AGCO, CNH and Claas have all temporarily suspended their European manufacturing activities, but we are still not clear how the COVID-19 situation is affecting Deere & Co.
Company leadership is closely monitoring guidelines issued by country and state level authorities and acting accordingly, is the official message, which includes temporary and partial suspension of production due to those mandates and/or to resulting supply chain disruptions in Asia, Europe, and South America.
The company’s US attractions (John Deere pavilion, historic site, tractor and engine museum and world HQ display floor) and factory tours are closed until further notice, but the only manufacturing plant that we know of where Deere has suspended production is at the construction and forestry equipment factory in Dubuque, Iowa.
This closed on March 30 after management learned of a confirmed virus case with an employee there. The facility is currently undergoing a thorough disinfection and employees will return to work via staggered, scheduled start-ups.
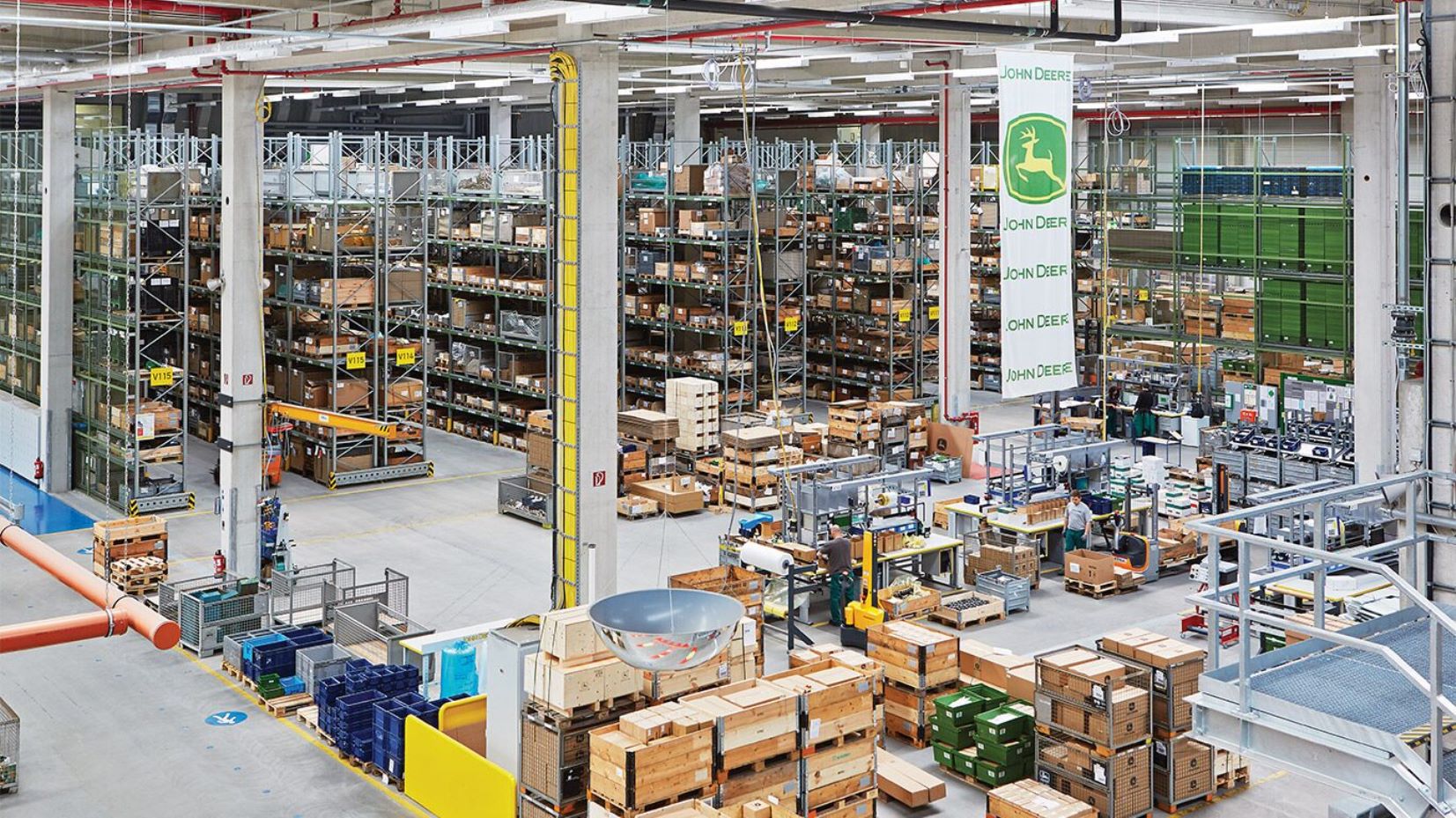
More than 300,000 different parts from knife bolt to a 10.7m combine auger are stocked at the European parts distribution centre in Germany.
What we can confirm is that John Deere’s parts business is currently not affected and European depots are continuing to deliver to order. All aspects of the UK & Ireland parts business are working normally including overnight delivery by air from the European parts distribution centre in Germany, with just the cut-off time for orders being brought forward a little due to Birmingham Airport closing earlier in the evening.
