. This resulted in a near perfect border spreading pattern, admittedly with some of the granules flying beyond the border into the neighbouring field (green bars in the graph ‘Bogballe: standard border spreading’). This would certainly not be an option for applications along roads and watercourses.
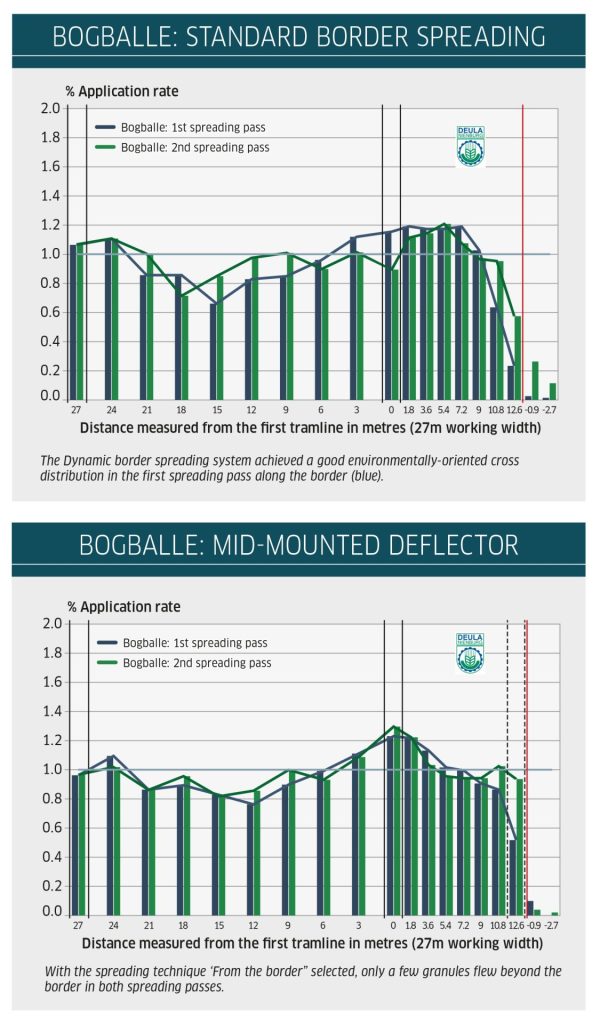
From the border
Border spreading with a deflector mounted in the middle of the spreading system is described as ‘spreading from the field border’ by Bogballe. In this mode, three functions are carried out simultaneously by an actuator; the gearbox alters the rotation direction of the discs; and a small deflector plate moves into spreading position while the right side is blocked. The feed system cannot open.
For close border spreading with the central deflector, the operator drives right along the border in the first pass. For the next pass in the first tramline, they open both sides of the spreader and significantly reduce the disc speed as well as also trimming the application rate.
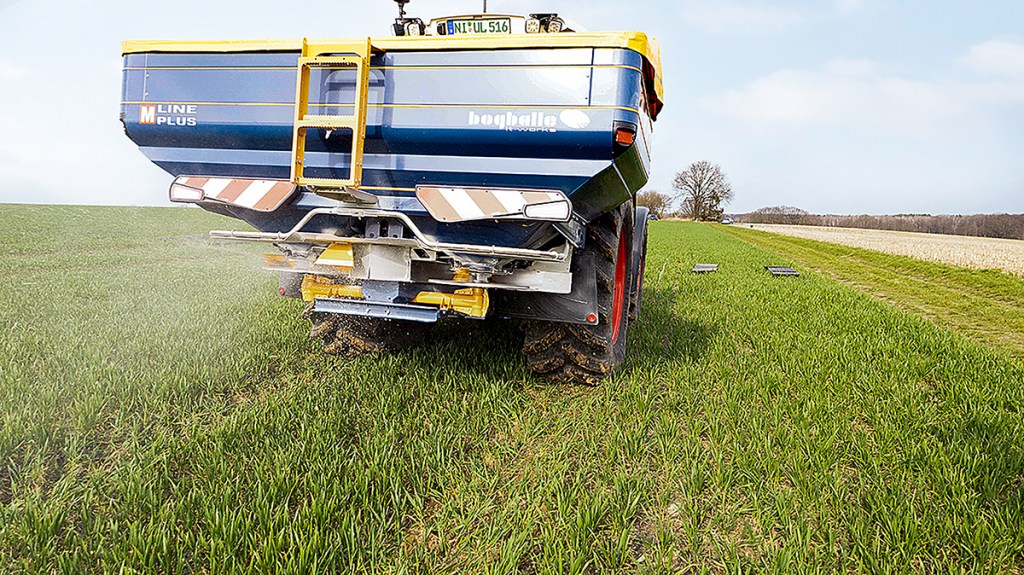
In the first spreading pass, Bogballe’s central deflector achieved a good cross distribution, with only a few granules flying beyond the border (blue graphs in the chart ‘Bogballe: mid-mounted deflector’). The test result was further optimised after we increased the rate by 10% when driving along the border and reduced it by 10% when driving in the first tramline (green bars in the graph ‘Bogballe: mid-mounted deflector’).
