To coincide with the UK Dairy Day on September 11th we are making a number of previously published articles available. Here’s some of the latest ideas we reported on back in June 2018. You can find more articles like this in our test centre.
With the desire to put into practise what he has learned, farm consultant Mike Hobbis set about creating a highly automated dairy unit. Not only are milking robots employed but there is also a fully automatic feeding system
Four years ago dairy consultant Mike Hobbis started out on a journey to achieve his career-long ambition to build the UK’s most modern milking set-up. Housing just 50 cows, it might be small but Wapley Hill dairy certainly ticks all the boxes to give it state-of-the-art status with an automated feeding system as well as a milking robot.
Having been advising farmers across the country on nutrition, housing and robotics for the last 40 years, Mr Hobbis had the benefit of a wealth of experience to put into practice but until a few years ago didn’t have the opportunity to do it on his own terms.
“I’m passionate about the whole dairy industry and have been lucky enough to see it evolve over the last four decades,” he explains. “But with no home farm to come back to I’d never been able to fulfil that passion in putting theory into practice. Then six years ago a parcel of 30 acres (12.1ha) came up for sale close to home and I decided to take the plunge and take the first steps down the road of becoming a farmer in my own right.”
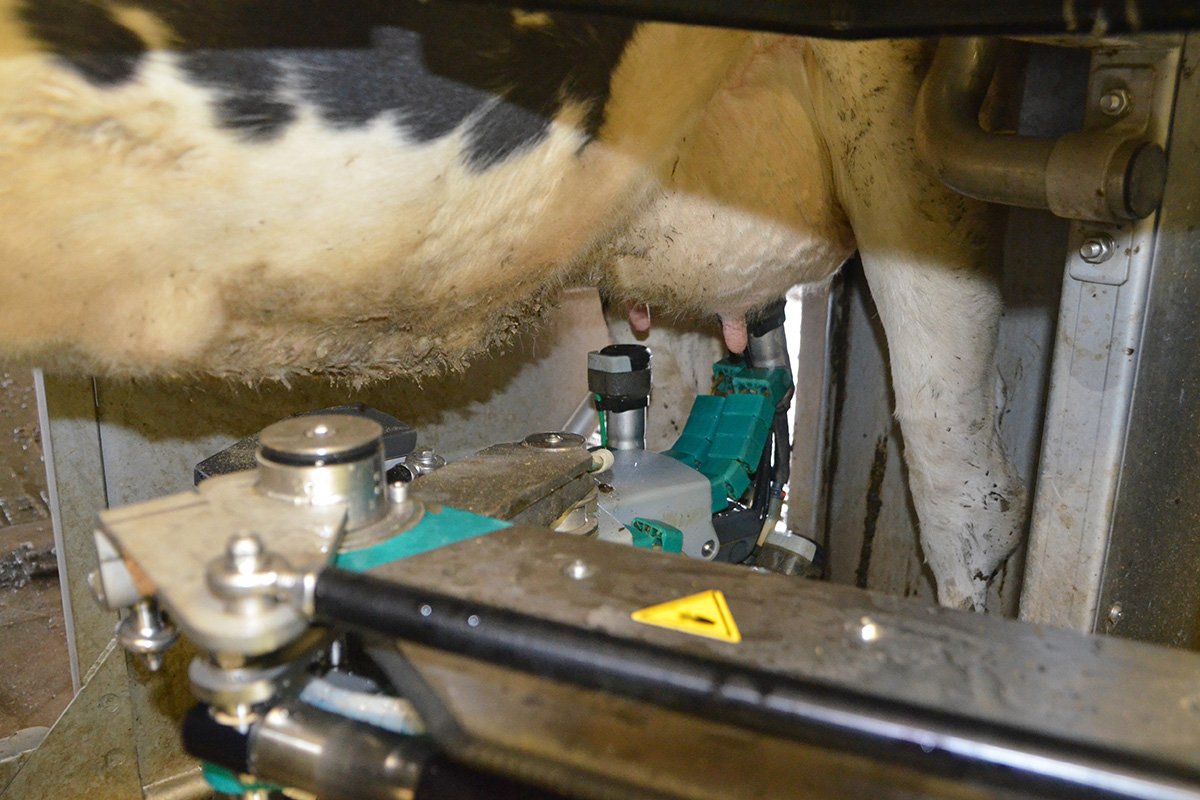
The robotic milking arm uses camera guidance to attach the cups to the teats.
