More than 250 entries were submitted to the innovation awards at this year’s Agritechnica. New Holland’s new flagship combine won the only gold, but there were 17 silver medals. All the winners are featured below.
ARABLE/ROOTS
GOLD FOR NEW HOLLAND
It was conceived and will be made at Zedelgem in Belgium, but otherwise New Holland is saying little this side of the show about its new flagship twin rotor combine. Described as a game-changer in terms of capacity and fuel efficiency over the current CR10.90 flagship, all the company is prepared to let slip is that it features a new driveline, wider chassis, threshing and cleaning systems and that the straw chopping and distribution system is equipped with camera-based control technology.
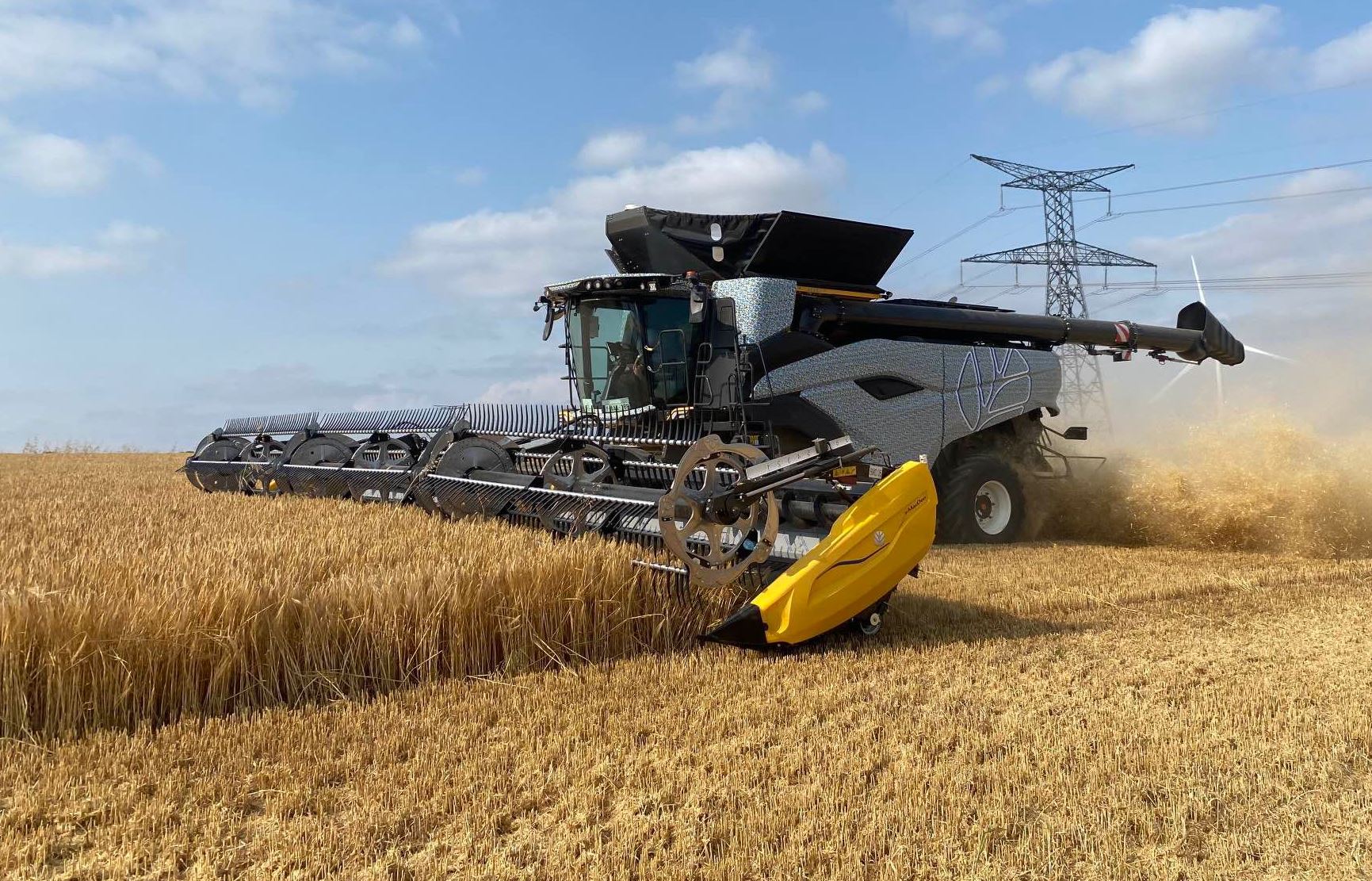
Believed to have been put through its paces throughout Europe, North America and Australia, maximum cutterbar width is reported to be 15m and the weight of the new machine is said to be on a par with the CR10.90. The longitudinal mounted engine will also have significantly more power too.
THE SILVER MEDAL WINERS ARE:
LEMKEN
The sensor system developed by Lemken and Dutch firm Track32 alerts the driver should a soil engaging part be missing and forecasts when wearing parts need replacing. Known as IQblue, and described as a useful aid on a standard tractor and essential for autonomous vehicles, tool analysis is carried out when the implement is lifted at the headland by analysing camera images using an AI algorithm.
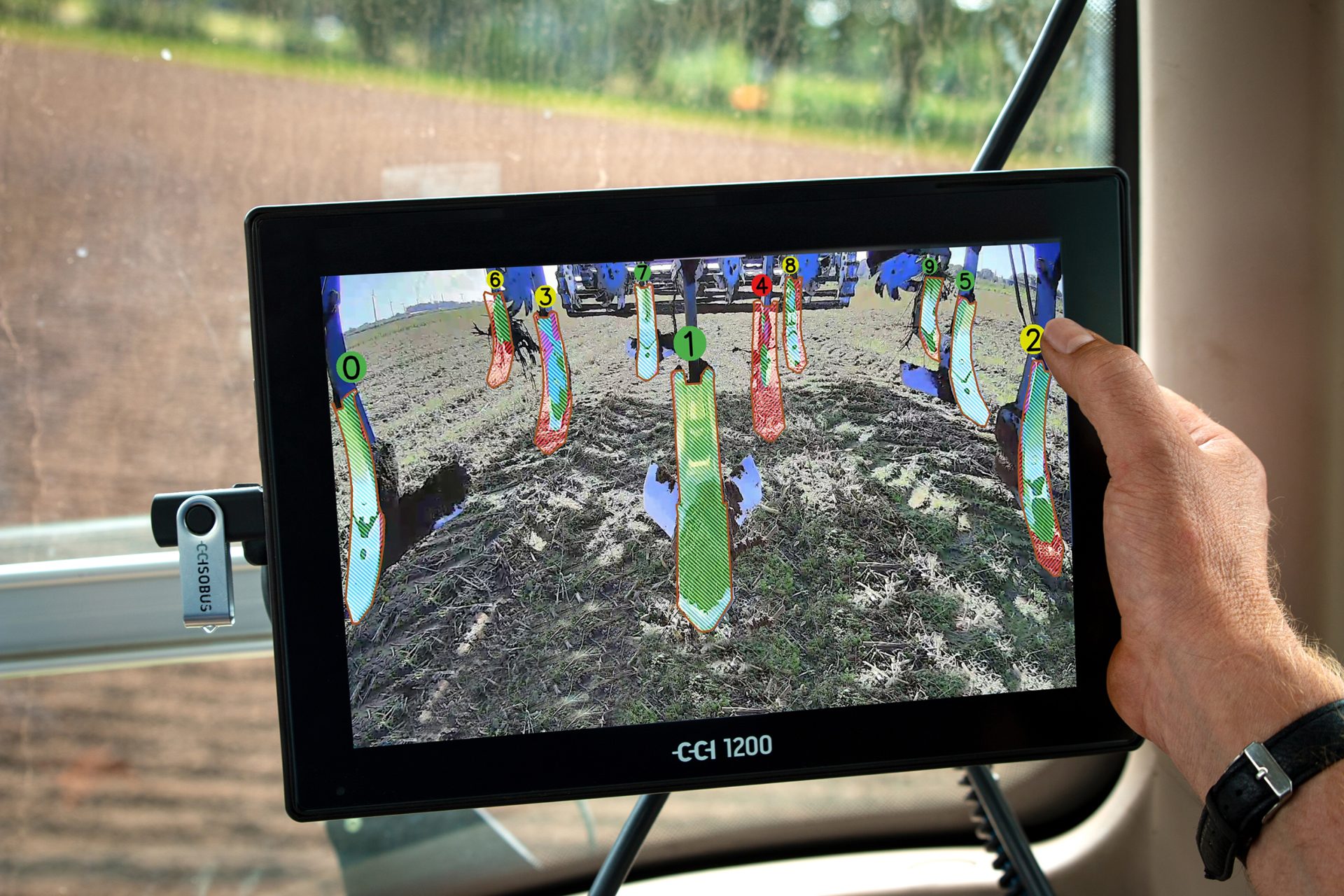
The system displays warnings in the form of a traffic light system. Coulter loss is displayed as red and damaged or worn wearing parts are highlighted in yellow. All is well when a green light is shown.