Just like Amazone’s BorderTS central system, you also need to switch off section control with the Bogballe when in the first tramline. Alternatively, you can delete the coverage as recorded during the run with the central deflector in place.
Combining the two new boundary spreading systems (Dynamic and central deflector) has only been possible since the 2024 season. The setting recommendations have not yet been incorporated into the spreading charts and have to be requested directly from Bogballe.
Although the interface on the ISObus screen is clutter-free, operators have to concentrate to avoid making errors. For instance, when in central deflector mode, users have to select a different setting for the first three bouts — along the border, in the first tramline and then the second tramline. This does makes the Bogballe border spreading system the most demanding on the operators of the trio of featured machines.
KUHN (RAUCH) GSE PRO
The current version of the GSE boundary spreading system from Kuhn bears the suffix ‘Pro’.
The central deflector immediately catches the eye because of its size. In its working position, it sticks out about 50cm, and out of work is about 30cm. So, you need to be careful when reversing and when filling.
The central deflector has a large vane and three studded splash plates that protrude into the flight path of the granules to optimise distribution at the first few metres.
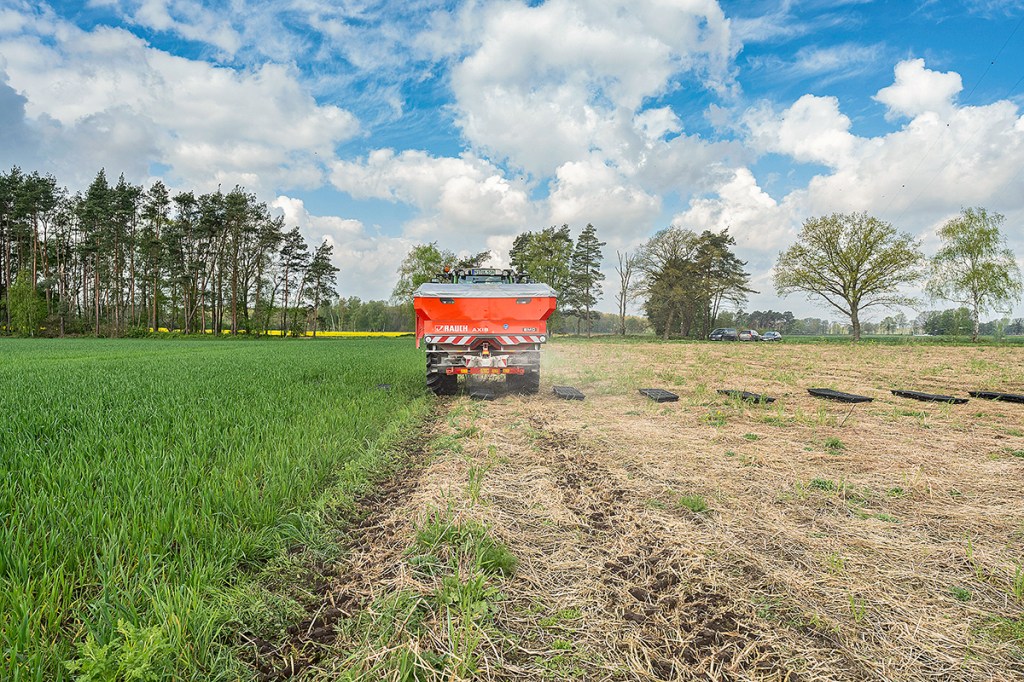
Setting up the boundary spreading system with the mid-mounted deflector only involves minimal changes. The user only has to adjust the metering aperture to alter the amount that the spreader should place at the border. The adjustment recommendations are shown in the Rauch/Kuhn app. There is no need to change the disc speed or the drop point, and the system doesn’t even need to be integrated into the onboard computer’s software.