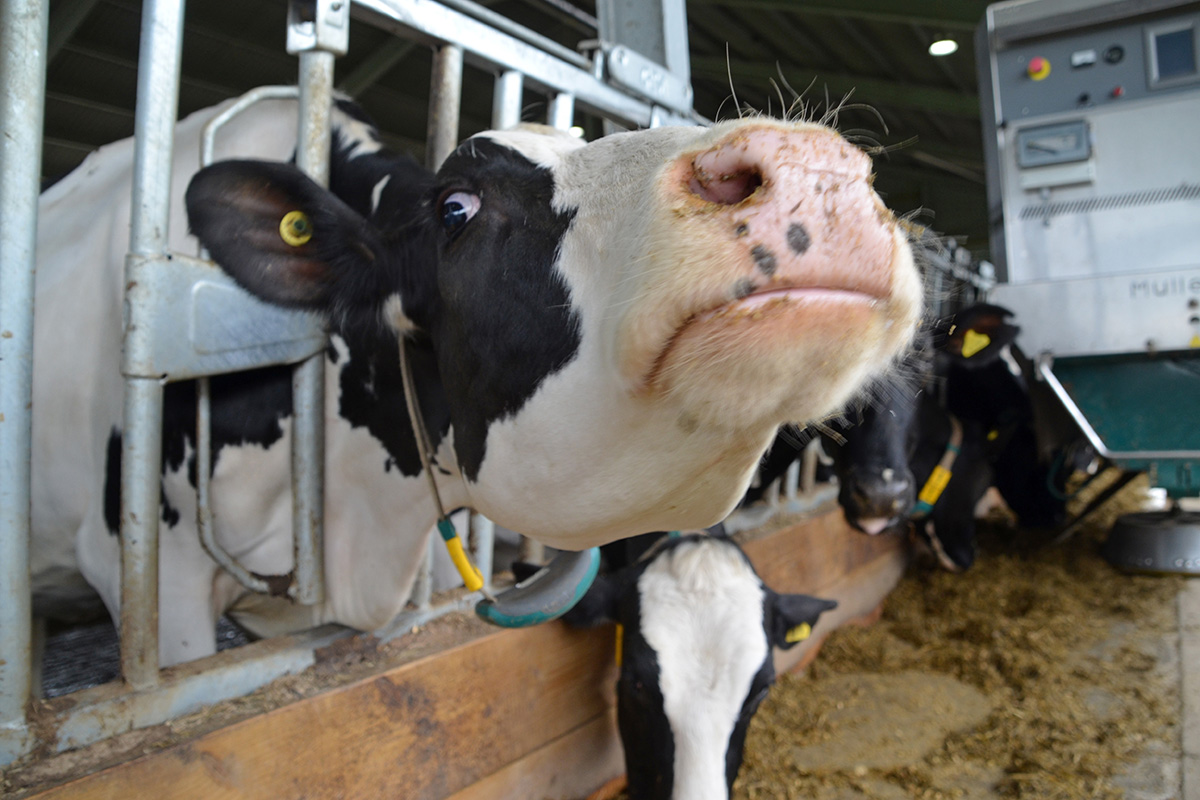
Collar activity monitors record the amount of time the cows spend with their heads down at the feed barrier as well as aiding in heat detection.
Rather than jumping straight in and immediately putting plans in place for a dairy, Mr Hobbis decided the sensible option was to look at ways of generating long-term revenue from the land that would help to finance the whole business proposition.
“My vision for the dairy was always that it should be carbon neutral so as soon as the deal was done on the land I started looking at my options for renewable energy,” says Mr Hobbis. “Solar seemed the most popular at the time but to me it seemed counter-intuitive to cover over productive farmland when any livestock enterprise on this small patch would be dependent on it for fodder production. So instead we went down the wind energy route.”
Not one to do things by halves, Mr Hobbis submitted plans for a 100kW turbine, having a decent three-phase connection to the grid to make exports of electricity possible. Initially planning was turned down but eventually it went through on appeal and in 2014 Northern Power erected a 37m high tower at the site. With it generating around £60,000 of revenue each year and providing an untapped source of power, Mr Hobbis was then able to start to get the wheels turning to establish his vision of the most modern dairy unit in the country.
“Nothing I would do was ever going to be large scale but I wanted to make sure we were making the most of what we had, he explains. “I wanted to set up an installation that would be ultra-efficient and would require the minimum labour input. That was critical because I still need to be free enough to do my consultancy work which takes me off all over the place. On top of that I wanted to build a dairy that could be used as a demonstration unit to showcase the latest technology not only to other farmers but also to the wider public.”
With his extensive knowledge of modern dairy technology he then set about nailing down exactly what was going to be required for a small-scale set-up to accommodate 50 cows. With experience of different robotic milking systems on clients’ farms he had confidence in this approach.
“The whole idea hinged around robotics and automated systems because without that I couldn’t do it and continue with my consultancy work,” points out Mr Hobbis. “But milking was only one part of the story – what about feeding and the things that are often picked up sub- consciously during milking like spotting bulling cows and any that are off colour? At the time, the only manufacturer offering the complete package that could deal with all this was Gea. I wanted to try and have an integrated system and so that’s the route I went down.”
Taking the plunge, he ordered a MI One single box milker to work alongside a Gea Mullerup MixFeeder and the German company’s CowScout activity monitoring system.
Much like other manufacturers’ machines, the MI One uses a robotic arm to attach clusters to the cow’s udder. Where it differs from the competition is that that single arm can be used to serve up to five different boxes, much like a small-scale conventional parlour with the human element replaced by automaton. The key thing here is that it is therefore a modular system, allowing further expansion of the set- up should that be required in the future.
“It wasn’t so much that I had an eye on expanding down the line, more that the MI One had been on the market for a number of years and had been proven whereas Gea’s Monobox was new at that time and I didn’t fancy being a guinea pig,” says Mr Hobbis. “The arms on earlier MI Ones had been of a different design but by the time I ordered mine they had been superceded by a newer, more reliable version.” Immediately as the cow enters the box, the cups are attached to the teats and a wash/rinse cycle begins. High rate pulsation is then used to stimulate let-down and help to avoid over- milking before a pre-milk flush. With that out of the way, the job in hands starts and the robot monitors milk flow from each quarter, waiting until each one is fully milked out before removing the cups individually. At the same time the electrical conductivity of the milk is analysed for early detection of any signs of mastitis.
