The UK is an important market for Bredal’s lime and fertiliser spreaders, with the K105 being the most popular model. We’ve been to Denmark to see how it, and other models, are made and tested.
NEED TO KNOW:
- The first Bredal lime and fertiliser spreaders were the B46 and B50 in 1946.
- The company also makes salt and sand spreaders.
- 70% of production is exported.
- Lime spreaders modified for handling sand at construction sites account for a lot of the 30% of machines that remain in Denmark.
- Germany and the UK are the most important destinations for Bredal spreaders in Europe, followed by Ireland and Norway. Australia is the number one export market.
- The K105 is the best-selling fertiliser/lime spreader in the UK.
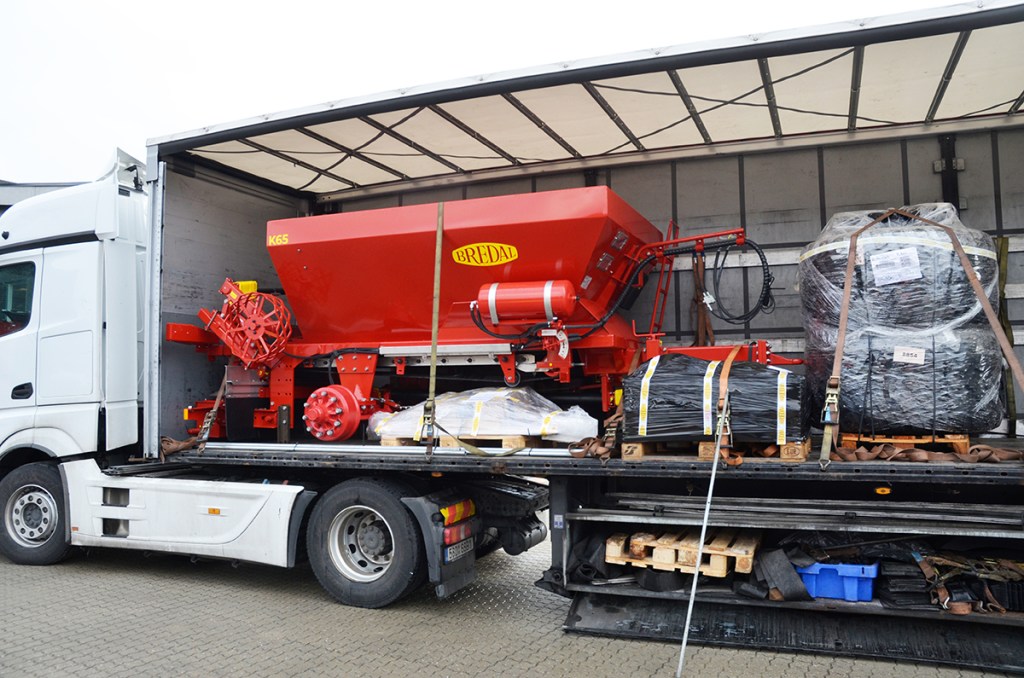
There are five big names when it comes to fertiliser spreader manufacturing in Europe; Amazone, Bredal, Bogballe, Rauch, Sky (Sulky) and Vicon/Kverneland. There is a very good reason for this, comments Michael Lond, export sales and product development at Bredal and Bogballe. “It looks simple, but is very difficult to do right.”
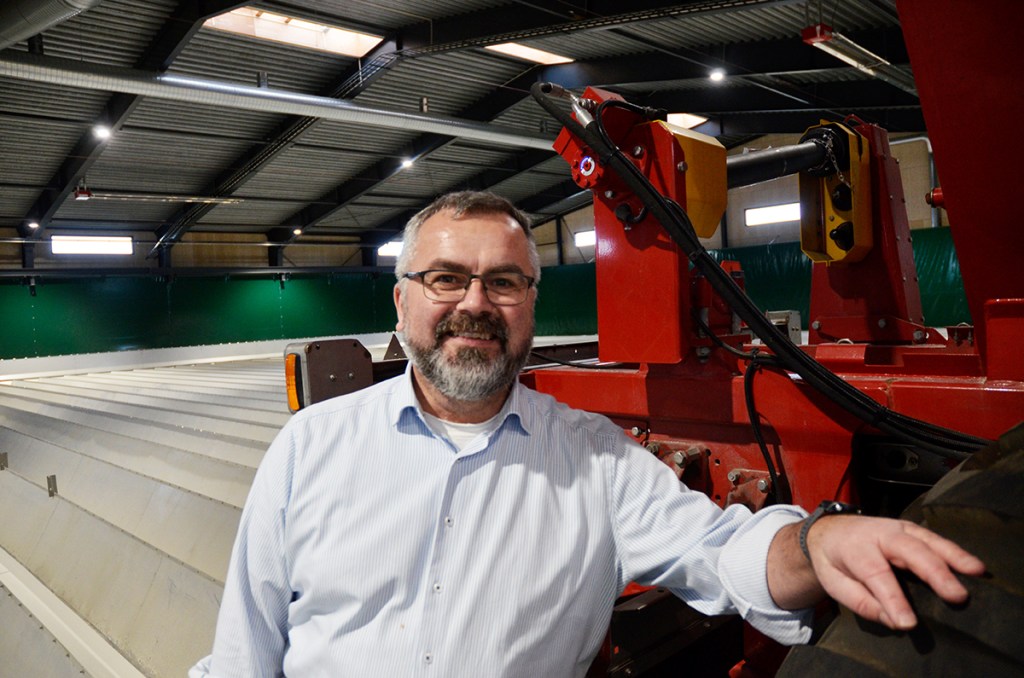
Having previously worked for Bogballe for 23 years, the friendly Dane now covers both brands following the purchase of Bogballe in 2017 and Bredal in 2023 by Erhvervsinvest who also owns Danish slurry specialist Agrometer.
The two brands give the Danish investment company an enviable production capacity for fertiliser and lime spreaders. With a total production area of 38,600m² spread over three nearby locations, the area is known as the Silicon Valley of fertiliser spreaders. The combined workforce of 109 is split between three factories – 64 at the Bogballe plant and 45 in Bredal’s current two facilities.
Separate…for now
Both companies continue to operate independently, and while the acquisition of Bredal seems a bit odd, it adds lime spreaders to the mix, something that Bogballe does not have.
This is not the first time the two companies have joined forces. Some older readers may recall that Bogballe was responsible for exporting Bredal products (also to the UK and Ireland where both companies have a long history with KRM and Atkins respectively) in the 1970s/early 1980s.