The central deflector on the Kuhn has a mechanical position indicator as standard. In our opinion, the optional electronic position sensor should be fitted as standard on the ISObus spreaders. Otherwise, the operator may forget about the central deflector and leave it in its working position for normal spreading.
For regular border spreading, the hydraulic Axis H fertiliser spreader has the disc nearest the border operate at a reduced speed and the drop-on point altered. With this system, around 10% of the target rate landed around 1m behind the border in the first spreading pass (blue bars in the graph ‘Kuhn: standard border spreading’). We then optimised the settings to be more environmentally friendly by reducing the disc speed by 100rpm on the border side and the drop point from 6.0 to 5.5.
To make up for the reduced spreading width, we also increased the rate that was applied by the border-facing disc from 20% to 23%. This led to a steep decline in the spreading pattern: no granules were found one metre away from the border. Such a throwing arc would be perfect even for a watercourse application but would mean less yield on the four metres along the margin.
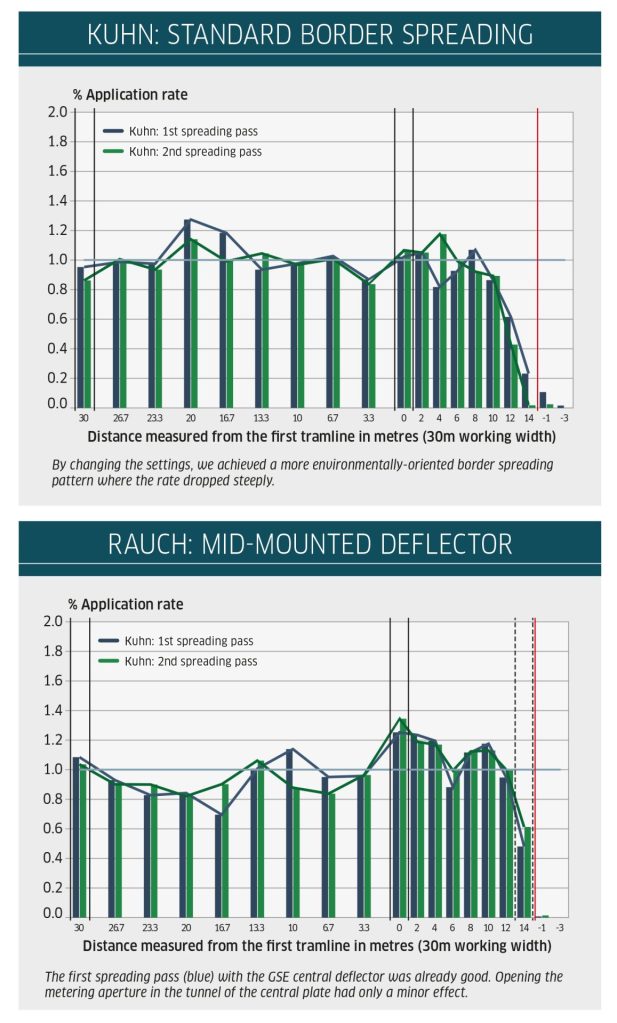
Good first time
Kuhn’s system also produced good results in the first spreading pass when using the mid-mounted deflector. This did not apply, though, to the region between the two tramlines next to the border and to the rate applied right next to the border. To optimise the results (blue bars within the graph ‘Kuhn: border spreading with mid-mounted deflector”), we increased the speed slightly on the disc facing the field and opened the metering aperture in the delivery system of the GSE completely.
Unfortunately, opening the aperture only slightly improved the distribution across rows on the field border. Nevertheless, the result was good because around 60% of the target rate landed just one metre away from the border. Those who want more, can reduce the drop-on point to increase the material in the delivery system.
Drawback is that section control will lead to a 2.0m overlap of the spread patterns, which in turn triggers the unwanted shut-off of one section.
Summary
This test comparison of the various systems produced a clear winner: If set up correctly, central deflectors apply the exact targeted rate just 1.0m away from the border and, at the same time, throw almost no fert granules beyond the edge of the crop. This sets new standards in broadcasting fertiliser.
Farmers should also check out the lateral distribution at the field boundary. With the right planning, they can keep plant damage and any extra effort for boundary spreading to a minimum.