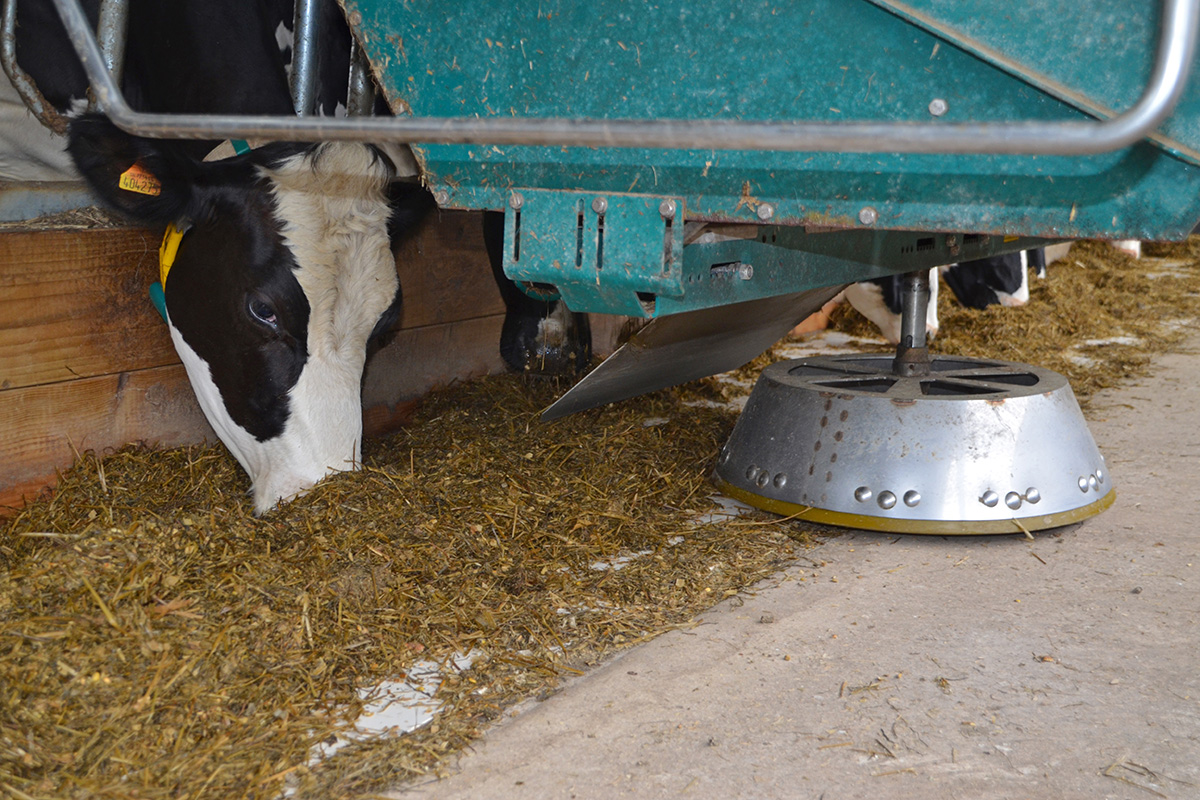
As the Mullerup automated monorail feeder runs up and down the barrier, a rotating wheel pushes up the remnants from the previous run to ensure every last mouthful gets cleared up.
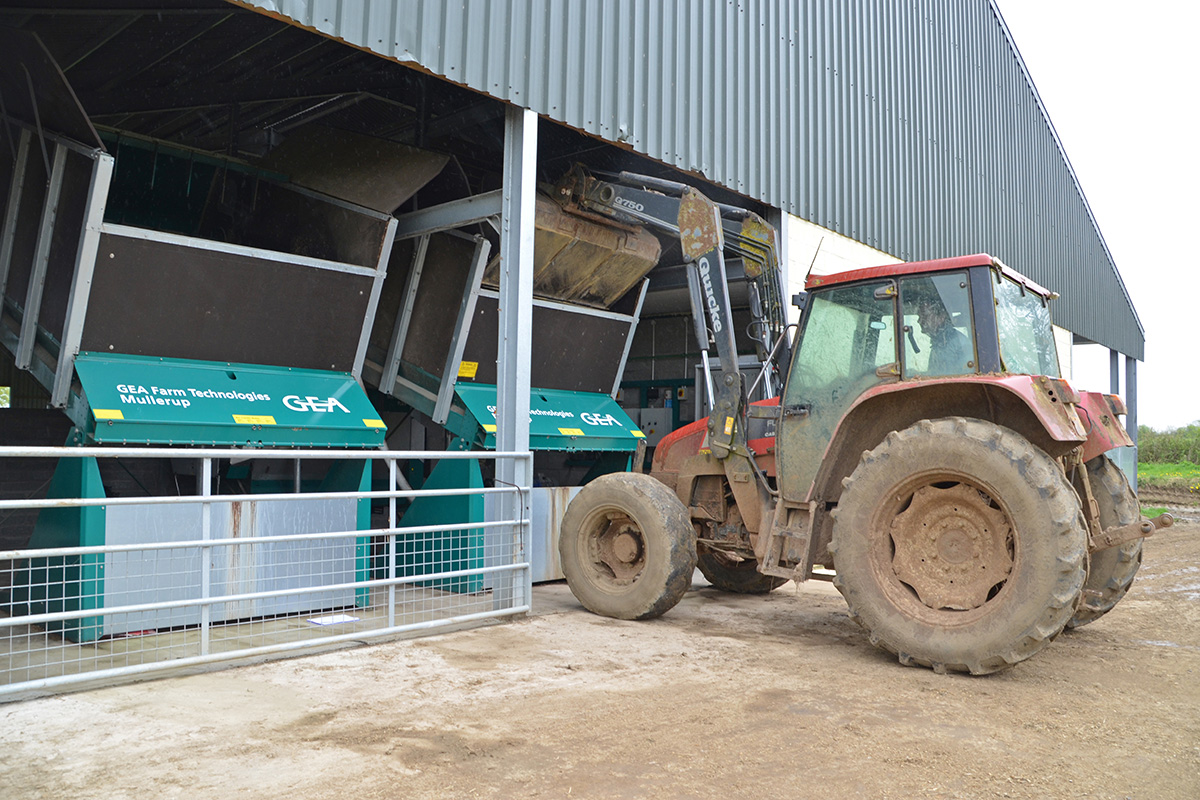
Twin bunkers are loaded with silage of different types to be dispensed as part of a TMR throughout the day.