The integration of the two businesses is an ongoing process that is still in the honeymoon phase. But the first visible signs are there, such as buying in components. Hopper covers for both brands are sourced from the same supplier. So too are weigh cells, actuators, electro motors and ISObus controllers.
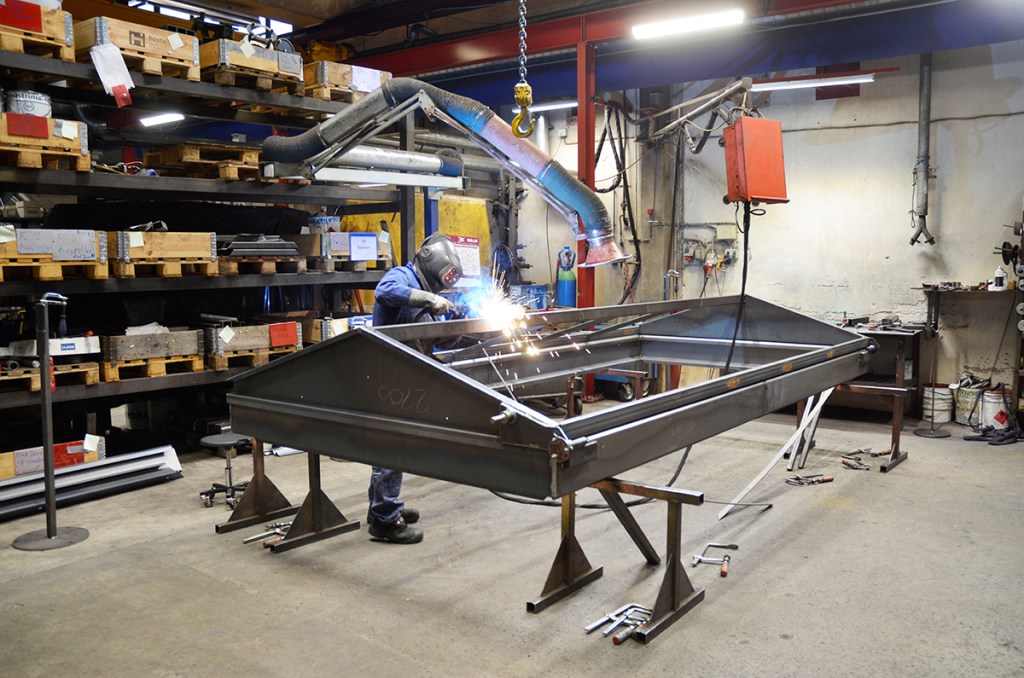
A number of Danish manufacturers took their name from the village in which they started. Typical examples include Thyregod and Harso, and both Bredal and Bogballe are names of villages. Bredal had a production plant in their namesake village until 2012, when it relocated 5km to the current site on an industrial estate, not far from the Danish town of Vejle.
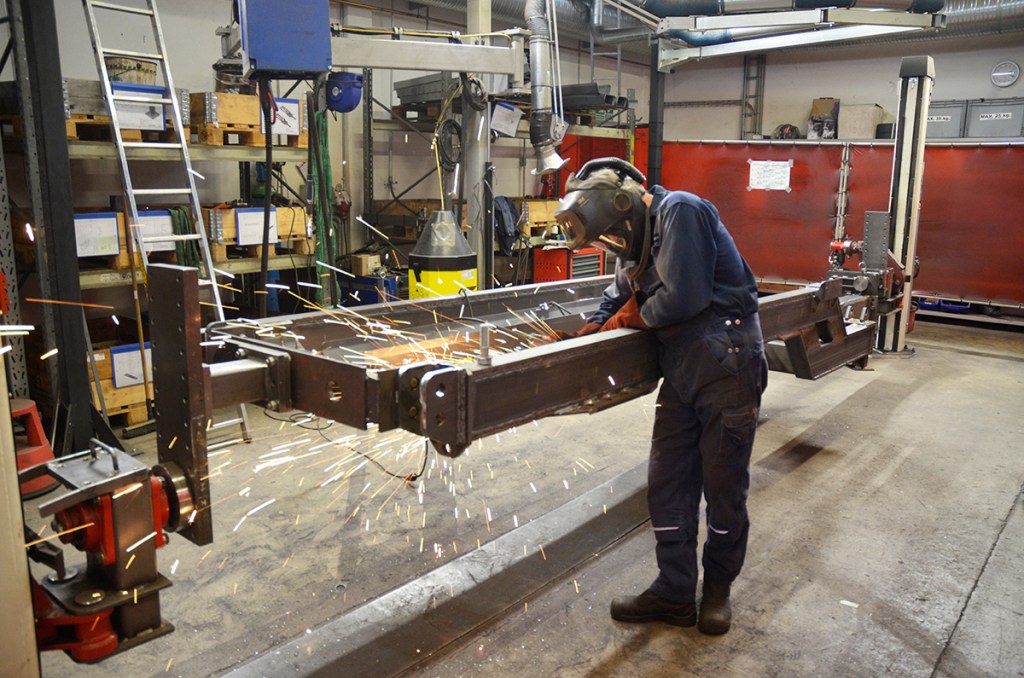
Steel parts made in-house
A fertiliser/lime spreader begins at Bakken, a separate Bredal building 4km from the production hall. In the 6,400m² fabrication buildings, sheet (thickness 2.0-30mm) and box-shaped steel is cut to size by fibre optic lasers, pressed and welded into recognisable parts, such as such the chassis, hopper, hopper extensions, etc.