TIPS FOR OPTiMISING BORDER SPREADING SETTINGS
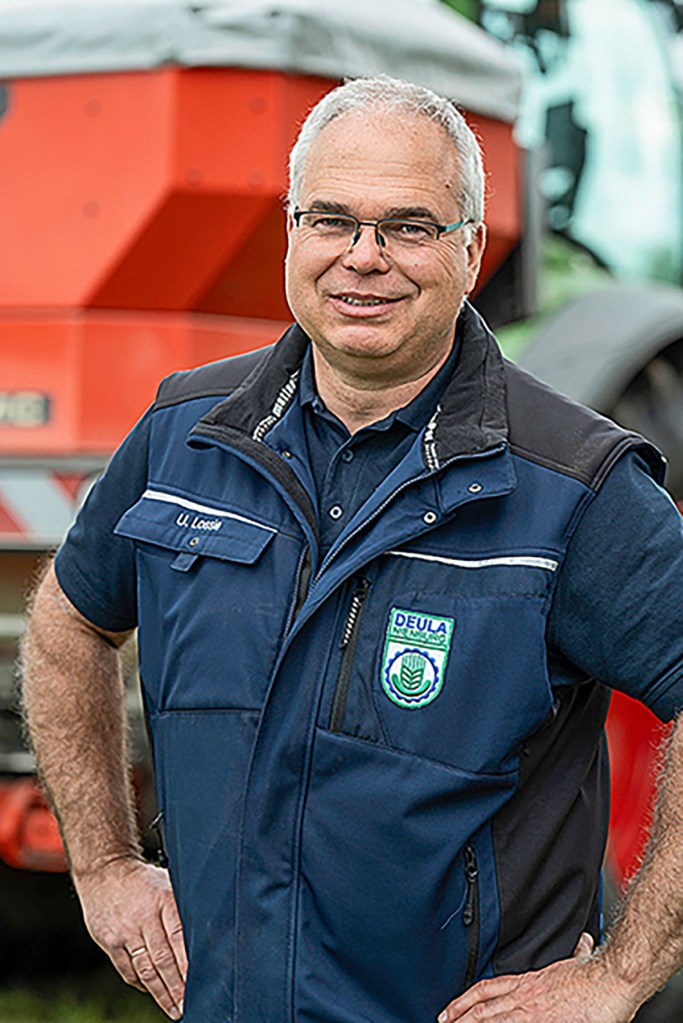
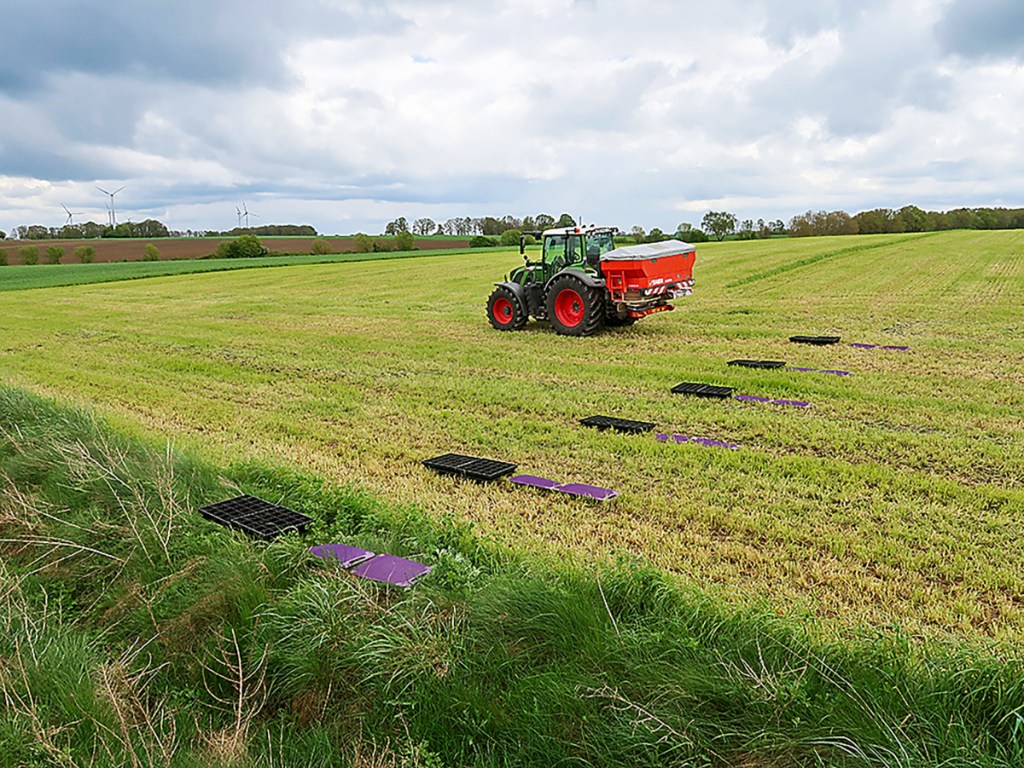
Verifying and tweaking the settings for spreading patterns along the border is more important for accurate border spreading than the hardware. And this takes more than just watching from the seat in the cab. A set of trays or mats for measuring the lateral distribution should be part and parcel of the spreader toolbox on every farm.