GRIMME
Grimme won a silver medal for a hydraulically interchangeable separator that allows a potato harvester to be converted to lift onions at the push of a button. Called ChangeSep, and combining two existing systems in a single machine, the changeover between ClodSep finger web and EasySep deflection rollers takes just two minutes and is done hydraulically from the tractor cab. Levelling adjustment of the first and second separator is still possible, and the speed of both can be adjusted individually and continuously, allowing the harvester to be adapted to different conditions and crops.
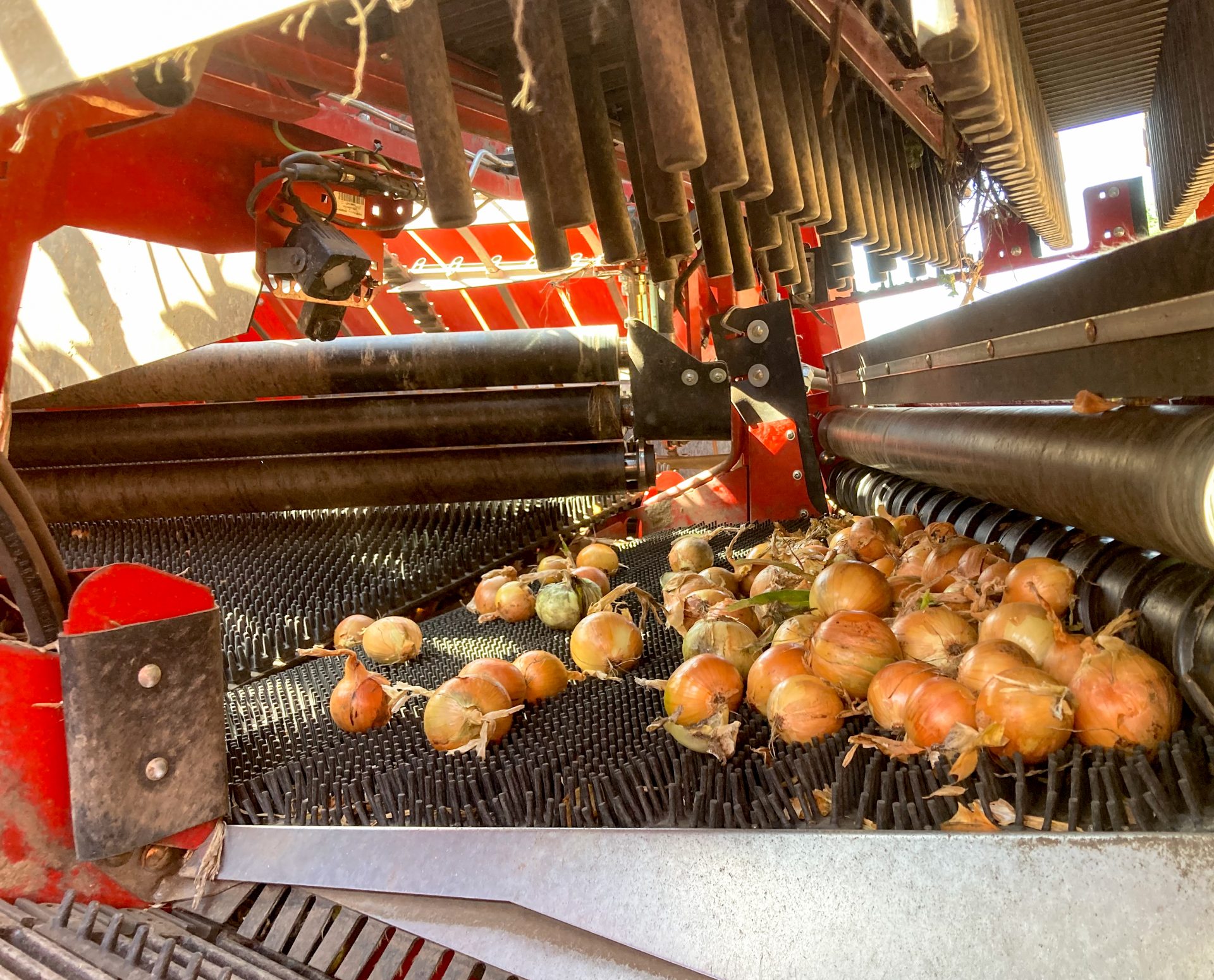
The TerraControl intake can be used to harvest potatoes and windrowed onions without modification. Already available on the Evo 290, ChangeSep will be offered on other machines next season. Grimme won a second silver medal for a potato windrower (jointly developed with Indian manufacturer Shaktiman) for small-scale growers in developing countries.
RADICLE AGRONOMICS
Claimed as a significant evolution of the soil sampling process for precision farming, Radicle Agronomics is a system that combines sampling, analysis, and the entire logistics of soil sampling. Developed by Precision Planting, and described as simple, fast, reliable, and precise, it eliminates the need to manually prepare and label bags of soil.
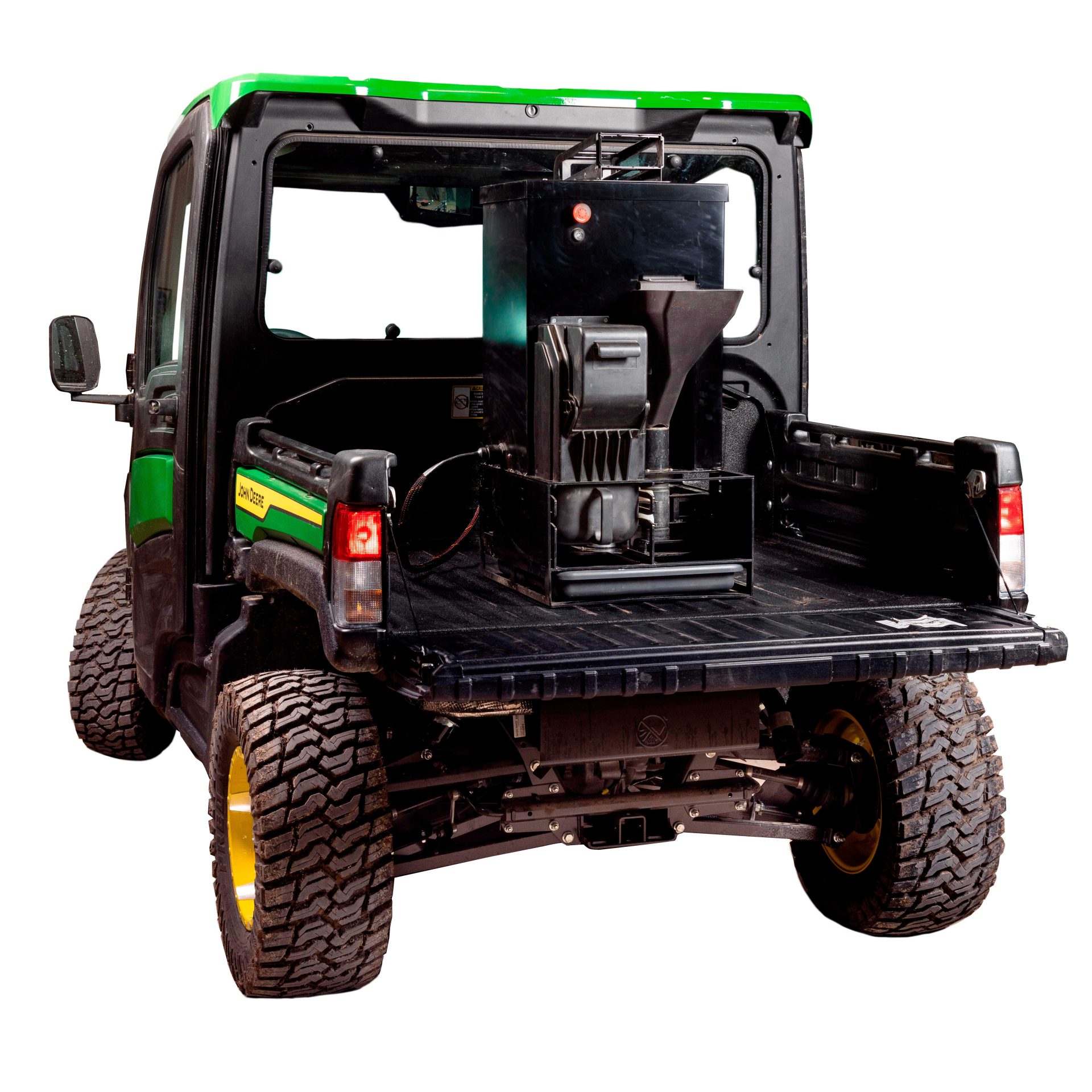
This is now done automatically in the field. RFID technology is used to provide each sample with the coordinates and the data necessary for further processing, and the soil laboratory is included in the system automatically completes all of the necessary work (calibration, preparation, analysis, and report preparation) within minutes.
AMAZONE
Developed as a software option for the ZA-TS mounted and ZG-TS trailed fertiliser spreaders, CurveControl adjusts the spread pattern to prevent under/over application while navigating a field corner. Curve compensation is already available on Amazone crop sprayers. However, the company says that this is easier because the application rate only has to be adjusted within the width of the boom.