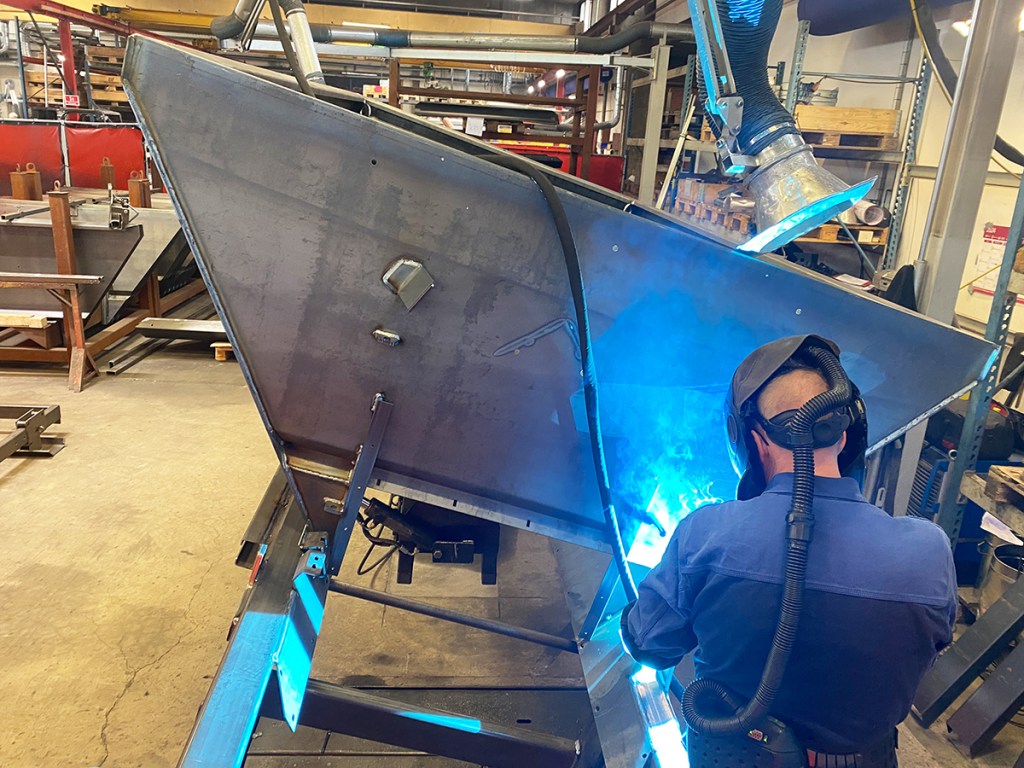
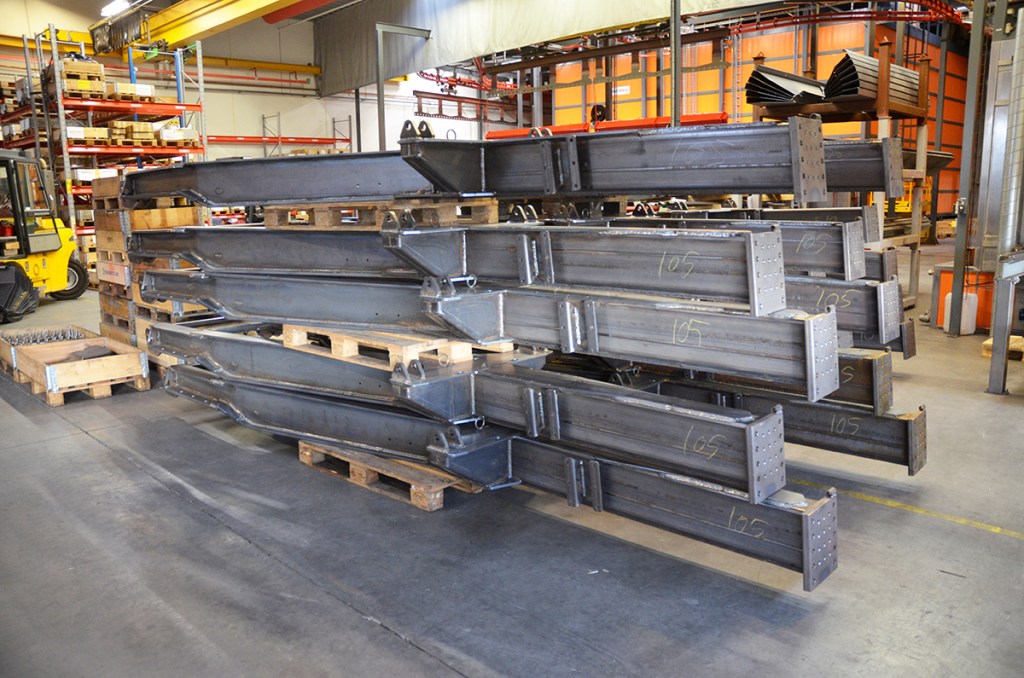
At the end of the process, parts are trucked to the 9,500m² production hall, where the current portfolio of trailed K series fertiliser/lime spreaders (2.5-20m³), mounted F4 (1.5-4.0m³) and trailed F8 and F10 fertiliser spreaders (5.7-10m³), and K-XE are built.
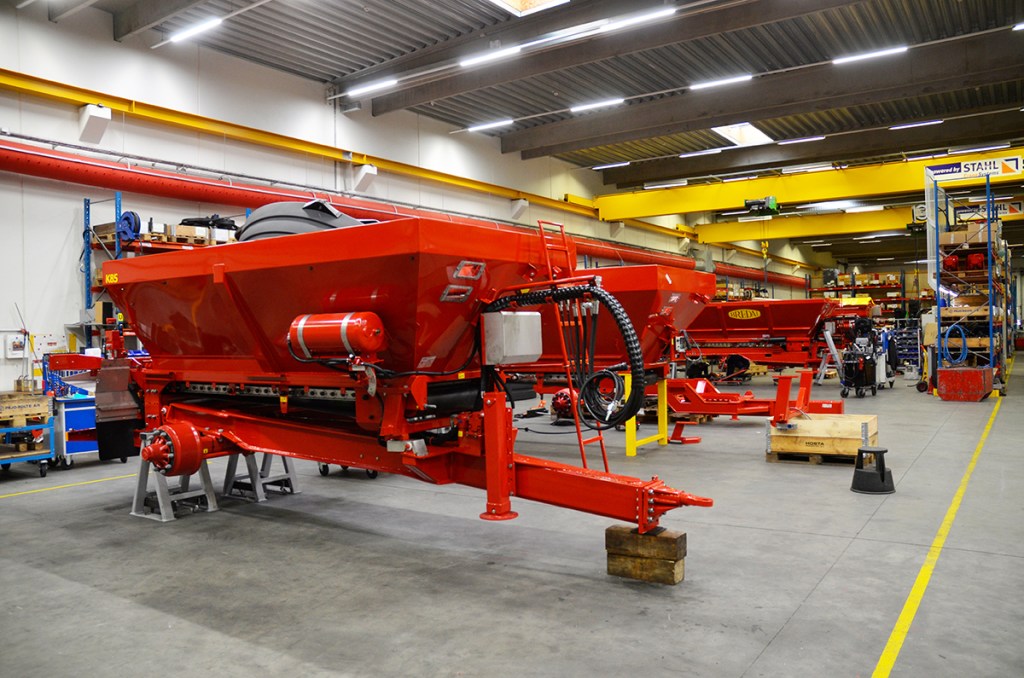
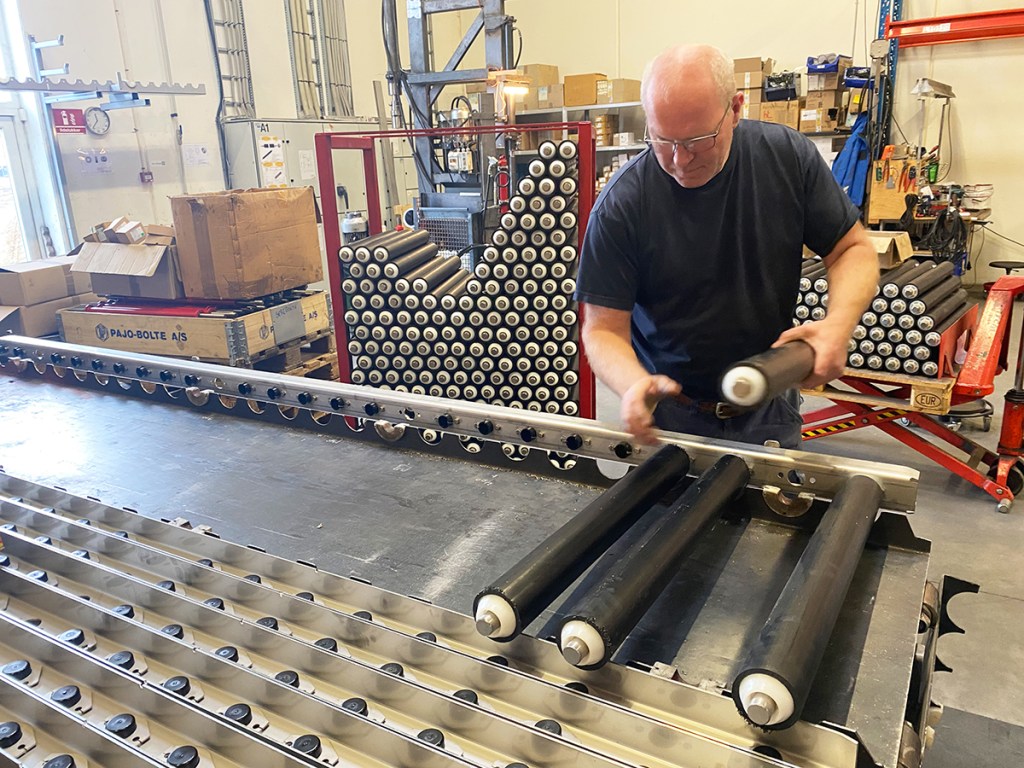
There are numerous reasons why Bredal and Bogballe spreaders continue to be assembled at the two locations. One of which is that Bredal’s trailed