Deula Nienburg has tray-use reccs that are easy to follow: Contrary to normal spreading procedures it is necessary to optimise the broadcaster for in-field spreading. This is done with a set of calibration trays. This step is necessary, because any change to the settings can affect the pattern along the border. After the machine is set up for in-field application, place at least six trays or mats along the boundary, placing one tray about 1.5m beyond the border and one about 1.5m within the boundary.
Make sure you equally space all of the trays all the way up to the middle of the bout. It is good to know just how accurate the boundary spreading system actually is across the last few metres up to the border. Only when you know what you are dealing with can you improve the distribution across rows either by using a central deflector or, alternatively, by using a liquid fertiliser nozzle of a different size.
As you optimise the settings, you should always observe the following sequence:
If too much fertiliser was thrown beyond the border, move the outer deflector back towards the middle, reduce the speed on one disc and reduce the drop point.
If there is too little fertiliser on the inside of the border, move the outer deflector farther outwards, increase the speed of one disc and increase the drop-on point on one side.
If there is too much fertiliser next to the first tramline, reduce the rate on the side facing the border. If there is too little fertiliser next to the tramline, increase the rate on the side facing the border.
If you are unsure about the adjustments, ask the manufacturer’s service tech.
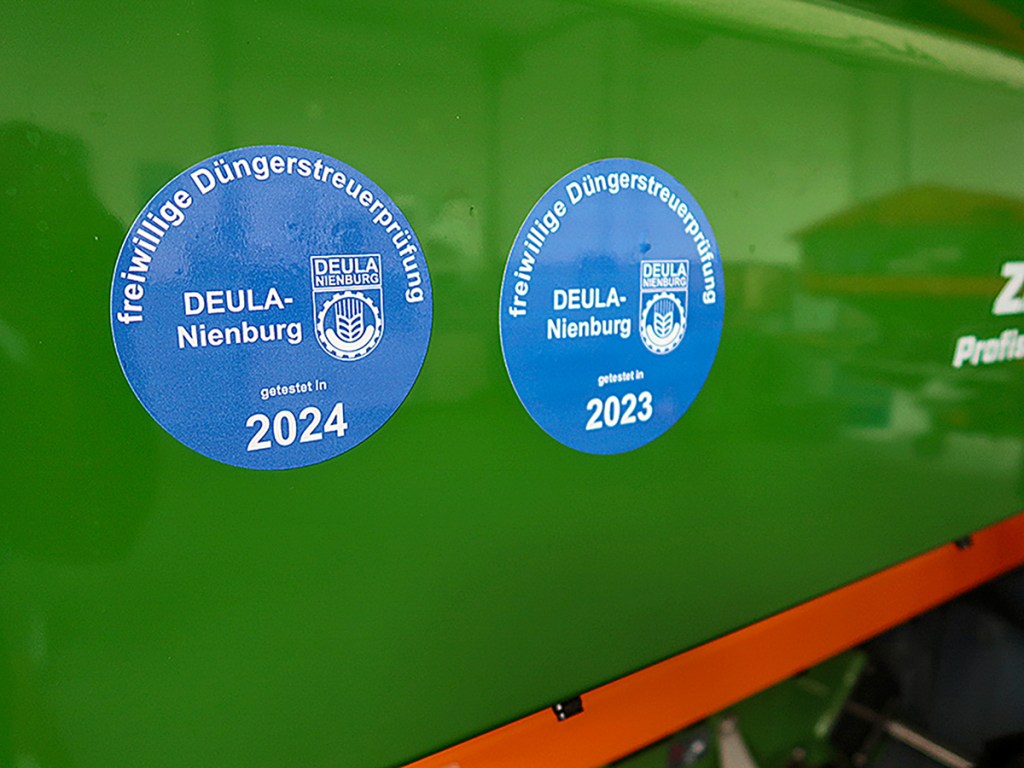
Ulrich Lossie, Anja Böhrnsen
For more up-to-date farming news click here and subscribe now to profi and save.