We are told that inventory levels are at the usual high level for this time of the year, just ahead of the season. In addition, John Deere Ltd’s parts inventory is higher at this time than in previous years due to a recent expansion of storage capacity, with nearly US$1m invested in new racking, order picking equipment, lighting and barcode scanning equipment at the Langar parts warehouse.
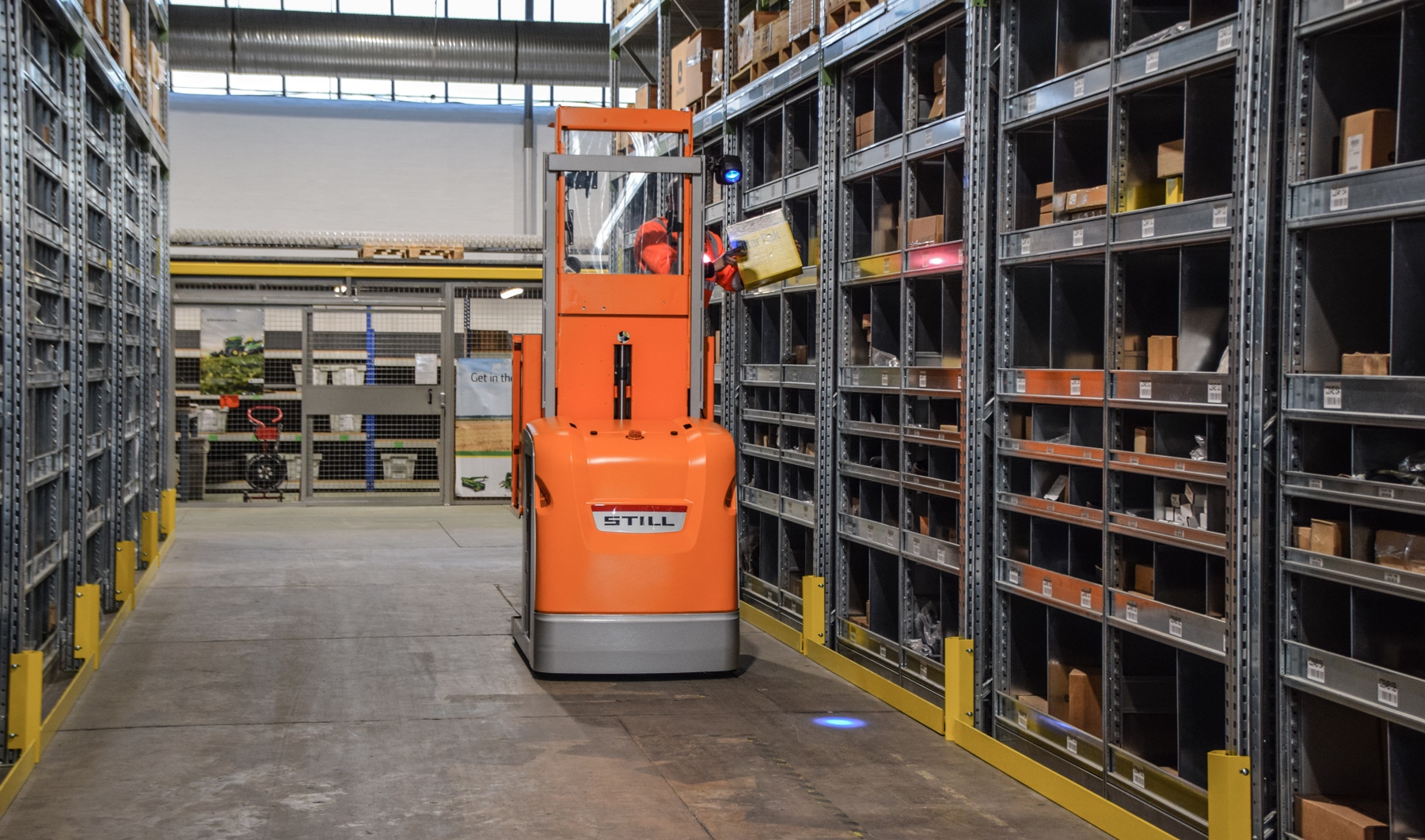
The parts inventory at Langar is higher at this time than in previous years due to a recent expansion of storage capacity.
Dealerships are still operating and maintaining their new machinery, parts and service delivery processes as far as it is possible, practicable and safe to do so within the current restrictions. Many have introduced contactless parts delivery and are keeping their customers up to date with regular bulletins by email and on social media.
The company is also able to provide connected support to farmers and contractors using the JDLink telematics system, including remote display access and service diagnostics without staff needing to visit farms and businesses unless absolutely necessary and in line with the latest official government advice.
Deere stresses that the priority continues to be the safety and well-being of its employees and the communities it serves. To that end, it has ‘put in place international and domestic travel restrictions, staggered shift schedules to enable social distancing, remote and flexible work arrangements for those employees not required in factory operations, and enhanced cleaning and sanitation regimens across its facilities.’