spreaders need 5.0t cranes to lift the heavier trailed components, while the Bogballe plant has smaller cranes.
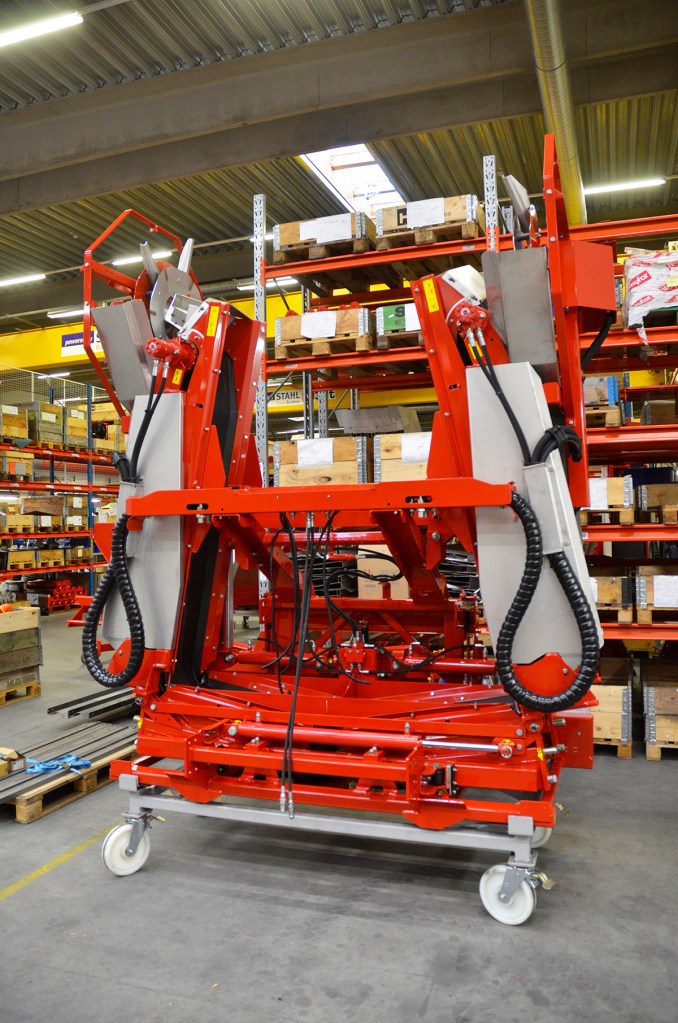
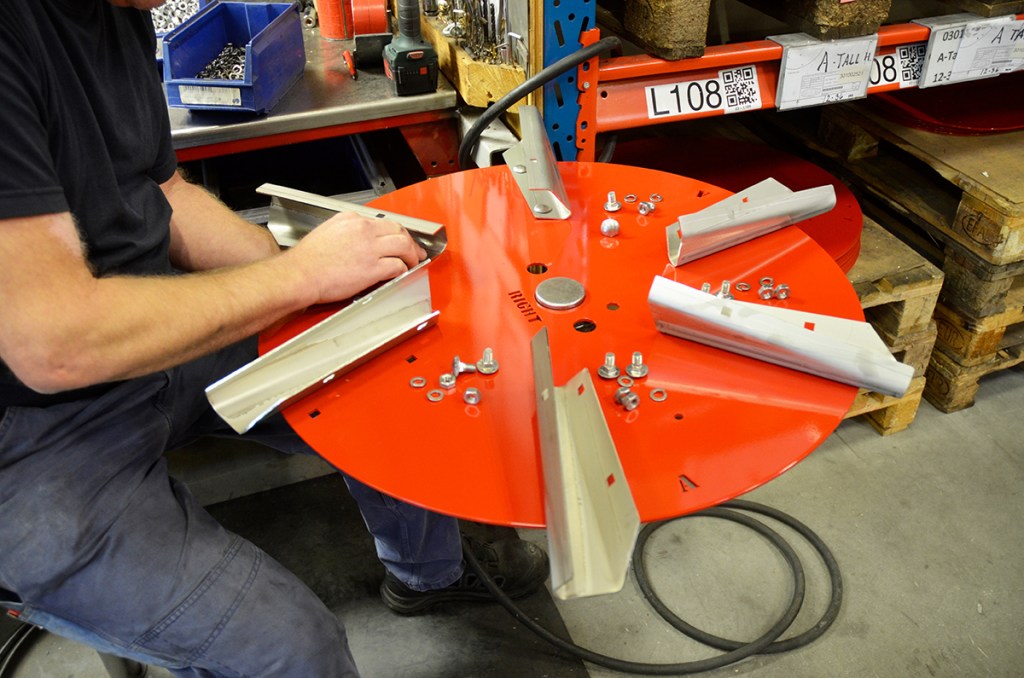
To my mind, one of the most interesting parts of the assembly process is the paint shop. Believed to be the largest shot blasting and powder painting plant in Northern Europe, it is large enough to accommodate a 17m³ hopper. Preceded by the shot blasting process, it depends on the part, but this takes 8-10 minutes and generates a split-second surface temperature of 800°C.