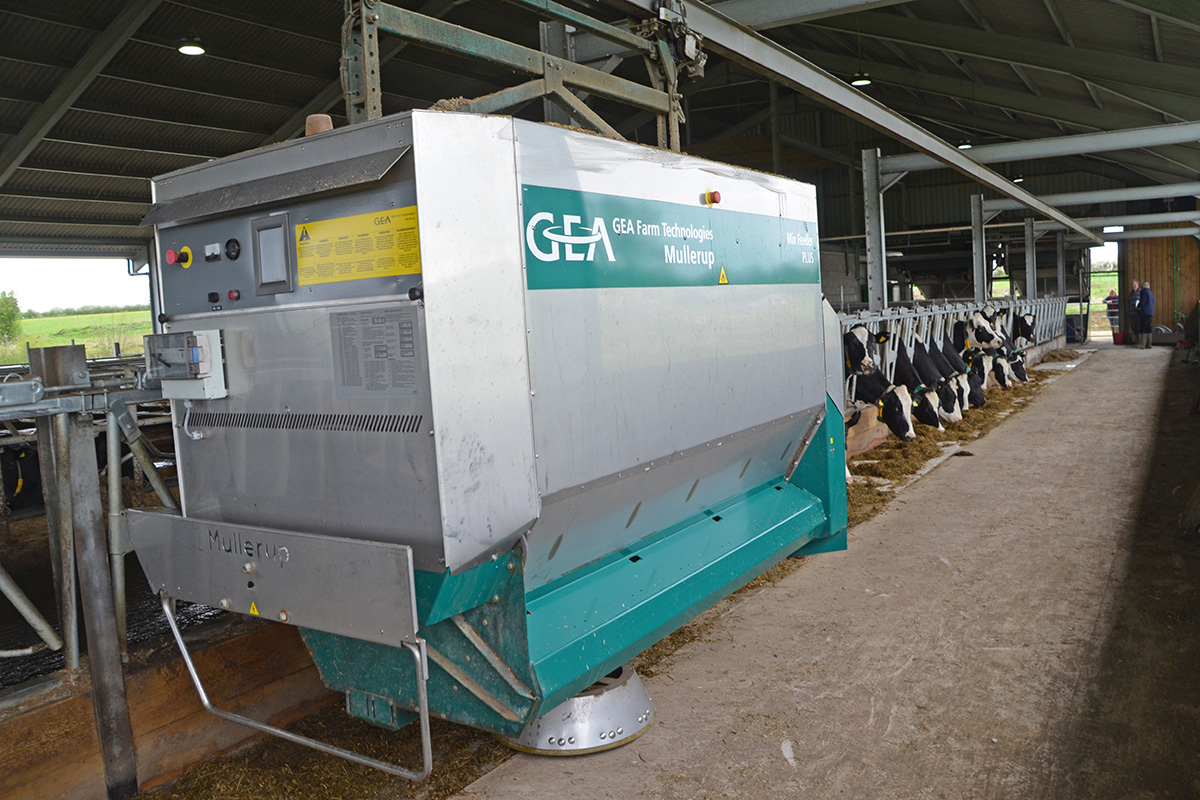
The GEA Mullerup MixFeeder runs along the feed barrier on an overhead monorail, returning to the filling station for loading, mixing and a battery recharge.
If the robot struggles with attaching the cluster, it will make three attempts before sending the cow out to go back around the building for a second run. If this occurs it sends out an alert to the herdsman’s smartphone. It’s a similar story with animals showing any signs of unusual behaviour. The Cow Scout collars constantly monitor the cows’ movements even down to how long an individual’s head is down eating at the feed barrier. If one has not been eating as it should, it sends a message so that she can be checked and any potential problems are picked up earlier than they might otherwise be.
The collars are also the key to heat detection. Increased activity from individual animals is monitored and if it persists, the cow is separated off into a separate holding pen the next time it goes for milking, with a message sent allowing her to be inseminated as required.
But it was about more than all the clever bits of kit. Making a robotic milking system work is, in Mr Hobbis’ opinion, all about cow flow (he’s even written a research paper on the subject).
“Many of the robotic milking systems on the market use aren’t set up with cow behaviour in mind. Free access set-ups are great in principle but after a while animals get lazy and will just mooch between the feed barrier and the cubicles, avoiding the robot with the result that you have to go and fetch cows for milking,” he says. “A one way system avoids this because the cows have got to pass through the milking area to get to the feed and rest areas.”
Central to the system is a sorting gate at the exit from the cubicles that either allows cows into the milking area for access to the robot or sends them straight to the feed barrier. Once in the feed area, one-way gates keep them there or allow them to return to the cubicles. When cows exit the robot they too are sent straight to the feed barrier, encouraging them to eat and therefore stay standing for a while before going through the one-way gates to lie down. This small detail is critical in maintaining udder health – it takes 20 minutes for the teat canal to fully close after milking. So if an animal goes and lies down immediately after exiting the parlour or robot, the risk of bugs and bacteria entering the udder are increased. Mr Hobbis believes the one-way system at Wapley Hill Farm is a big factor in the unit’s low cell counts and bactoscan readings. In fact, there hasn’t been one incidence of mastitis in the cows since the building went up.
The other big contributor to this is the frequency of milkings. Cows average 3.5-3.8 milkings per day, with the result that infection has less of a chance to build up with shorter intervals. Milk conductivity testing aids in early detection but hygiene is the other key factor – the robot flushes and disinfects the cluster between each cow.
