Seka’s retrofit air filtration kit sets out to improve operator health. We see what it offers and how the maker adds one to a Fendt 742 Vario
Tractor and sprayer cabs have long since used seals, filters and fan(s) to lift cabin pressure over that of outside air. The notion is that dust can easily get in, so the operator breathes clearer air. It works; at least until seals age and/or maintenance standards drop. Yet even most factory-fresh conventional systems have limits. Their relatively simple intake filters can’t handle very fine dust. Neither can they extract gases; vapours (that is, molecules from a liquid or solid diffused in air); aerosols (solid or liquid particles suspended in air), or stinks in general.
There’s a Standard for that
Before seeing how Seka’s systems might help, consider BS EN 15695 1-2. This little number is in two parts. The first splits machine cab type into categories 1-4, with Cat 4 at the top. Cat 2 cabs protect against dust. Cat 3 cabs keep out dust and liquid crop protection products, while a Cat 4 cab handles dust, liquid products and their vapours. Cat 4 protection is needed with pesticides which expose the user to risk or harm while outside the cab; and where specific air contaminants occur in buildings, composting facilities, waste management plants and quarries. In the UK and Eire only some sprayer cabs in agriculture and horticulture meet Category 4 out the gate, and few others can be upgraded at the time of ordering. The second part of BS EN 15695 1-2 deals with air filter properties, test procedures and marking.
Normally, existing cabs in Categories 2 and 3 can’t readily be upgraded to Cat 4. But a couple of companies produce retrofit solutions: Seka is one. Its SBT 50 kit suits machinery in agriculture, fruit growing and viticulture, with the only requirements a cab with aircon and the application of around €6,100. The bad news? Currently Seka has no UK agent – though that may change – and does not supply kits for DIY fitment.
What’s involved?