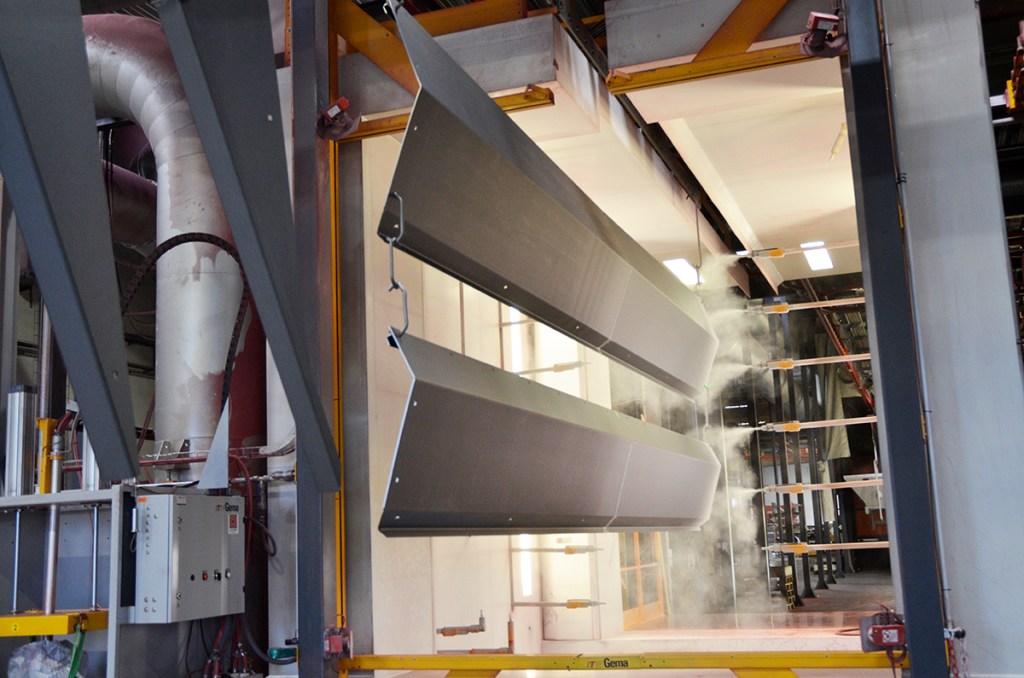
All parts then travel through the automatic powder coating process. Suspended from a network of rails, the first sees a barrage of nozzles add the 60-micron epoxy polyester primer. The part is then transported to another booth where highly skilled workers manually touch up all parts that the nozzles cannot reach.
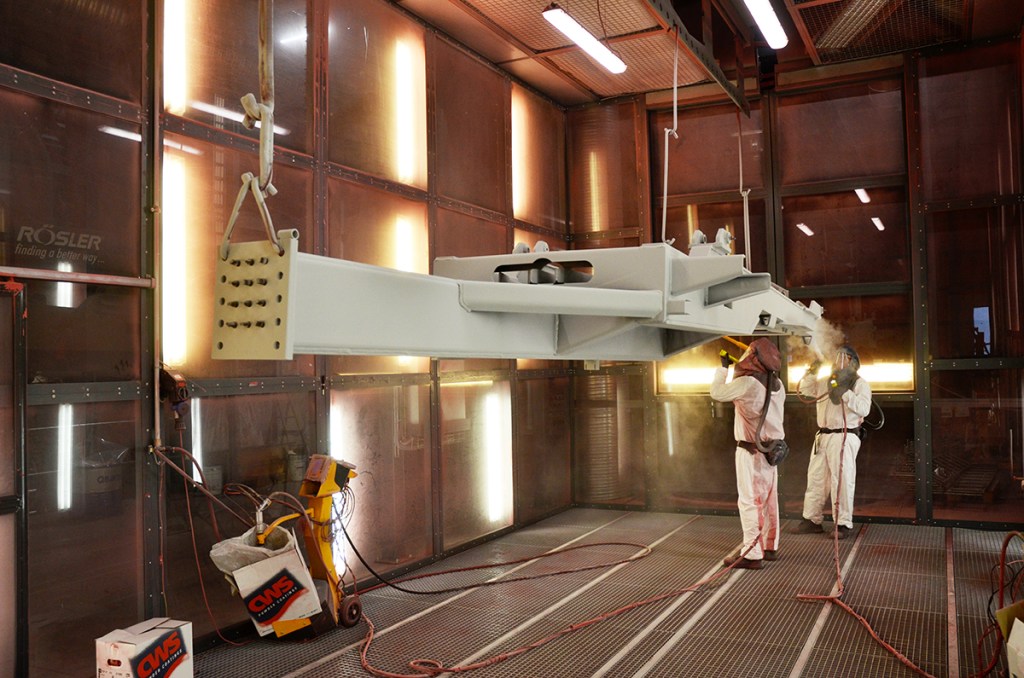
Spreader frames, hoppers, extensions, etc, then spend around 90 minutes in a 200°C oven, after which they are allowed to cool before the process is repeated, this time with a 60-micron Bredal red top coat.