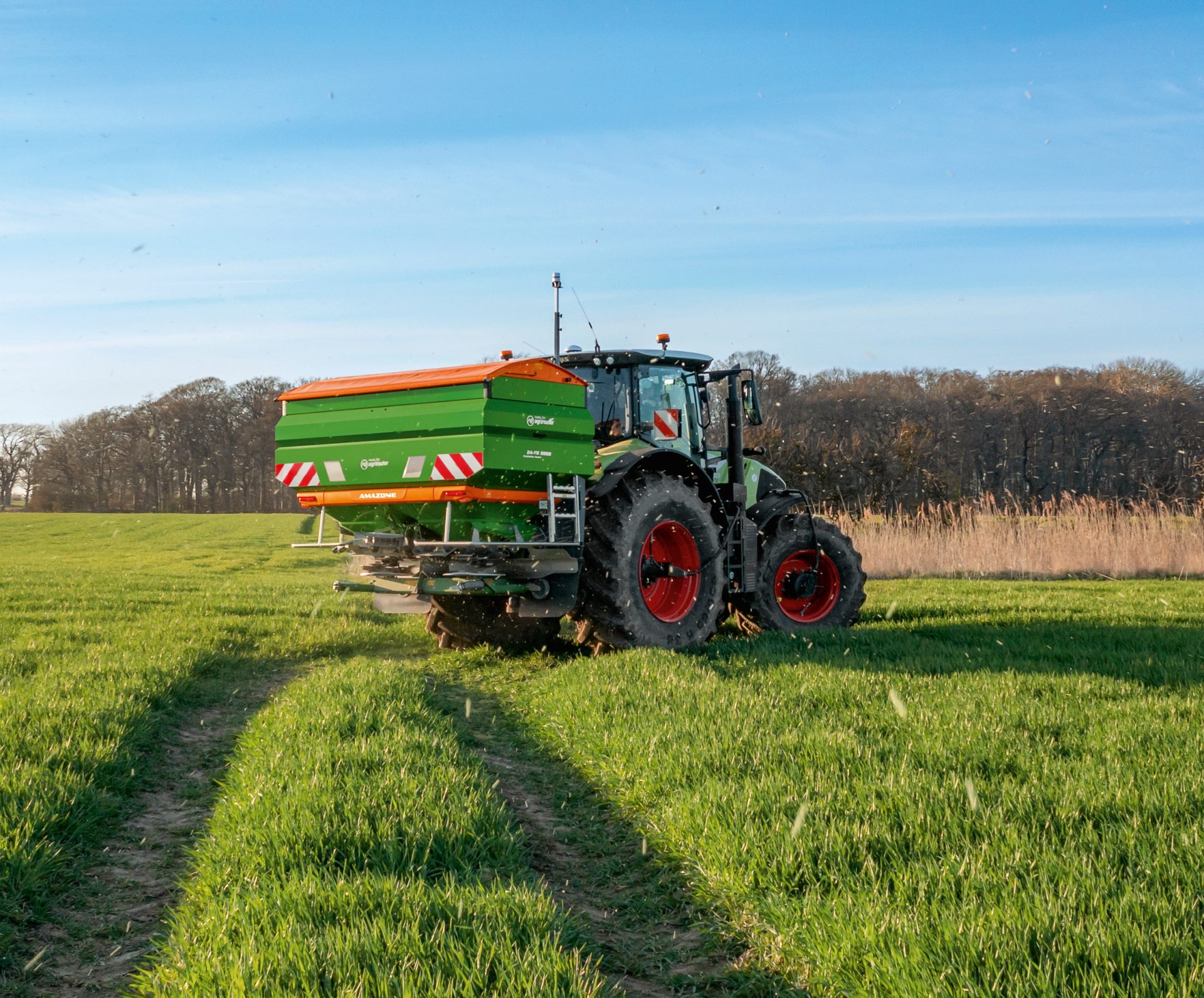
It is much harder with a fertiliser spreader, is the message, where the throwing distance can be up to twice the working width and, depending on the type of fertiliser, the application can be many metres behind the spreader. This requires precise knowledge of how the spreading discs work with different fertilisers and accordingly complex implementation in a control algorithm.
SAPHIR
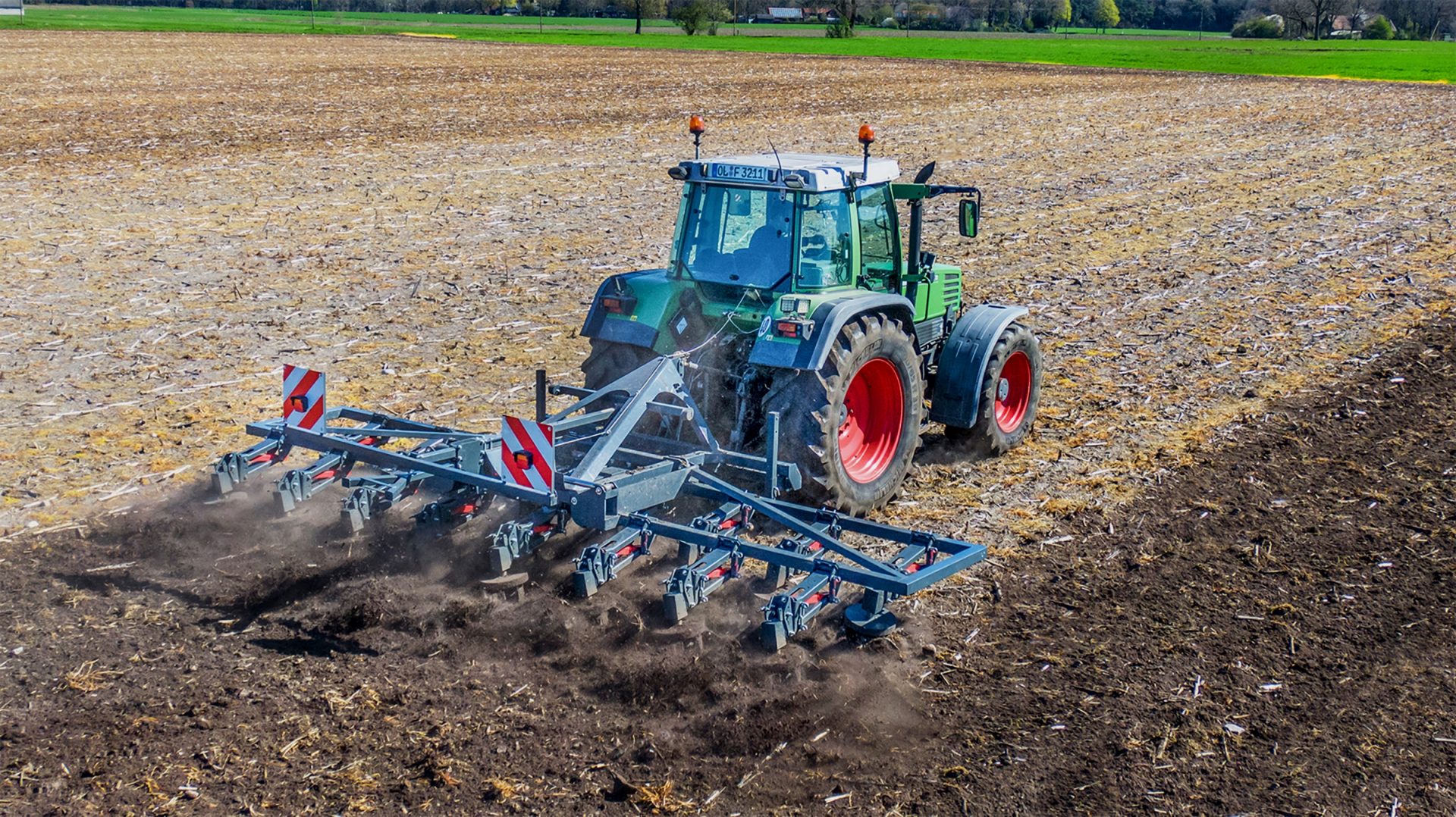
The GrindStar cultivator developed by German company Saphir Maschinenbau is designed to conserve soil moisture and provide the optimum conditions for volunteer cereals. Developed jointly with the University of Applied Sciences (Cologne) and fellow German company Seed2Soil, sharply angled 740mm-diameter ground-driven rotors work the soil to a depth of just 2.0cm. Each one is mounted on a parallelogram linkage so it can maintain its depth. Power requirement is around 26hp per meter.
ALL-IN-ONE
Integrated cutting blades on the outer edge of the four elements on the rotating ridge former made by German company All-in-One are designed to slice through surface trash from previous crops to prevent it from clogging. Said to require little tractive power, and helping to reduce the risk of damage when reversing, the ridging elements can work at speeds of up to 15km/hr.