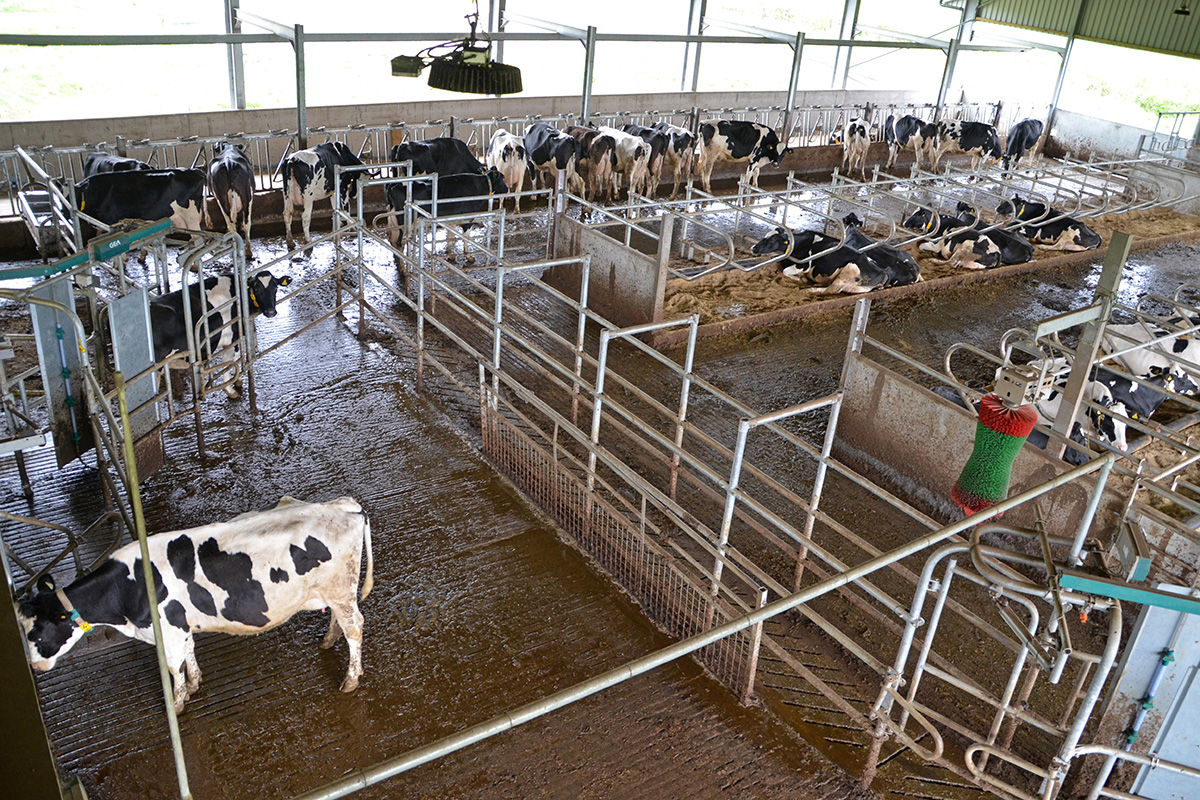
Key to the success of the whole system is cow flow according to Mr Hobbis. Central to that is the selection gate in the bottom right of the picture. This either allows cows through into the waiting area for the robot or, if they don’t need to be milked, sends them up the race to the feed barrier.
The Gea Mullerup MixFeeder is one thing that really sets the Wapley Hill set-up apart from other robotic milking units in the UK. Running on an overhead monorail, the miniaturised mixer wagon massively reduces the time and labour input spent feeding cows. Two large feed bunkers are used to hold bulk loads of forage – grass and maize silage typically. In addition, there’s a blend bin, a molasses dosing pump and a mineral hopper that are all linked in to the automated feeder’s control computer. When it parks up at its charging point at the end of the monorail, a pto-type coupling links it up to a 12hp electric motor which powers the rotor on the bottom of the mixer body. Each ration ingredient is then metered in automatically before the unit sets off on its next round of feeding.
“The feeder is capable of running up to nine times in a 24-hour period which has a big impact on cow health. Because they’re getting fresh grub little and often they’re gut is never overloaded and they’re not bossing each other about or sorting through the mix,” notes Mr Hobbis. “The sweeper wheel on the underside of the feeder means any left-overs from the last round are pushed in front of the cows for them to clear up before the next load is fed out.”
Of course it’s not all about the flash technology. Although standard in many ways, the building structure has even been designed with cows in mind. In combination with and open ridge, the 20°. pitch roof is reckoned to be near perfect for airflow, winter and summer. Clear roof panels were avoided on the basis that they would contribute to heat build-up when it’s not wanted.