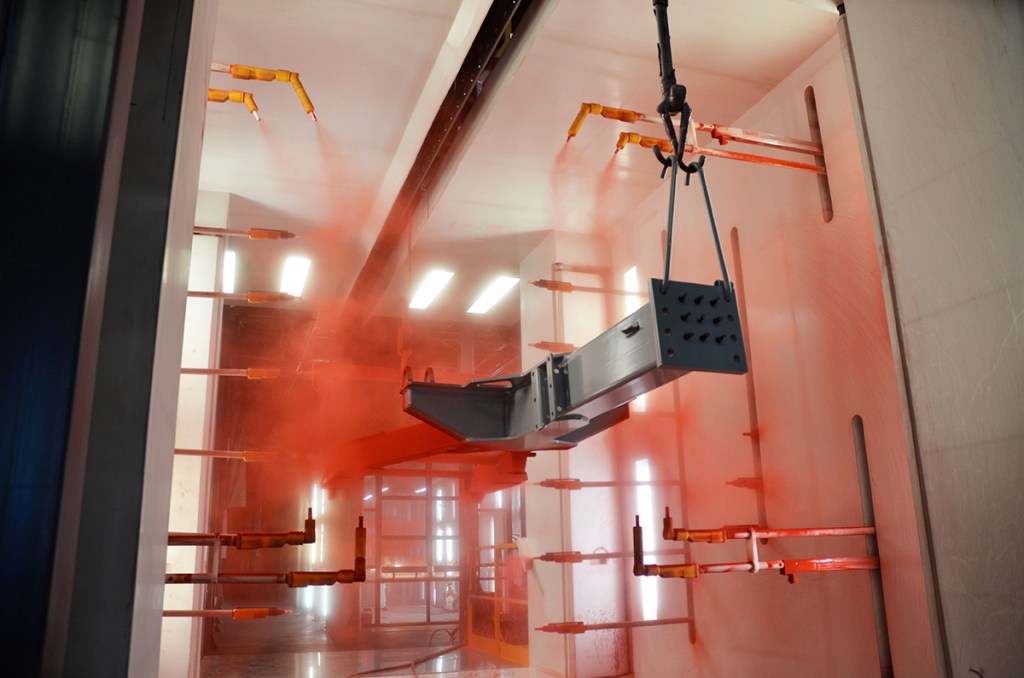
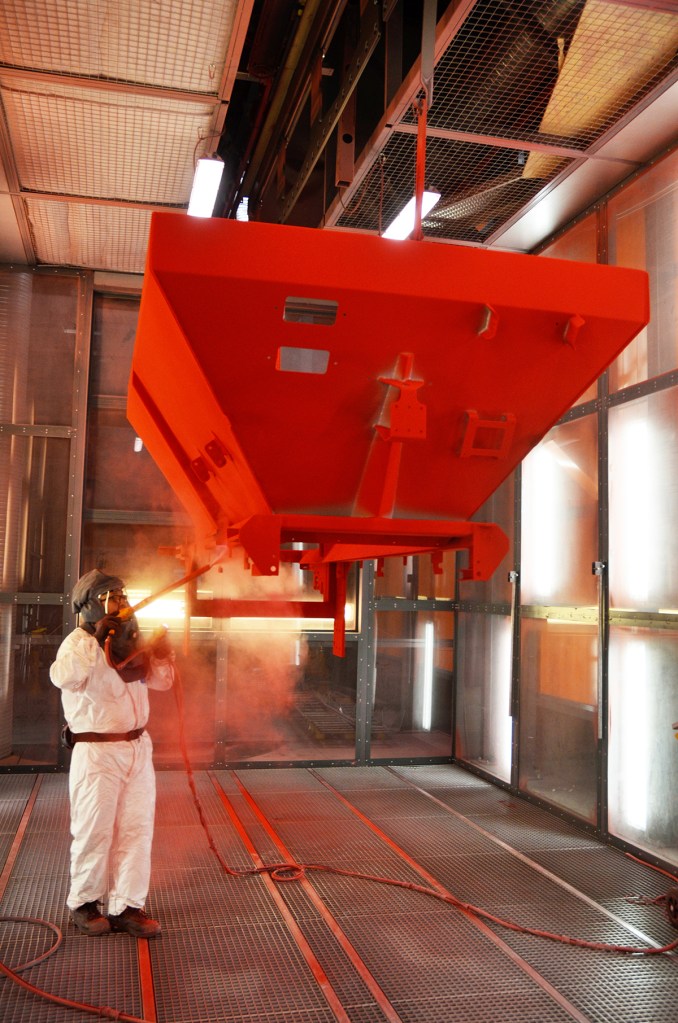
There is plenty of space to assemble four trailed machines at the same time, and when a chassis is lowered to the floor it stays there until the machine is finished. It depends on the model, but this takes from two to three days.
