Since the takeover, Amazone and Schmotzer have been stepping on the development gas — new features include a linear side-shifting frame and a smart camera with slope compensation. The livery colour has also changed since our driving impression, with green replacing blue.
KEEPING IT BRIEF
- In addition to the parallelogram sliding frame. Amazone introduces the linear sliding frame.
- Also new is its own SmartVision camera system.
- We used the hoe in three different crops without having to alter the settings.
Shortly before the Amazone takeover in 2019, Schmotzer had presented the Okio camera system, which was intended to advance its automatic row-finding technology in collaboration with an external supplier. But the partnership never really got into its stride, so Amazone then switched to its current arrangement of predominantly going with the fourth-generation Culticam cameras from Claas E-Systems.
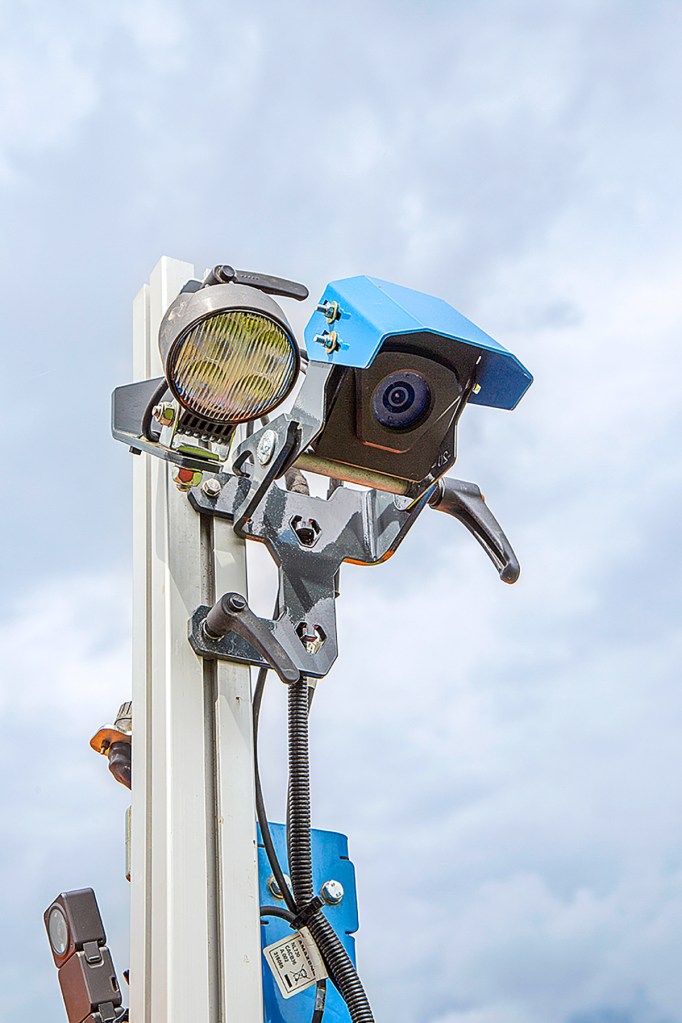
Even though Amazone now has its own in-house SmartVision system, the company will continue to have the Culticam in its range.
With SmartVision, the machine manufacturer now wants better integration and to be more in control of the features and functions such as the all-important side-shift control, slope compensation and how the operator interface is laid out.
There is also the subject of cost: by keeping the electronics in-house, the likes of adding a second camera unit for row guidance will be around half that of the bought-in Claas system. Amazone can also include the likes of LED lights as standard, which often cost several thousand euros extra if relying on an external supplier.