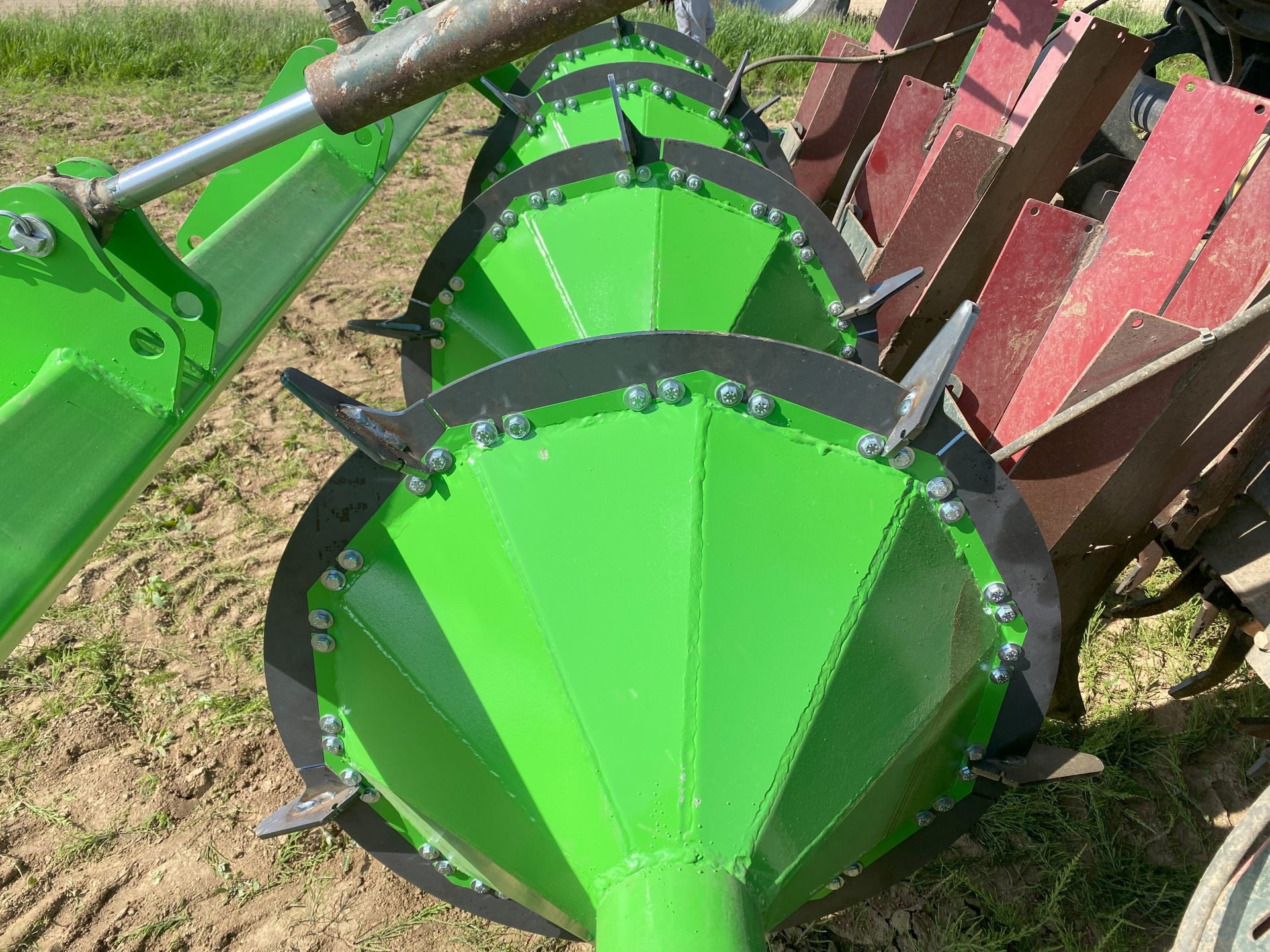
Developed to fit behind a four-row planter, the company has also thought of ways to reduce soil erosion. The five paddles attached to each disc leave a series of indentations in the bottom for water to settle in.
TRACTORS, LOADERS AND HANDLERS
STEYR
Steyr stunned visitors with its Konzept tractor at the last Agritechnica in 2019. Described as a development of this, the prototype tractor heading to this year’s show is based on the 180hp (rated) Steyr 6175 Impuls CVT. The combination of hydro mechanical CVT drive to the rear axle and the hybrid module on the front axle – both of which can be combined with an intelligent 4wd clutch – allows the hybrid tractor can transmit up to 260hp.
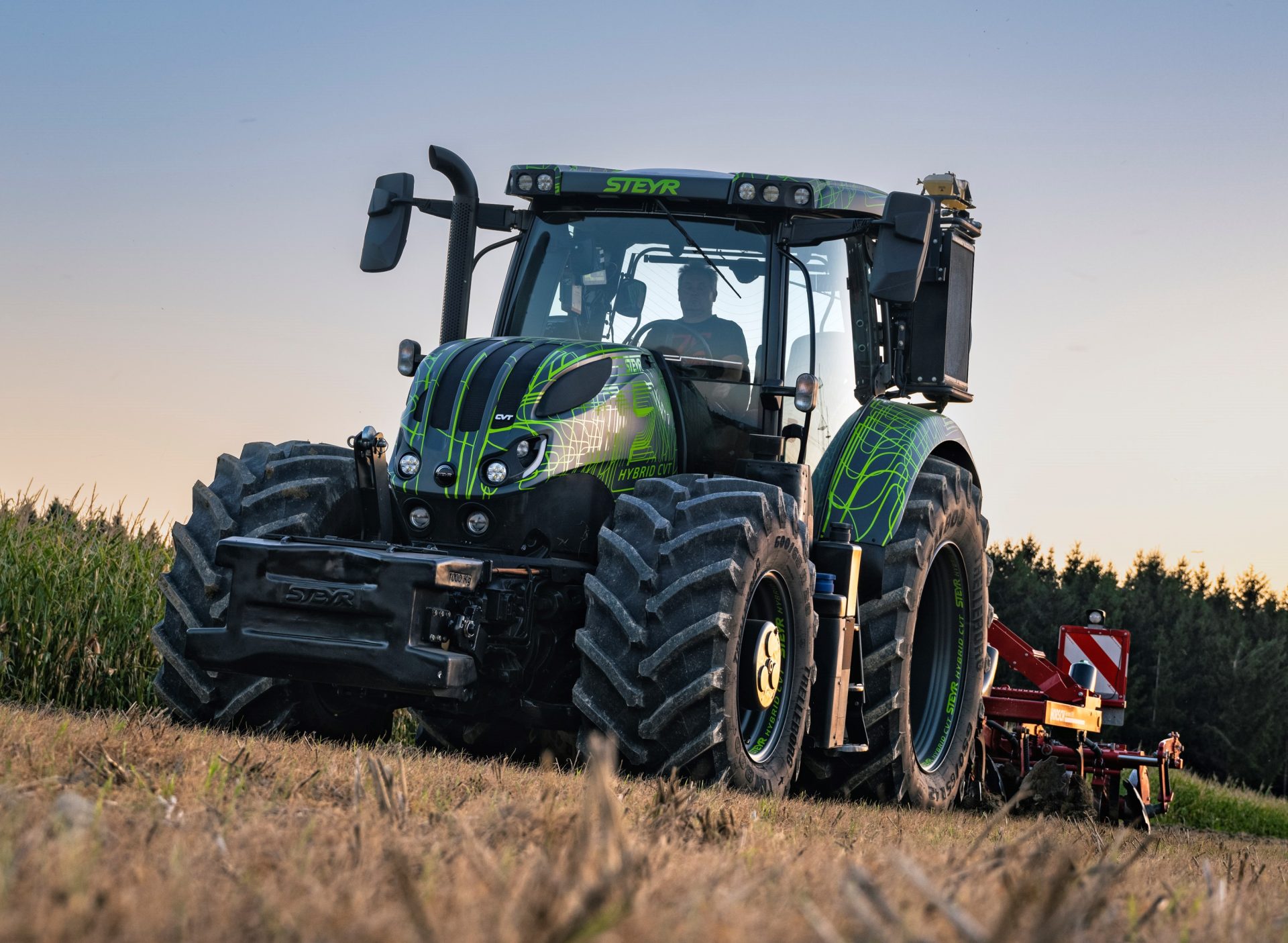
The technology provides numerous possibilities including the E-CVT mode, where the tractor is powered electrically up to 75kW and 1,100rpm. E-Steering accelerates the front axle during headland turns to reduce the turning radius and E-Boost provides additional electric power when needed. E-Braking keeps the tractor’s speed constant when travelling downhill, using the electric driveline like a retarder, and the E-Eco mode has the potential to reduce fuel consumption by as much as 10%. The hybrid tractor can also power electric implements.
STOLL
A telescopic loader boom that can extend the lift height by 1.45m has been developed by Stoll and with good reason too. Tractors in the 120-150hp bracket are the most popular for adding a loader and this generally coincides with a maximum lift height of 4.0m, however, if you want to load an HGV trailer which can be up to 4.0m high, it doesn’t take much of an upset in ground conditions to stop the loader being able to do its job.