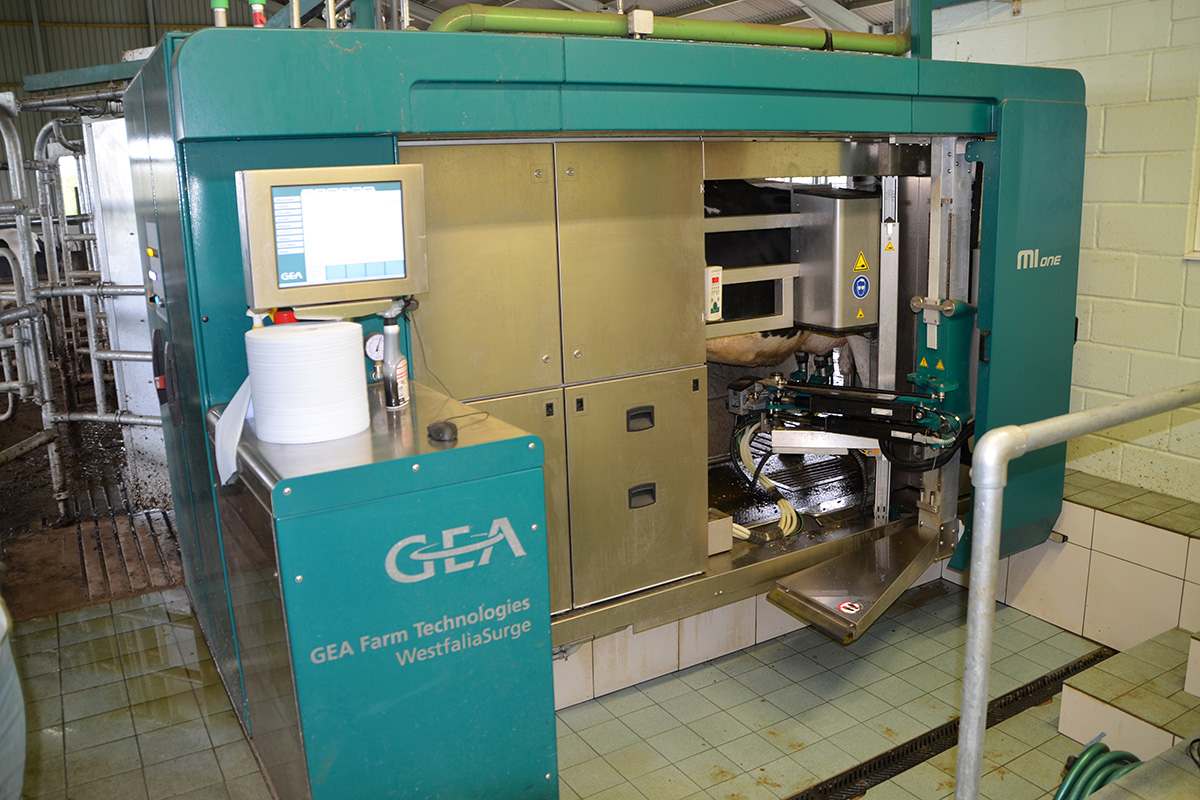
With a regular maintainence package in place, the Gea MI One robotic milker has proved to be reliable, comfortably handling 50 cows each visiting three to five times per day.
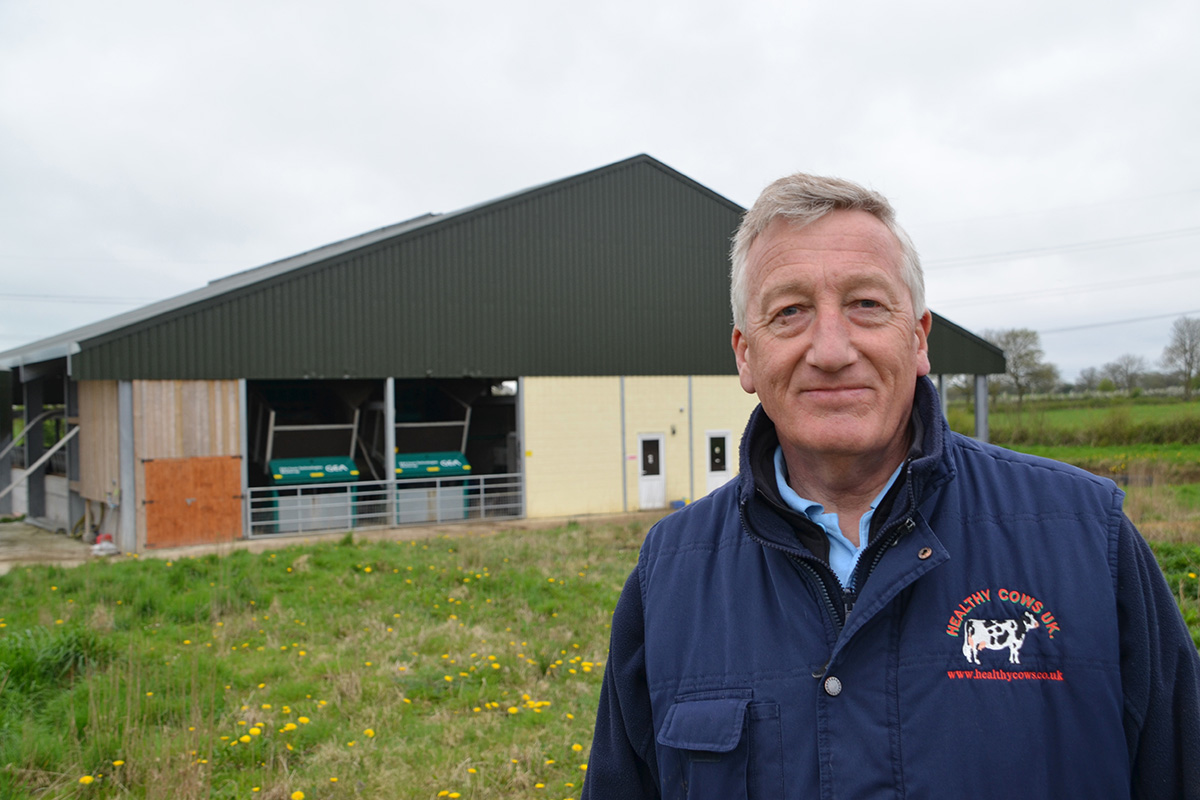
Having spent the best part of £500,000 on his state-of-the-art robotic milking and feeding set-up, consultant Mike Hobbis has achieved his goal of creating the UK’s most modern dairy.
With renewable energy produced on site the building is instead kept bright with high-tech LED lighting. Run in two circuits, for eight hours at night the ones over the cubicles shut off completely while those over the feed passage remain on at a low level.
But all this ultra-modern automated technology comes at a cost. How can it be justified on such a small-scale unit? In total Mr Hobbis spent almost £500,000 on the greenfield set-up. A good chunk of that went on the robotic milker and the automated feeder.