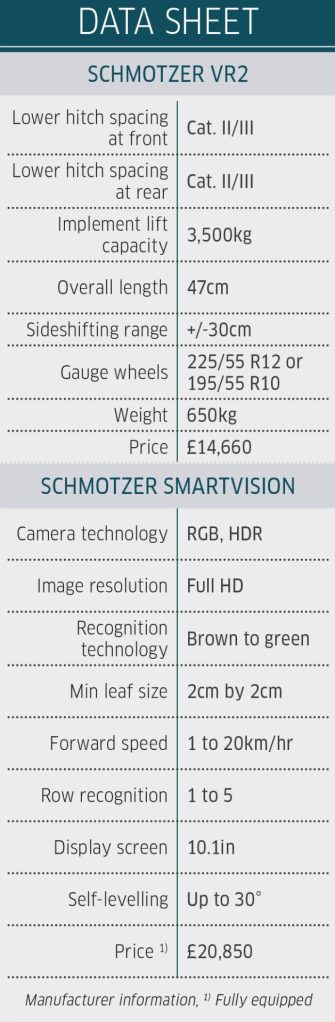
Protecting crops
The firm’s new camera system boasts an integrated self-levelling system, unlike the existing camera side-shifting platform on which the operator had to manually correct drift/crabbing movement on a side slope. Now, since Amazone’s developer has included a tilt sensor, the on-board electronics can automatically correct any drift. Amazone specifies a factory-installed correction of 2.2cm per 5° slope gradient, which can also be altered on the terminal as an option. Technically, the sensor can detect angles of up to 30° but this isn’t something that would be realistic in most field situations.
A 10.1-inch terminal is used to visually show the row detection and to adjust the camera steering system. Although the system is currently not yet fully ISObus compatible, this will at least be used for exchanging data between the hoe and the camera system.
Button functions can also be transferred using ISObus, allowing you to assign certain tasks to Aux-N buttons. For instance, the side-shift frame can be operated manually from buttons on existing joysticks, whereas up till now this was done from a separate joystick that came with the terminal. For the time being, the camera images cannot be transmitted through the ISObus cable simply due to the amount of data, so a separate cab terminal is kept in place to show the visual control video image.
The menu layout with its handful of sub- menus is the typical Amazone layout, so users of other Amazone kit should be able to pick it up quickly. Apart from the plant size, you generally don’t have to adjust any settings — convenient and will be welcomed by users.
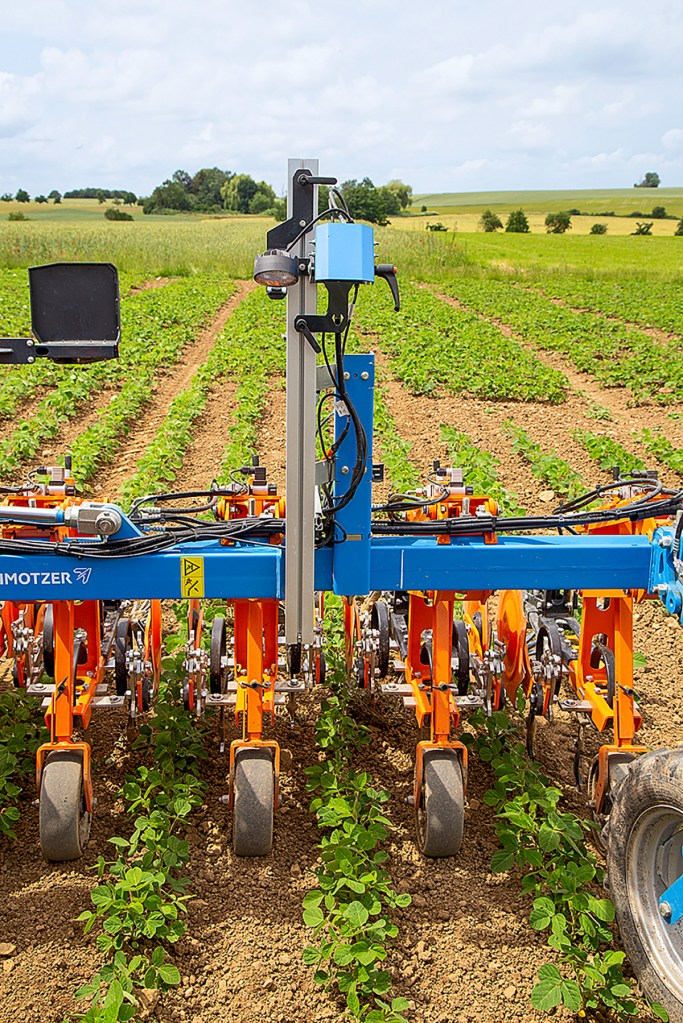
A razor-sharp image
Moving on to the new camera for row guidance, this is a digital camera unit that captures and transmits data in HD quality. The optics recognise the RGB colours and detect the plant rows by evaluating the differences between the green colour of the plants and brown of the soil. If the system doesn’t detect brown ground in a weed pocket, the overall quality of the images will decrease. If the system falls below a preset value, then the side-shift just holds on its current position until the camera unit can distinguish the row again. It is not yet able to detect rows by difference in crop/weed height, although Amazone is considering introducing AI to interpret this data.