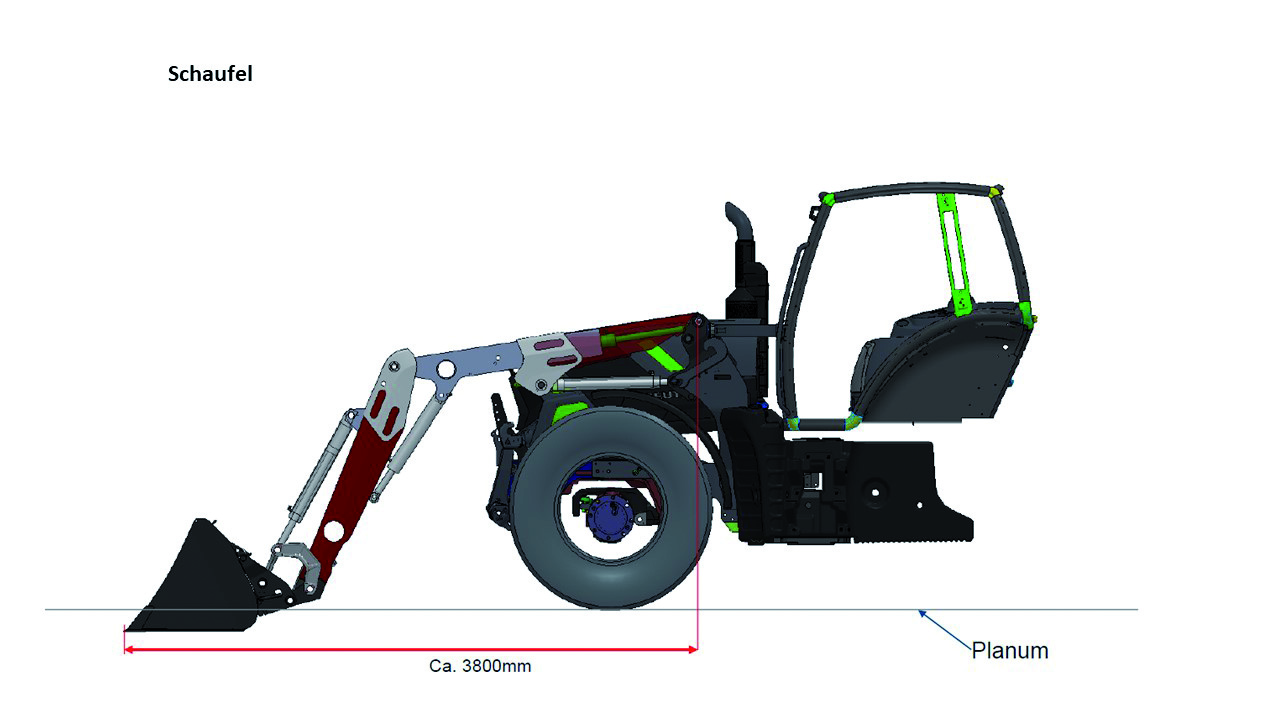
The extra reach boom will be available on all Profi Line models and is a two stage approach. The first part of the boom telescopes out 0.5m, as a secondary movement, the forward section of the boom can be straightened out for extra lift height. When fully stretched this can extend the reach to 5.45m.
NEW HOLLAND
New Holland won a silver medal for the T7 (up to 270hp) Methane Power LNG prototype already shown earlier this year. The New Holland and Bennamann solution can be provided by liquefied biomethane sourced from livestock muck and slurry. The patented active temperature-controlled fuel system incorporates a stainless-steel tank shaped to match its diesel counterpart. It has a self-supporting vacuum space that insulates the fuel within, enabling a reduced tank thickness.
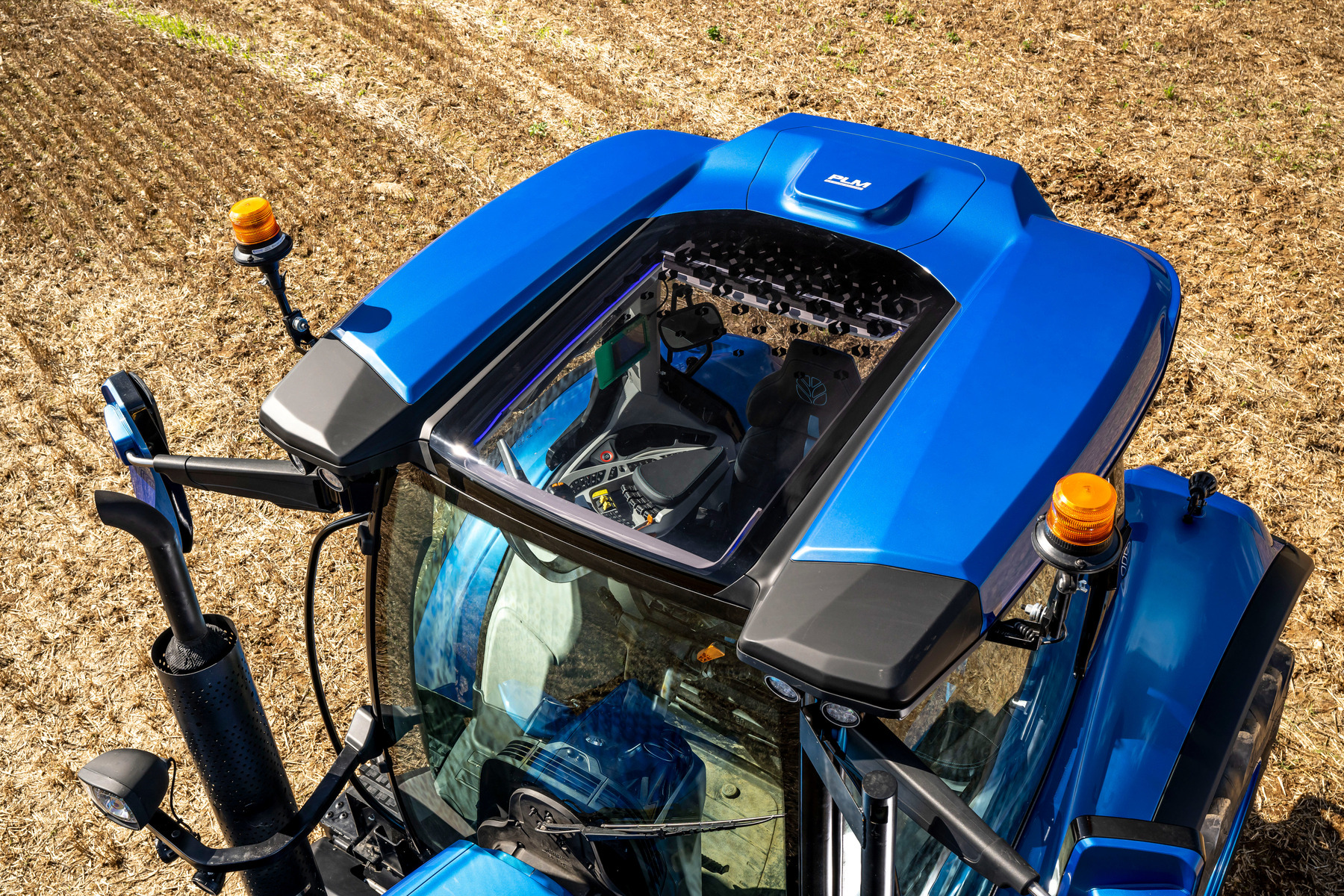
The tractor comes with PLM Intelligence and PLM Connect uptime support, and has the same SideWinder Ultra armrest, new IntelliView 12-inch touchscreen and CentreView fixed hub steering wheel mounted display as the higher HP tractors. The new design and styling (includes the full length sky dome roof) for the methane powered T7 will be adopted on future New Holland tractor ranges.
CLAAS
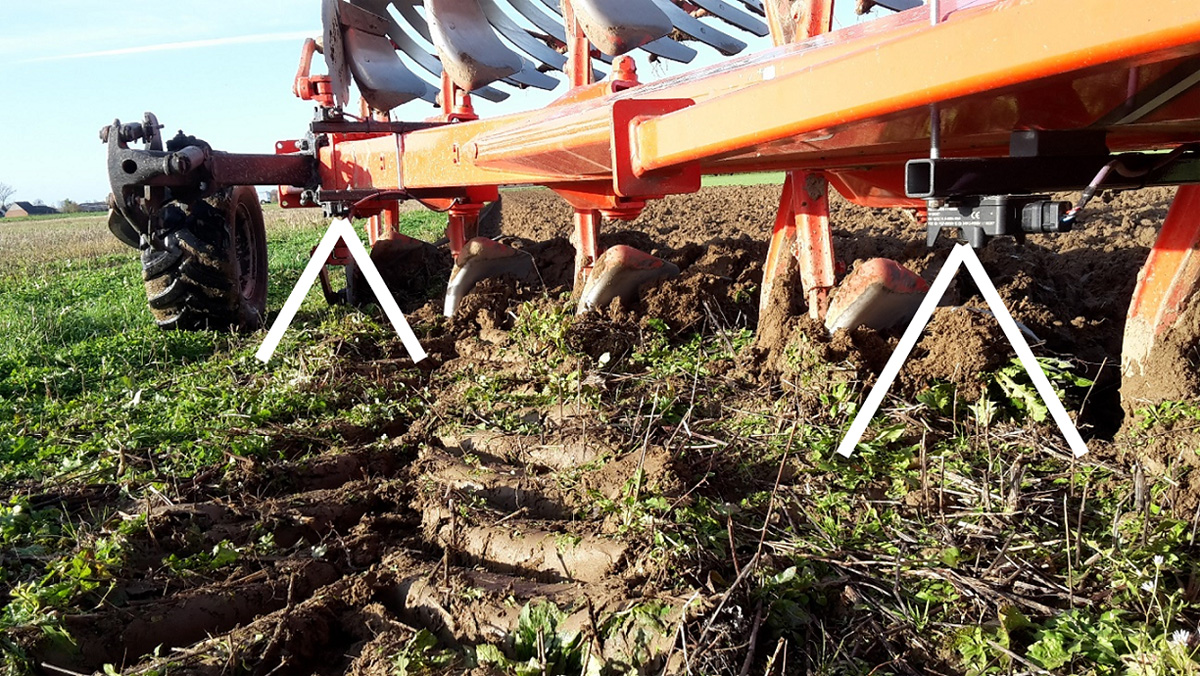
Tractive power is usually regulated by the lower link arms, but raising or lowering them can result in different working depths at the front and rear of a cultivator. Claas is looking to optimise this by integrating the hydraulic top link into its multi-dimensional three-point linkage control system. Height measurement sensors mounted at the front and rear of the implement transfer position signals to the tractor’s control electronics.The length of the top link is automatically adjustment via an additional hydraulic controller. This ensures that the implement is aligned parallel to the ground.