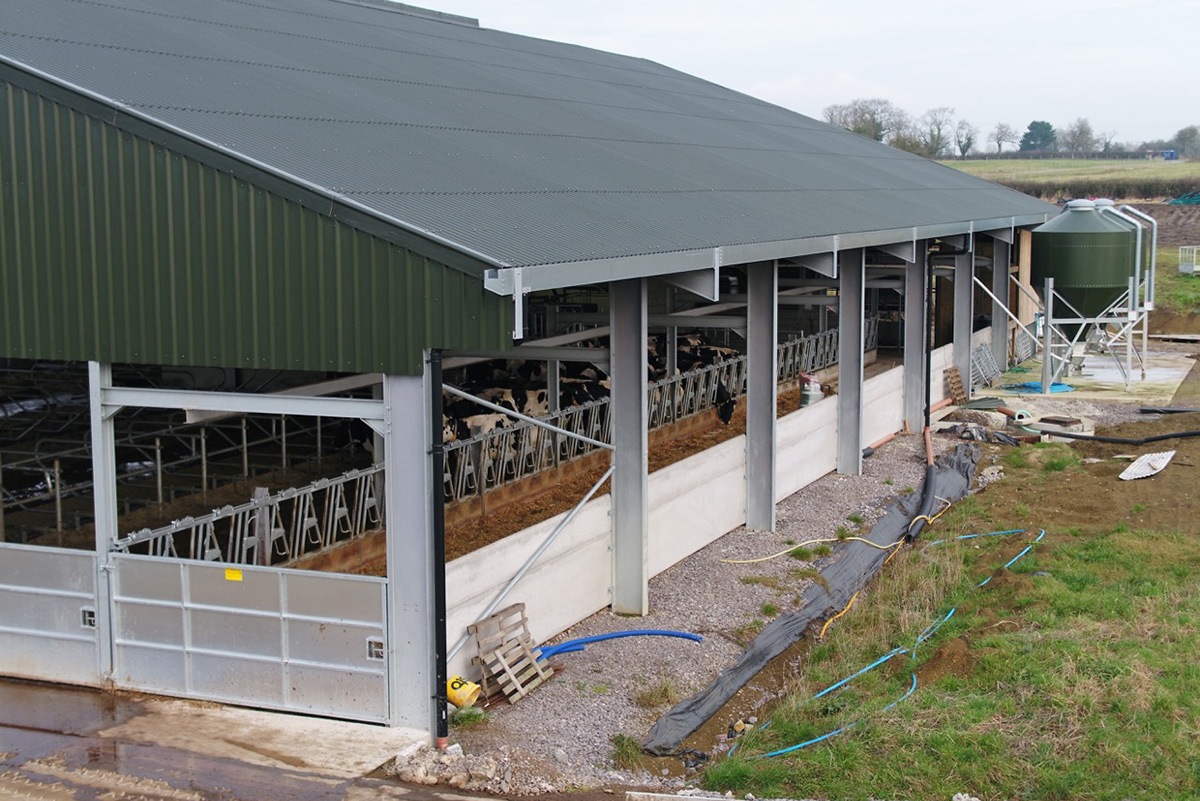
At 20° the roof pitch is steeper than standard and the ridge is left open to encourage good airflow. Clear roof sheets were avoided to limit heat build-up in the summer. Instead intelligent LED lighting is used to keep the building bright for a steady 16 hours a day, year-round.
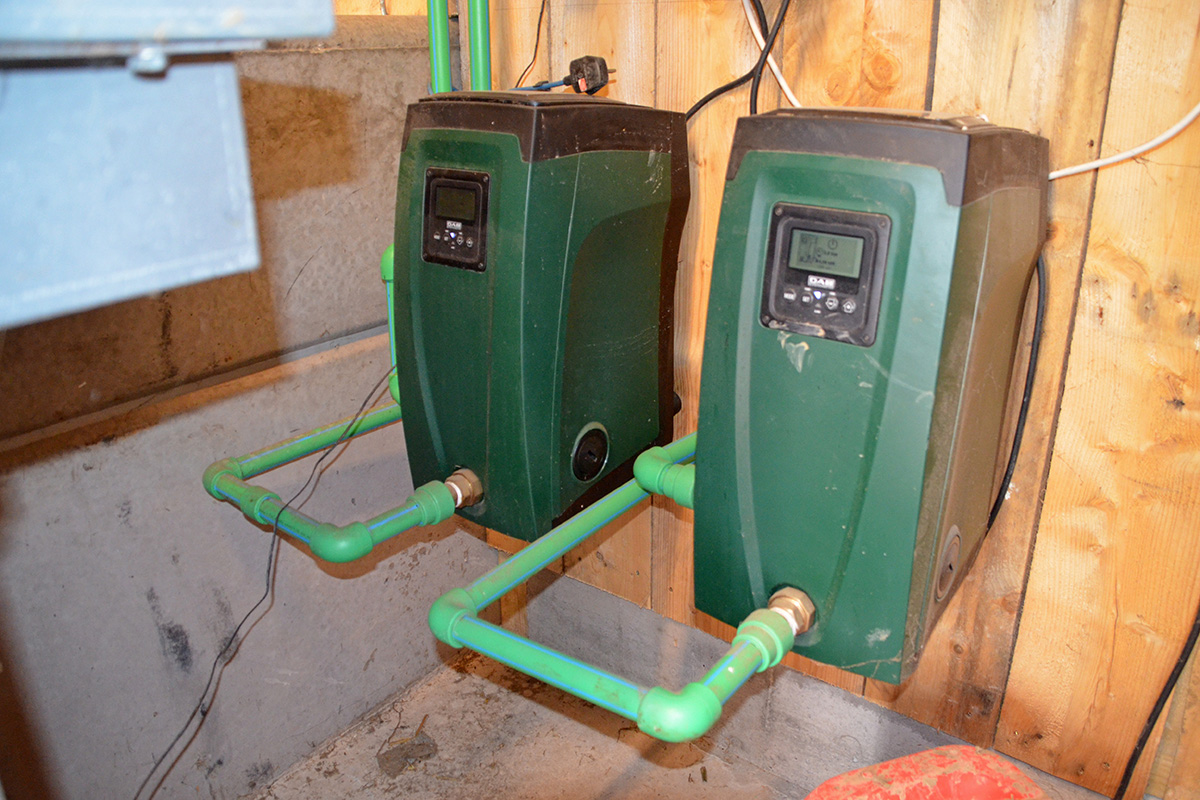
Rather than big pressure vessels and tanks to ensure wash water arrives at the robot at the correct pressure, Mr Hobbis tracked down these small pressurization units. All liquids are moved around the unit in frost-proof pipework. Using solvent weld fittings, he was able to do the plumbing almost entirely himself.