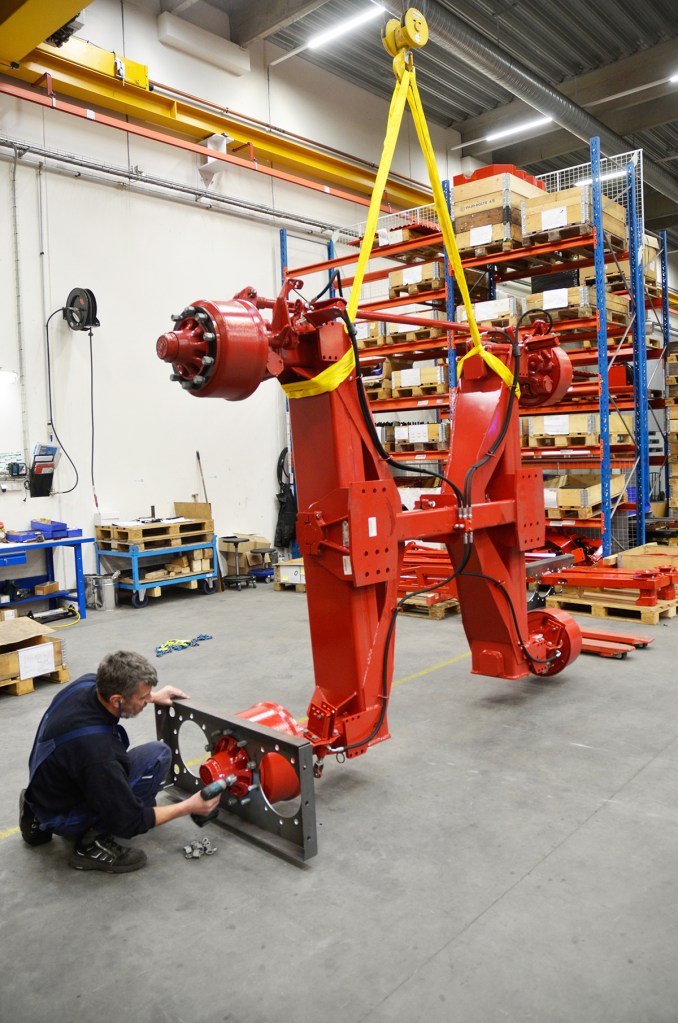
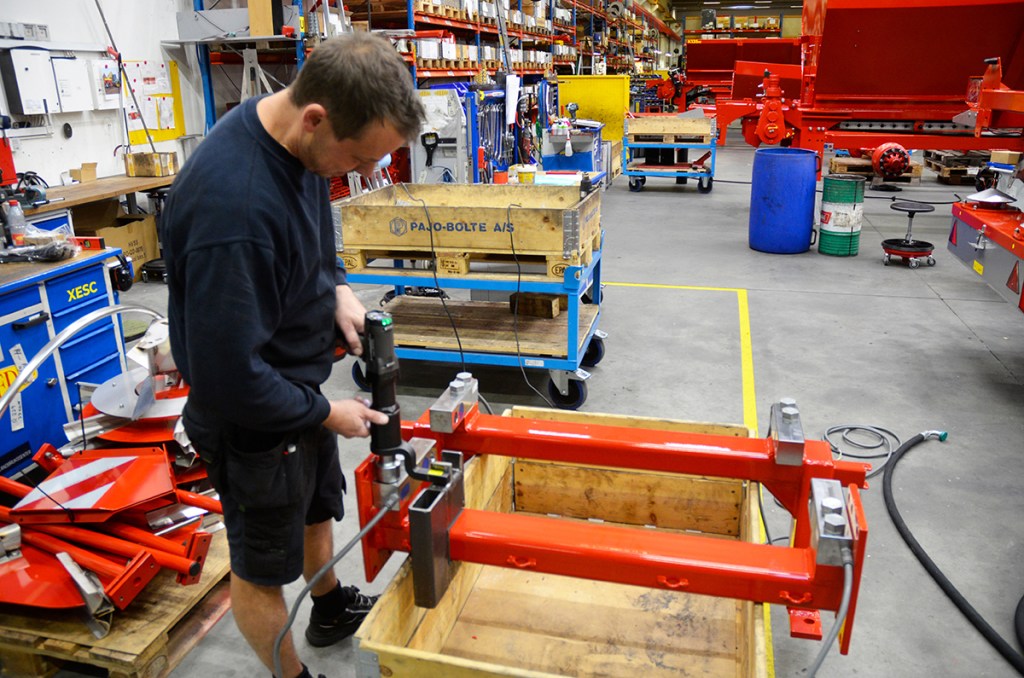
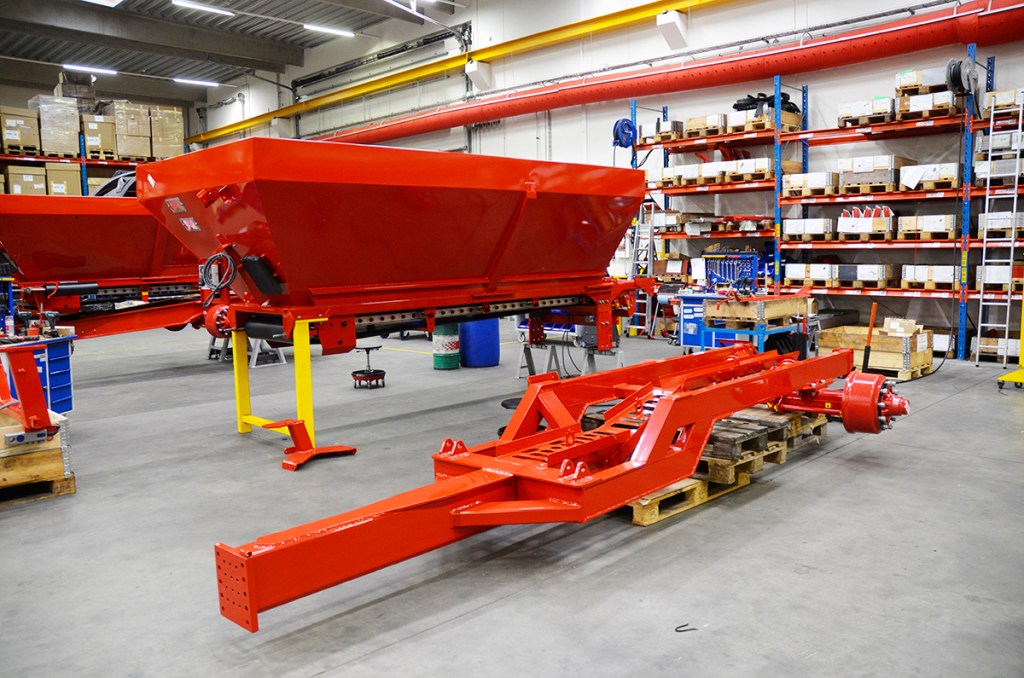
Test hall
Michael reckons that Bredal can learn from Bogballe with precision farming, and that both companies can pool spreader experience to further increase the performance and accuracy of their machines.
Another area where Bredal and Bogballe work together is with testing facilities. Bredal does section control and start-stop on field inclines (up to 90 degrees) inside Bogballe’s 3D test hall. Bredal’s 2020-opened 2D test hall gives Bogballe access to highly accurate spread charts.