CASE IH
Case IH Axial-Flow combines are now available with a system that assesses crop density and regulates forward speed and material intake before it enters the machine. Allowing operators to exploit the full potential of a combine without fear of blockage, the ‘Advanced Feedrate Control’ system relies on four forward-looking radars units positioned across the header.
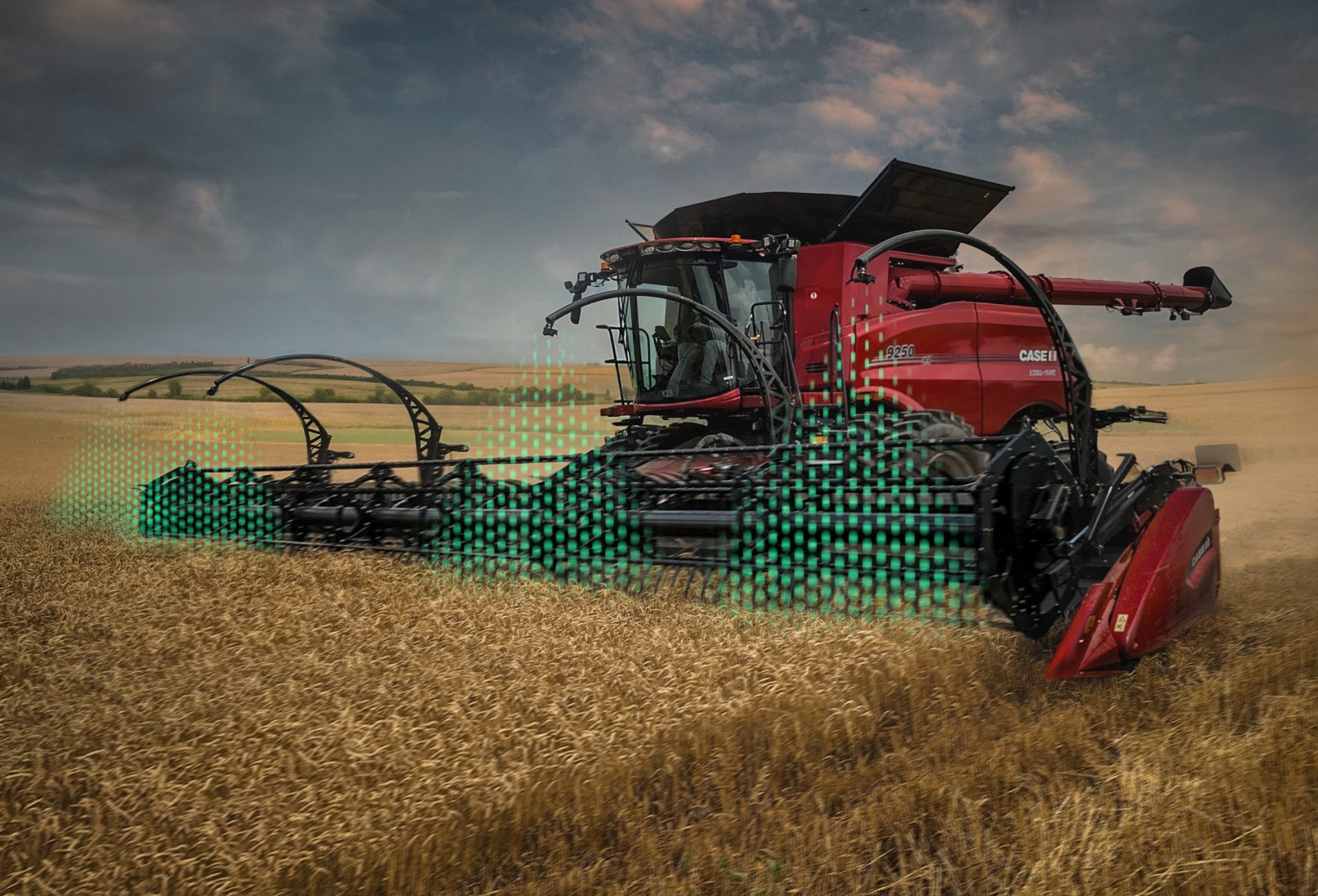
Measuring the plant mass from the ground up, the information generated is used to automatically adjust key settings such as forward speed for the crop volume the machine is about to ingest. As a result, forward speed and engine load are maintained as closely as possible to the desired level, maximising output without the risk of blockage.
Experienced operators can get the maximum from their machine, is the message, while less experienced ones can be more confident they can push the combine without fear of it blocking. The system offers the potential to boost workrates by up to 20% when compared with a combine fitted with the established reactive automated feedrate intake. At Agritechnica, the system, for which a number of patents have been sought, will be fitted the VariCut header paired with the Axial-Flow 7160.
AGXEED, CLAAS AND AMAZONE
The use of an autonomous field robot with a cultivator is only effective if it is able to detect a blockage or wearing part loss. With this in mind, joint work between AgXeed, Claas and Amazone, has led to the development of 3A (Advanced Automation and Autonomy) planning and implementation software where sensors register issues, such as a blockage or lost coulter, and can also monitor a packer roller to ensure it is operating at the right speed.
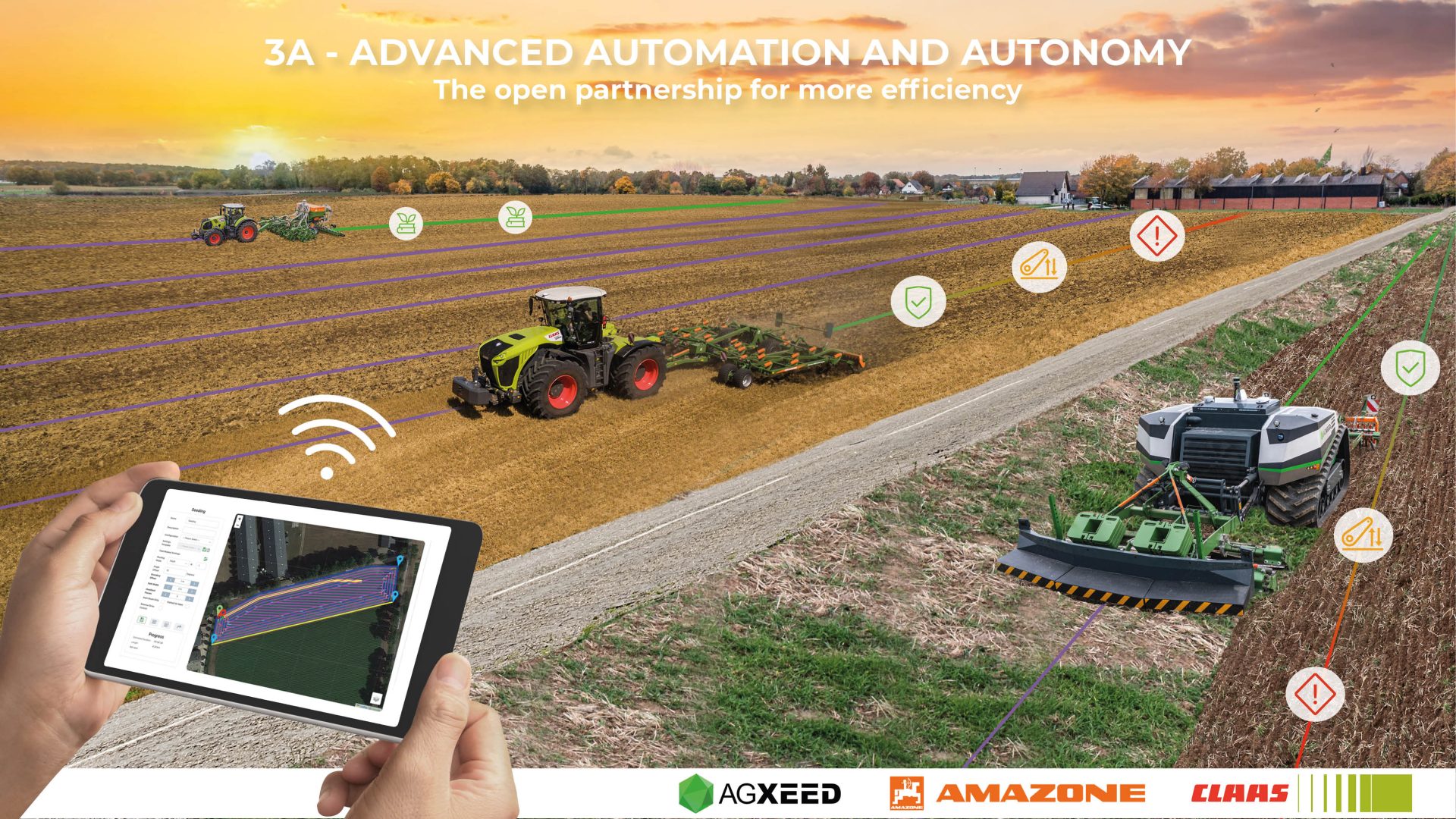
The AgXeed Box from the 3A system enables standard tractors and implements to be integrated into the planning and autonomous implementation process for the first time by means of the ISObus interface. Implements can also interact with robots and tractors via this interface in order to optimise field processes.