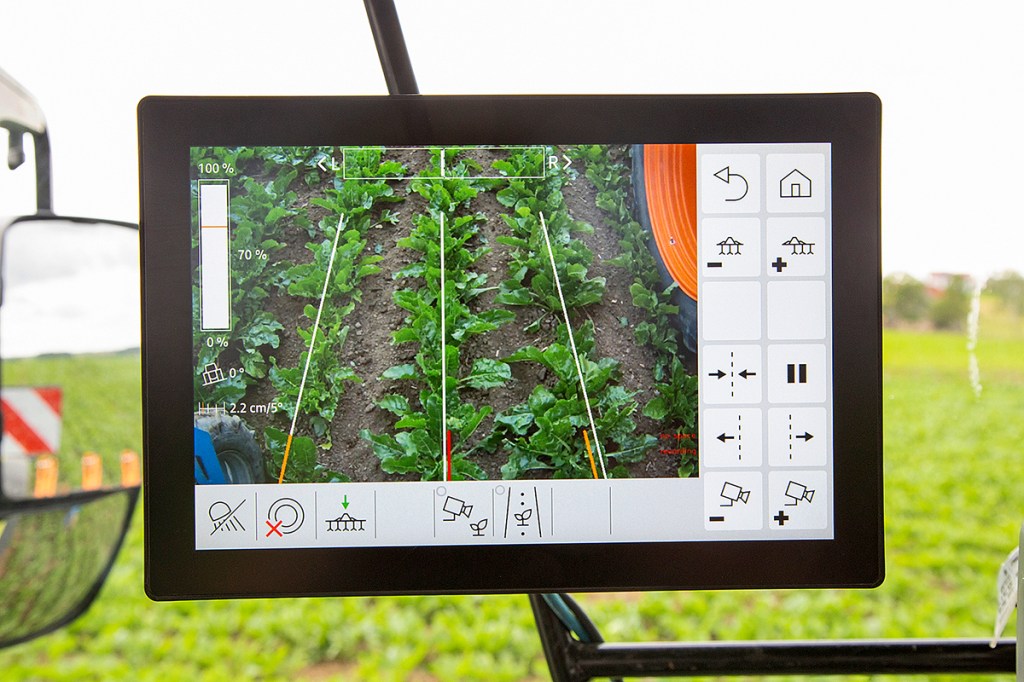
The camera automatically adjusts the colour tone and exposure to compensate for direct sunlight or shading. It is said to have enough computing power to do this at speeds of up to 20km/hr.
Recognising small plants
The minimum detectable leaf size is 2 by 2cm, according to the designers. However, the farm we visited that has been using a pre-series machine was able to weed sugar beet with a leaf size of just 2x4mm at the cotyledon stage. At this size it would be difficult to make out the beet plants by eye, so that’s pretty impressive.
Basically, it is not necessary to alter the height and angle of the camera, unless the crop size varies significantly or the row width is changed. Specific system setting instructions or charts are not provided; you just need to figure it out by ensuring that you can see the selected number of rows on the screen, which can range from one to five.
Depending on the camera height you set, you have to adjust lines on the screen that visualize the expected row lines. This way, you won’t have to measure the camera height. Adjusting the lines on the screen is straightforward, and it’s set to become even easier.
Central frame
Schmotzer has been an advocate of using a parallelogram for its side-shifting platforms, praising the smoother control and easier tractor removal as well as the excellent overview of the cultivating elements. Up until now it has never offered a linear side-shift platform, so this is one of the changes being made by Amazone.