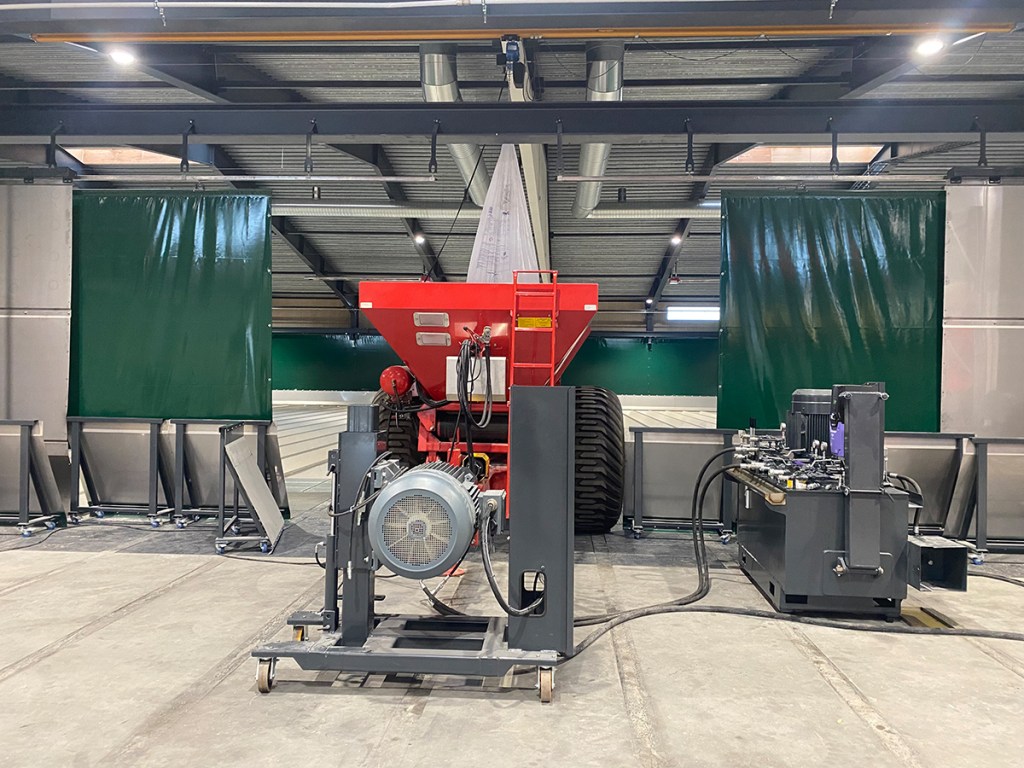
Anyone can make a fertiliser spreader, comments Michael. “The hard part is in ensuring that it works accurately in a wide range of different fertilisers.”
To do this is expensive, and the 2020-opened 3,000m² two-dimensional test hall left the company with no change from €4 million. “Fertiliser is one of the highest input costs for an arable farm. If you do not have a test hall then you cannot sell spreaders.”
Each of the 70 x 1.0m-wide trays inside the 40m-long x 70m-wide test hall equate to a test tray of 40m².
The hall does not test newly assembled machines. What is does do, though, is each time a new fertiliser spreader range is released it is tested to create a spread chart. Also, when a new fertiliser is released, it is also tested with a model from the F and K ranges.
The discs on the K65 we saw was testing a new nitrogen fertiliser for the coming season in the UK, only needed to be activated for eight seconds. “We only need 1.5t of fertiliser to create a complete spread chart for all of our machines.” Fertiliser from each tray is automatically transported to the side of the building and weighed. The system is self-emptying.
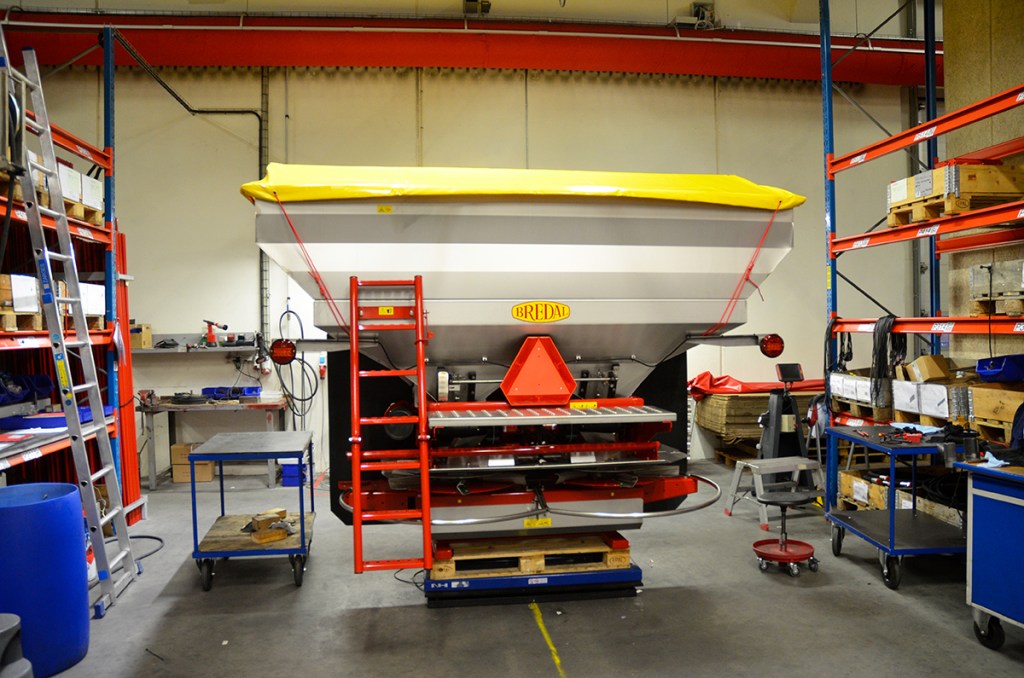
Upping the numbers
Bredal is also keen to export more machines, and Michael reckons there is a big initial potential for the company in North America, followed by South America and Africa.
With Bredal and Bogballe belonging to the same group it can offer potential importers a wider range of products. For example, Brazil is a big market for mounted and trailed spreaders. “Having both makes us interesting for a strong partner.”
Capacity is currently the limiting factor to making more spreaders as anyone that has ordered a new Bredal spreader will know. Delivery times are currently upwards of 12 months. The plan is to reduce this as fast as possible to six months.
“We need to find more capacity inside the production and fabrication buildings either through more people or more machines. There is plenty of space for both, and we could add more staff to the day shift.” The 40 staff in the production hall clock up a 37-hour week from Monday to Friday.
Our tip is to expect more of both in the future. In fact, a welding robot will arrive early this year. Currently, all chassis are manually welded and it takes two full days to do one. The new robot, which will probably start with a K105 chassis, will not only reduce this to six hours, but also do it at a more consistent quality. “Steel plates in the fabrication building are cut to size by two laser robots so we are ready for a robotic welder.”
Steven Vale
For more up-to-date farming news click here and subscribe now to profi and save.