NEW HOLLAND
Developed by engineering teams in the US and Italy, aided by partnership with Californian based Monarch Tractor, the T4 Electric Power has a peak power of 120hp, maximum torque of 440Nm and maximum speed of 40km/hr. Said to be well suited to mixed and livestock farms, orchards and specialty applications, it depends on the workload, but the battery is said to provide a full day of use, and recharge time with a fast charging system of just one hour.
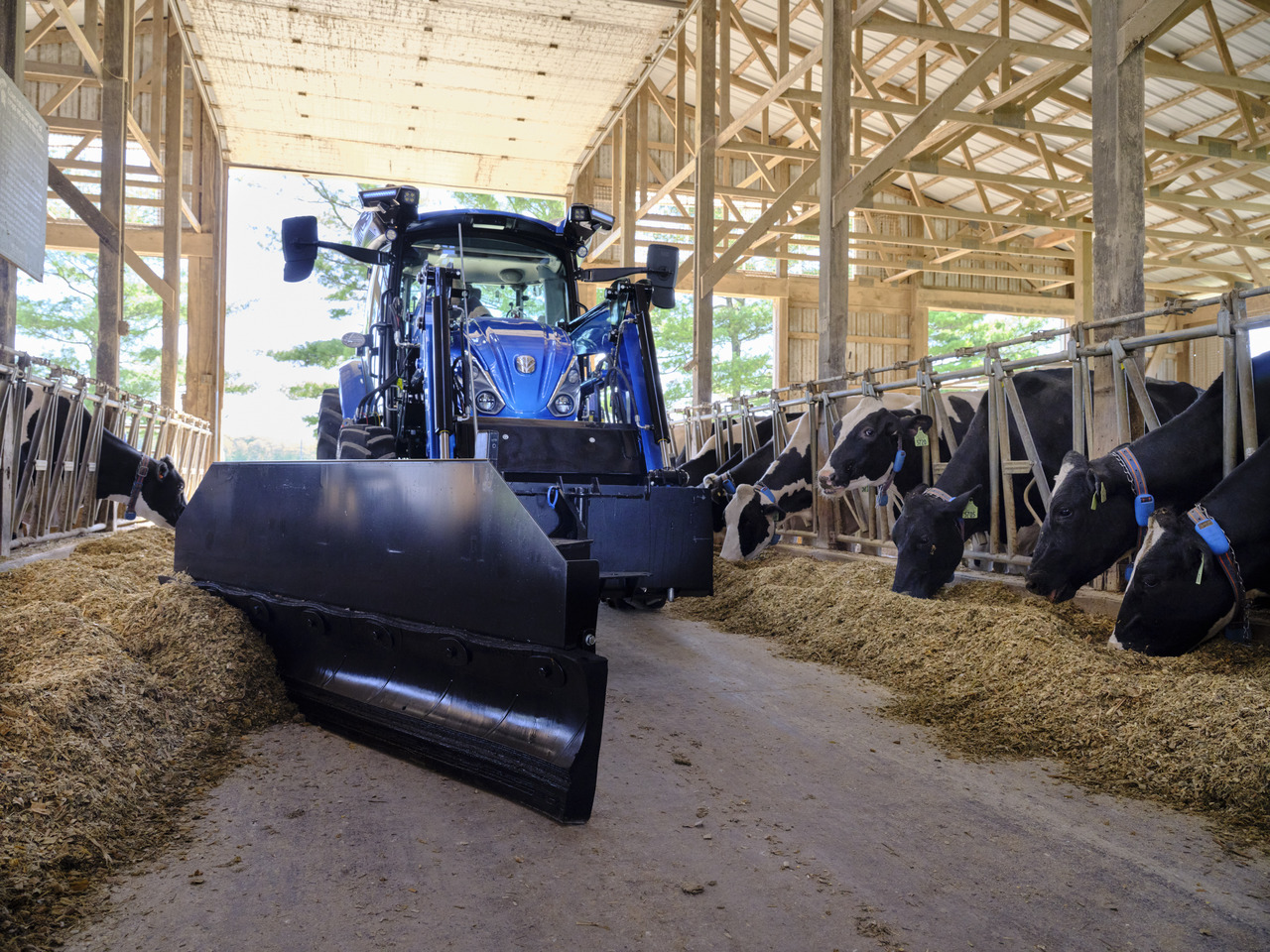
The tractor can also be used as a backup power source for other devices and machines and can power electric implements. Stand out features include Smart Roof, a 360° system which integrates sensors, cameras, and control units to detect and avoid obstacles, and the Follow Me Mode allows the tractor to follow the operator when outside the cab. New Holland says this is useful when passing through gates or feeding cattle. Commercial production is due to start before the end of this year.
LIVESTOCK
ZUNHAMMER
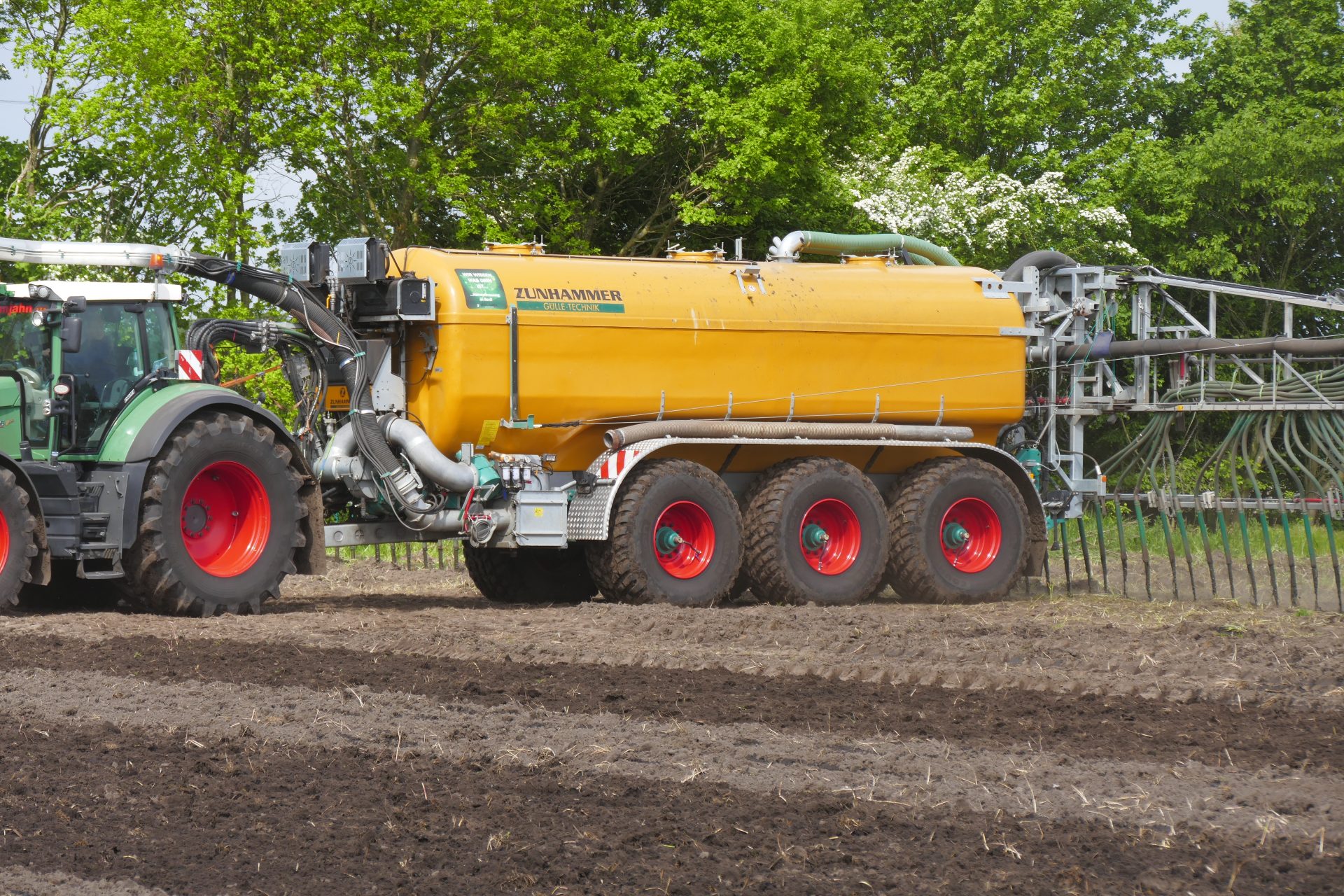
Zunhammer has developed a solution to ensure application accuracy when using wide working slurry injectors and trailing shoes. Called Eco-Duo Vario, it comprises two positive displacement pumps. Individually controlled by ISObus, pump rotational speed is automatically adjusted to maintain the required application rate. The frame comprises separate feed hoses for both the left and right this allows slurry volumes to be regulated independently on each side (for example, working width of 30m corresponds to two sections of 15m), without altering the application rate on the rest of the machine.