“Any herd this size would struggle to provide someone with a proper full-time income so to make it work you’ve got to have the time to go out and earn money off-farm. To do that you’ve got to massively reduce the labour requirement and the technology has allowed me to do that,” he says. “But when you start to peel back the layers it’s not quiet as extravagant as it might seem. For example, the automated feeder cost significantly less than you’d spend on a tractor and mixer wagon and that’s before you’ve factored in the cost of something to load it with.”
Having spent the last four years designing, building and tweaking the system, he has now taken a step back allowing a neighbouring farmer to rent the whole set-up to experience what running ‘the UK’s most modern dairy’ is like.
“In investing in the most advanced technology I not only hope to secure an income for my retirement but also want to provide other people with the opportunity to come and learn about this state-of-the-art kit and how it could help them with their businesses,” he explains. “Critically I hope it will arm them with the right questions to ask if they’re thinking of putting in robots: How many milkings per day are the cows averaging? How many cows need fetching each day? What do you do with cows the robot can’t attach to?”
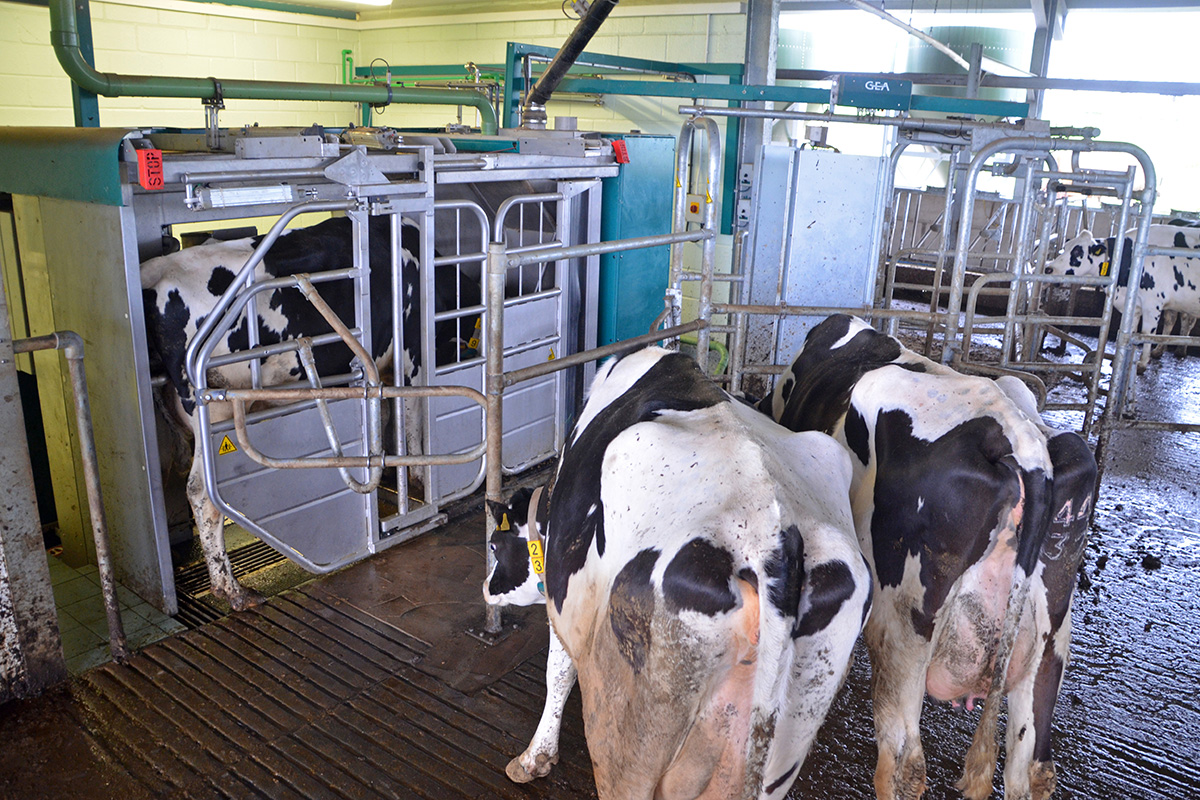
Milkings take an average of seven minutes per cow so animals in the waiting area aren’t hanging around for long
Summary
What Mr Hobbis has put together at Wapley Hill Farm is undoubtedly impressive and it certainly looks likely that he’s achieved his goal of building the UK’s most technologically advanced dairy. Equally as impressive is that fact that the unit is totally self-sufficient in energy – in fact 90% of the electricity generated by the 100kW turbine is exported to the grid.
The single box milking robot does the job as it should, so long as it is maintained on a regular basis. Cow collar activity monitors mean remote heat detection is a reality as is identifying any animals that might be off their food or under the weather.
Perhaps the piece de la resistance is the automated feeder which massively cuts the labour input required and means the cows have got fresh grub under their noses up to nine times a day. All these factors have meant it’s been possible for Mr Hobbis – and now the unit’s tenant – to work away from the site, only spending a minimum of time doing the daily chores.
This article was taken from the June 2018 issue of profi magazine. For more like this plus the latest news from the agricultural sector, visit the profi website and subscribe to profi magazine here.