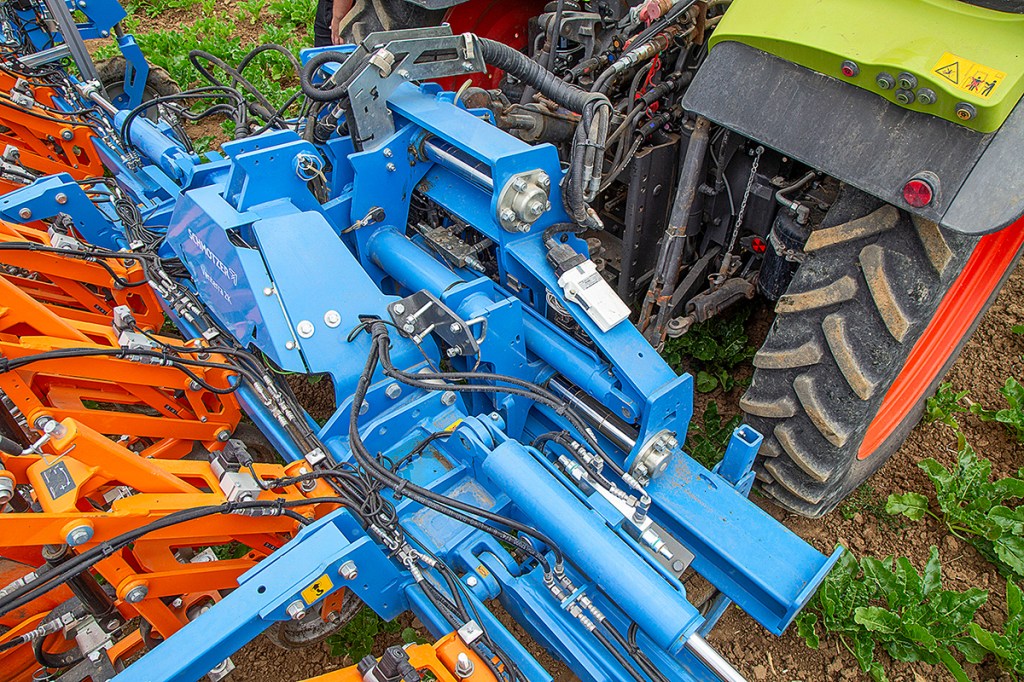
The machine we looked at was the first model from the new series, the VR2. “VR” stands for the side-shifting platform, “2” indicates the two folding elements. A smaller VR1 platform and larger models will follow.
The VR2 is designed for use on cultivation attachments of up to 3,500kg and available in various Cat. II to III tractor coupling categories. The frame itself is sourced from Amazone using the main beam donated by the Precea maize drill, although it is rotated through 90°. This is used to accommodate various modules such as the pneumatic gauge wheels, either in pairs or singles, and a spring-loaded disc for hoeing on slopes.
On the outside, the frame is 2.30m wide and designed for 1.50 to 2.25m track widths. Additional flange points are provided on the sides for extending the frame to an optional 3.00m track width.
Unlike on our pre-series machine, the full-production models will have a larger ground clearance. The side-shifting platform is sold with a frame ground clearance height of 80cm or 100cm … for the weeding of maize, for example.
60cm shifting range
The VR2 slides on 60mm chrome-plated rods, one top and one bottom-mounted shaft. The frame sits on composite-made bushes . All of the key moving points are lubricated from an easily accessible grease bank on the left — great. The total length of the intermediate frame is 47cm.
The hydraulic cylinder that carries out the shifting of about 30cm to either side is positioned between the two sliding shafts. This has a built-in measuring system that detects the current position of the piston crown. Response rate is good.
Speaking of hydraulics, there are various solutions. The entry-level version requires one single-acting spool valve to provide a continuous flow and one free return for the side-shift. There is also the option of lifting out rows hydraulically when coming out/in from an angled headland.
Alternatively, there is a load-sensing option. This comes with a 3.0-litre oil reservoir so the side-shift can respond more instantly than it can with a load-sensing supply. The reservoir capacity ensures that the platform can move twice to the left and right; when empty, the load-sensing system tops it up again.
Load-sensing can also connect the pump to an optional front tank from Amazone — for example, for band spraying.