FENDT
Automatic adjustment of the conditioner intensity helped the Fendt Slicer win a silver medal. Developed jointly with ConGra Victor Klüber and Fritzmeier, the concept is said to result in more even drying of the material for a constant dry matter content across a field for improved feed quality. Available on all models in the Pro series, crop volume is determined by creating an application map using satellite data or by having a sensor record the yield data directly in the field.
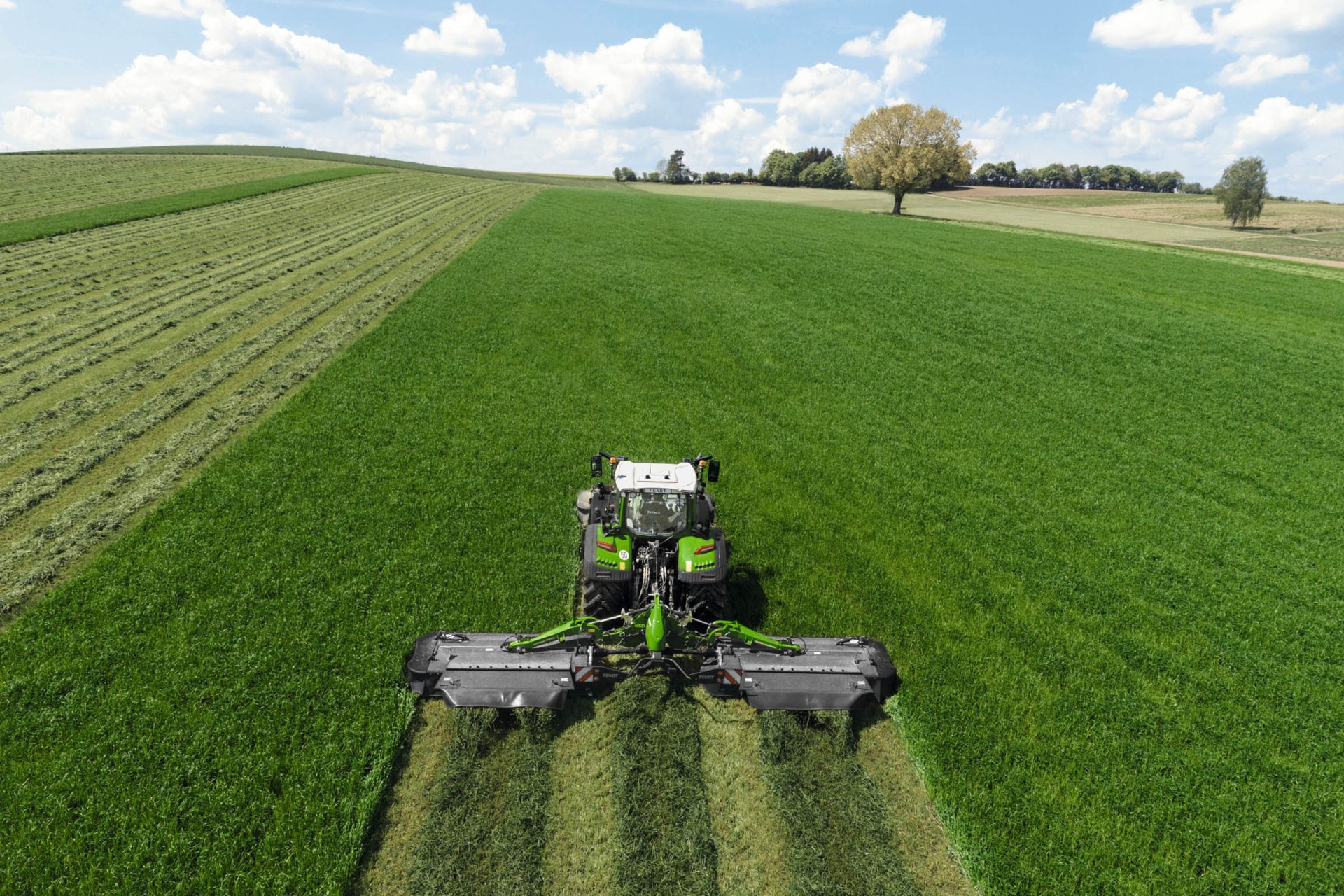
Data is sent via ISObus to the mower’s job computer, which calculates the appropriate settings and forwards them directly to the electric motor on the conditioner. Helping to reduce the driver’s workload, other claimed benefits of the system include lower fuel consumption and reduced set-up times.
KRONE
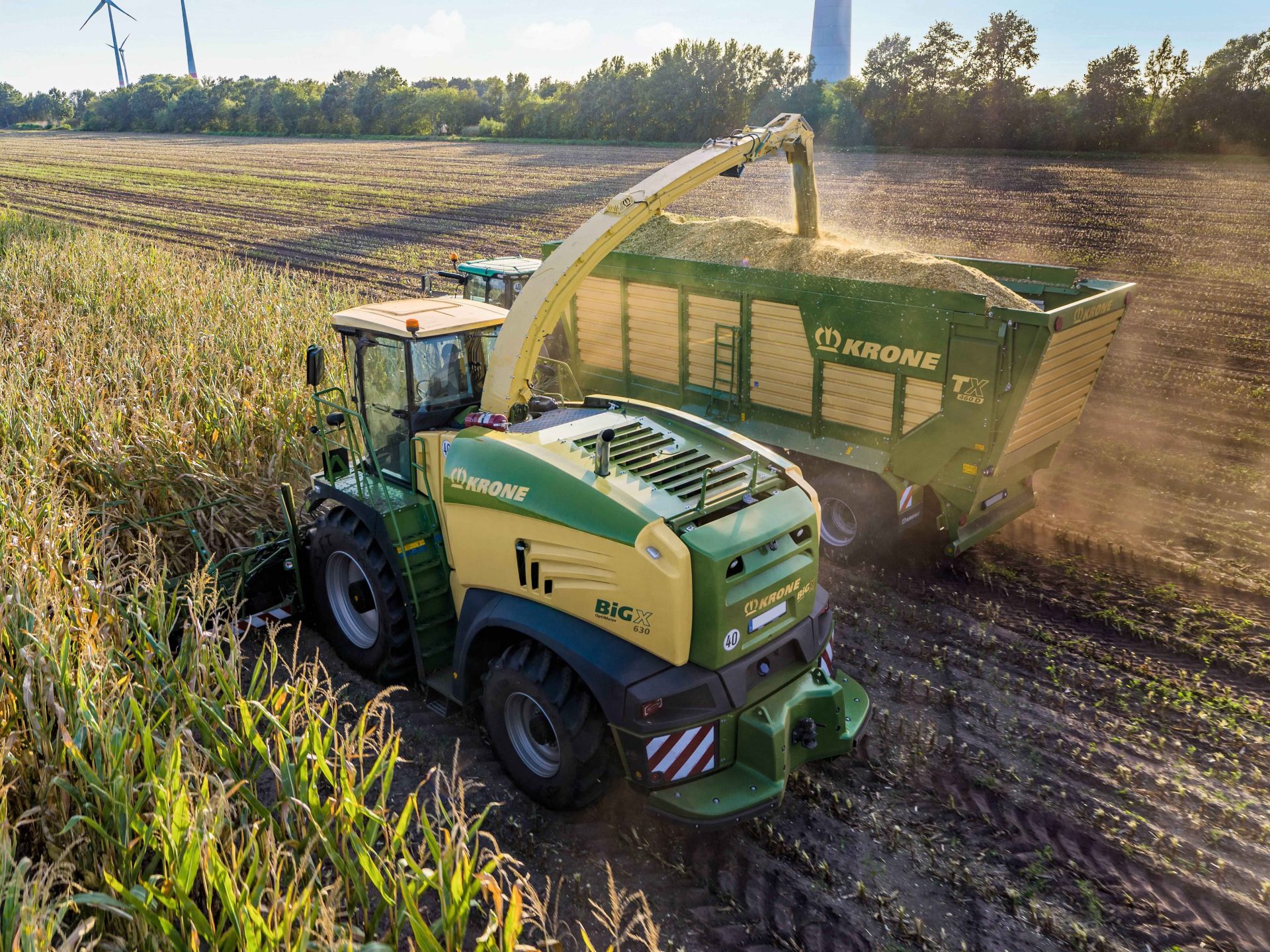
Krone has done away with the need to manually reset the sharpening stone used on Big X harvesters due to a new mounting system. Previously the stone would need to be manually adjusted after 400-450 sharpening cycles and could only be reset around four times despite a reasonable amount of stone material still present. The new stone is encased in a plastic holder, as the knives are sharpened the plastic is burned away and the firm’s research suggests this does not create micro-plastic filings in the forage. As well as a time saving, the stone can now be used up to 2,200 cycles.
For more up-to-date farming news click here and subscribe now to profi and save 47%.