Costs for the VR2 without load-sensing will be £14,660, while the SmartVision camera is £20,850 including self-levelling system and LED lights. Price for a second camera has not yet been finalised.
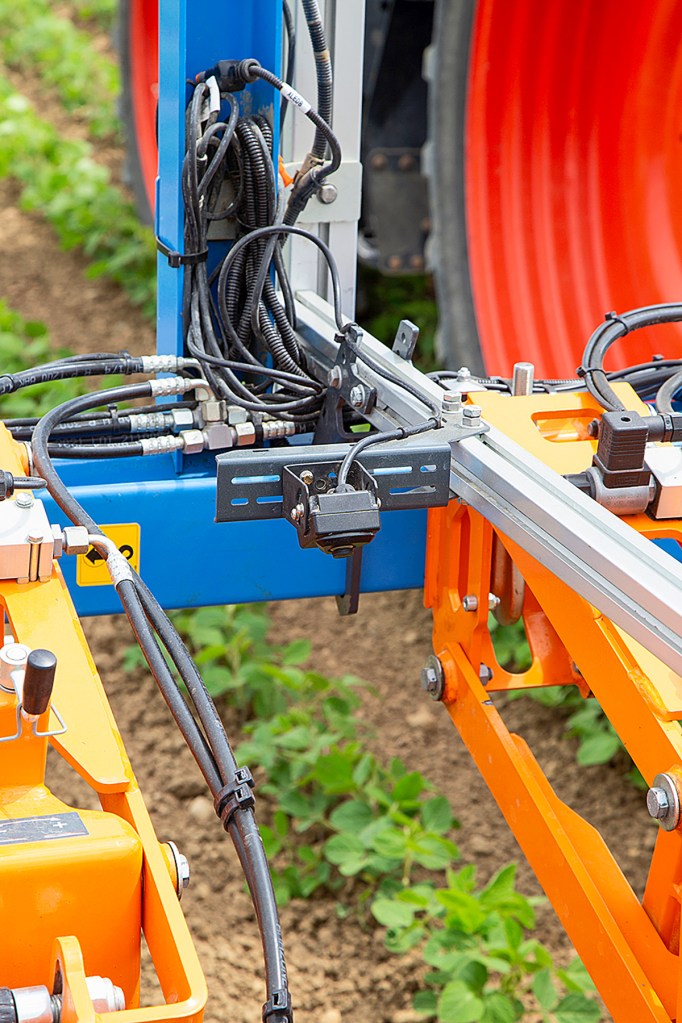
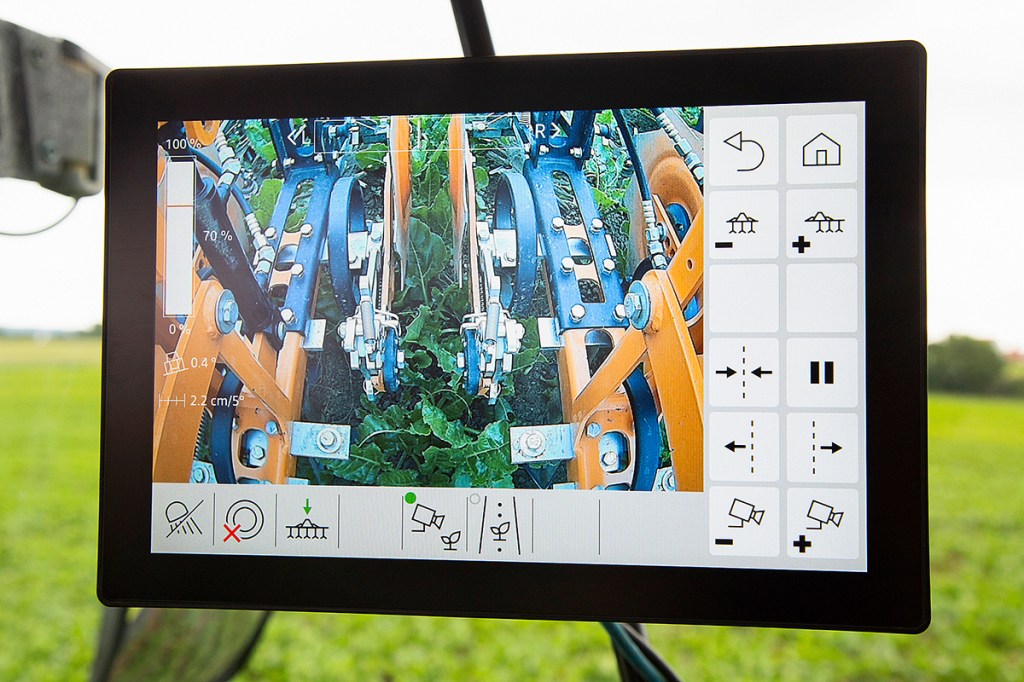
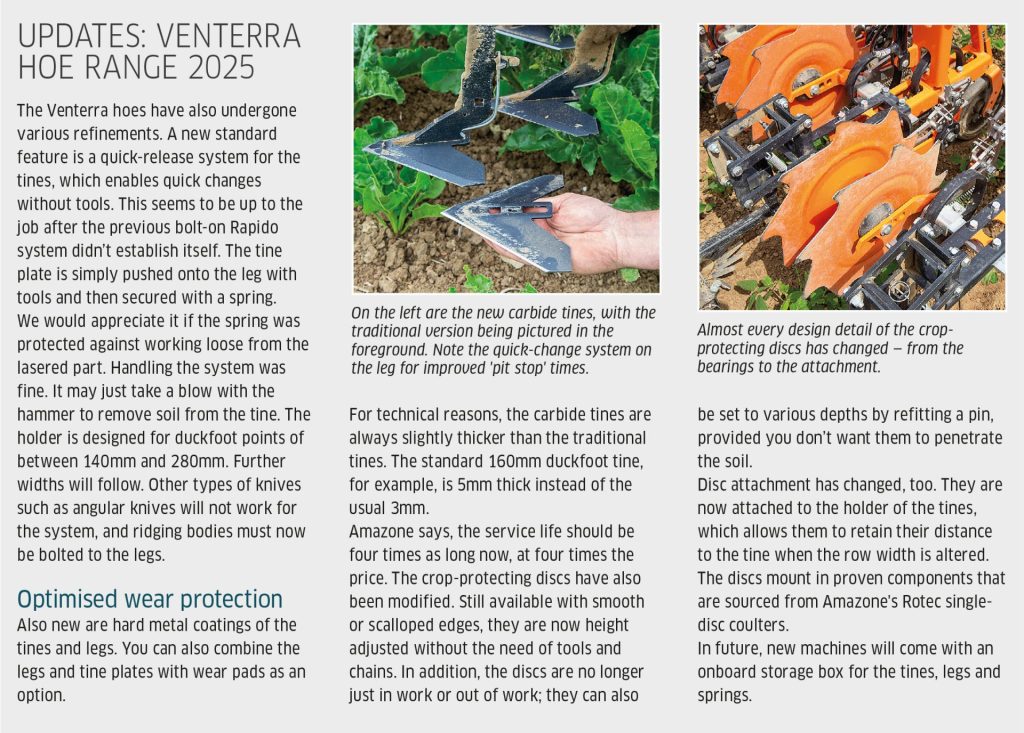
Other details
- Oil requirement for the VR2 is around 15l/min. Section Control on the hoe needs another 35-45l/min.
- The lift-out signal for the sliding frame comes from the hoe.
- The electronic components are housed in the left sliding frame; the hydraulic valve chest is on the right.
- Amazone plans to offer camera software updates at least once a year.
- The camera can save short video clips for service purposes.
- A digital camera can be integrated as an option for visually monitoring progress.
- A second camera unit makes sense for larger working widths, for less uniform crops rows and where there are fields with varying contours.
Summary
With a new side-shift frame and its inhouse-developed camera, Amazone increases its range of hoeing equipment, which clearly reflects its own DNA.
We were able to hoe maize, sugar beet and soya beans without any hiccups and without changing the settings. The response rate is pleasant and the user interface intuitive. There’s no green-in-green detection feature at present, but this is clearly something that’s envisaged for the future.
Sönke Schulz
For more up-to-date farming news click here and subscribe now to profi and save.