The SBT 50 is a smaller version of the company’s typical industrial package. For spraying the minimum cab pressure needed is just 20 Pa over atmospheric, says Seka, with 50 Pa an upper limit. Below 20 Pa the operator gets both a visual and audible warning.
The most obvious bit of the system is a stainless steel housing with an external fan. This means that pressurised air is blown, not sucked, through the whole system, so contaminated air should always stay outside the cab. Inside the stainless housing is a cyclone to separate larger dust particles, then two cartridge filters. The first filter has a glass
fibre-based element to take out very fine material; the second uses activated carbon to extract gases, vapours and odours. All but a tiny fraction of incoming air goes through the filters, which Seka reckons do their job around ten times more effectively than a conventional FFP-2 face mask. If full-house protection is not needed, the unit can run with just the dust filter in place.
Cleaned air then goes via a hose to the cab’s standard filter housing and onward to the cab’s existing ventilation ducts. A small display keeps on system performance, warning if cab pressure drops quickly, if filters need changing, and overseeing fan operation.
HOW SEKA KITS OUT A FENDT 724 VARIO
1) MOUNT AND BASE PLATE
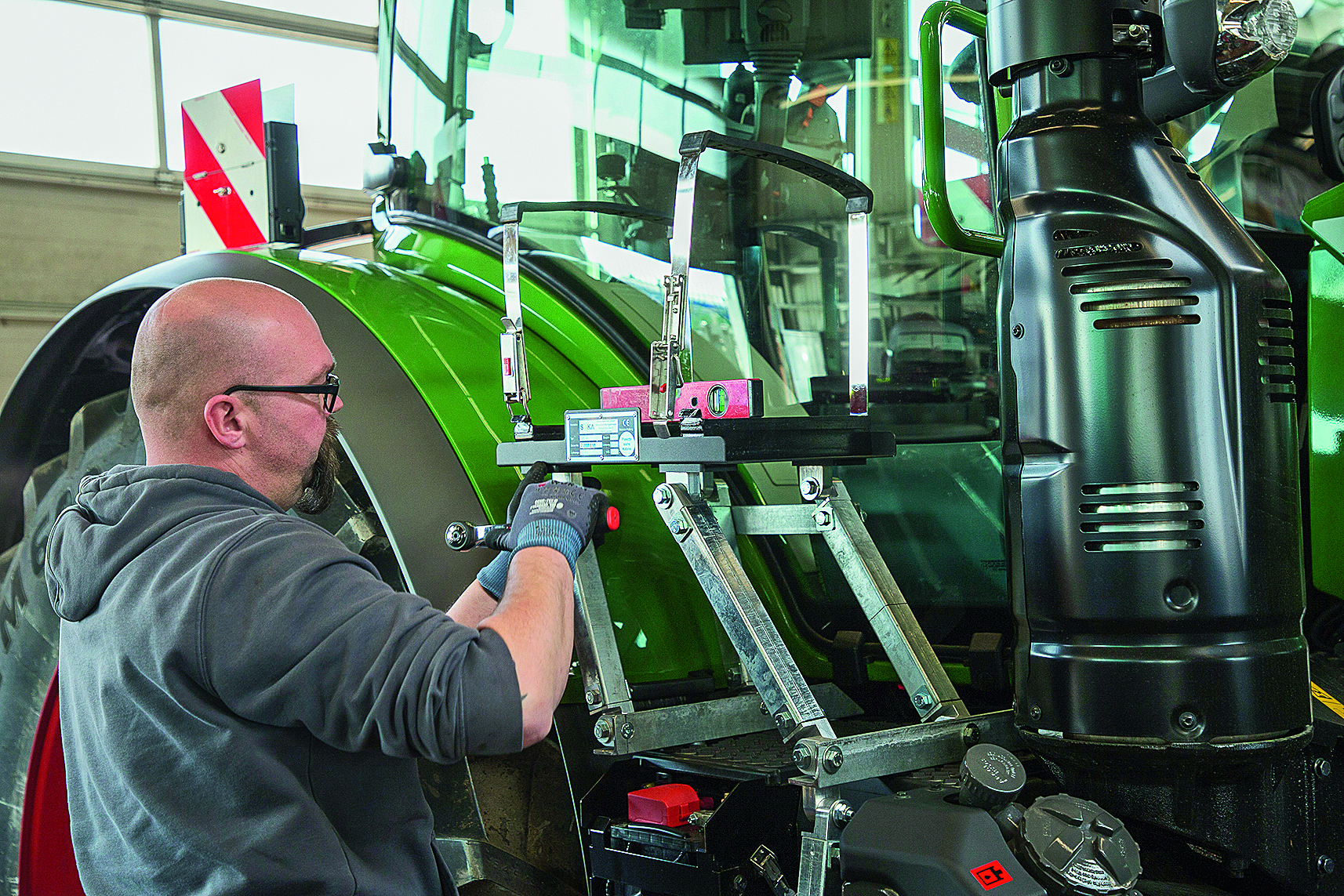
Seka’s modular mount can be built up to suit most candidate machines. Galvanised and held together by stainless fasteners, it carries the filter housing’s baseplate — in this case on the offside of the cab. Mount design has to take cab/ mudguard movement into account.
2) ON GOES THE FILTER HOUSING
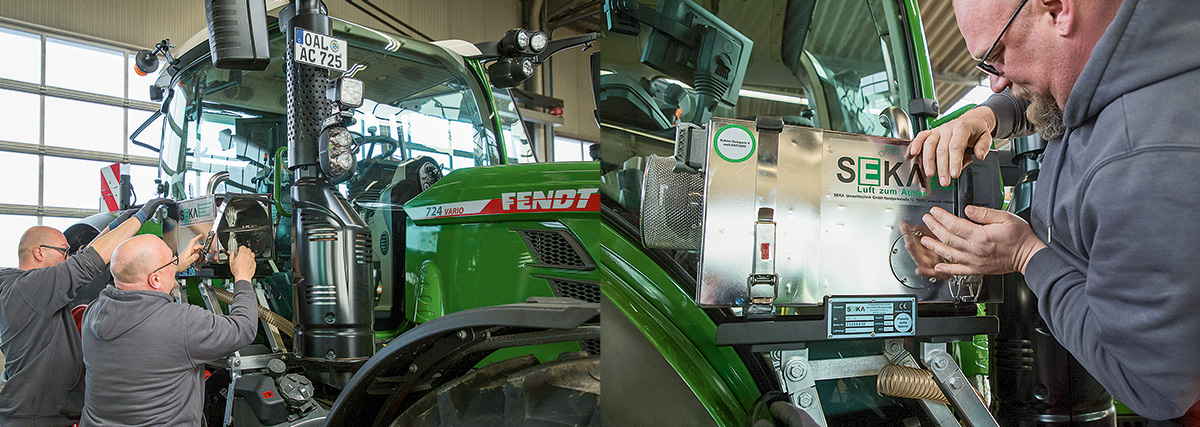
The sizeable stainless steel filter housing sits on rubber mounts and secures to the baseplate via straps and over-centre latches. Clearly, in this case the offside door can’t be used. That may already be the case where screens clutter that side of the cab, and is less of a problem where traffic drives on the left.
3) THE AIR SUPPLY HOSE
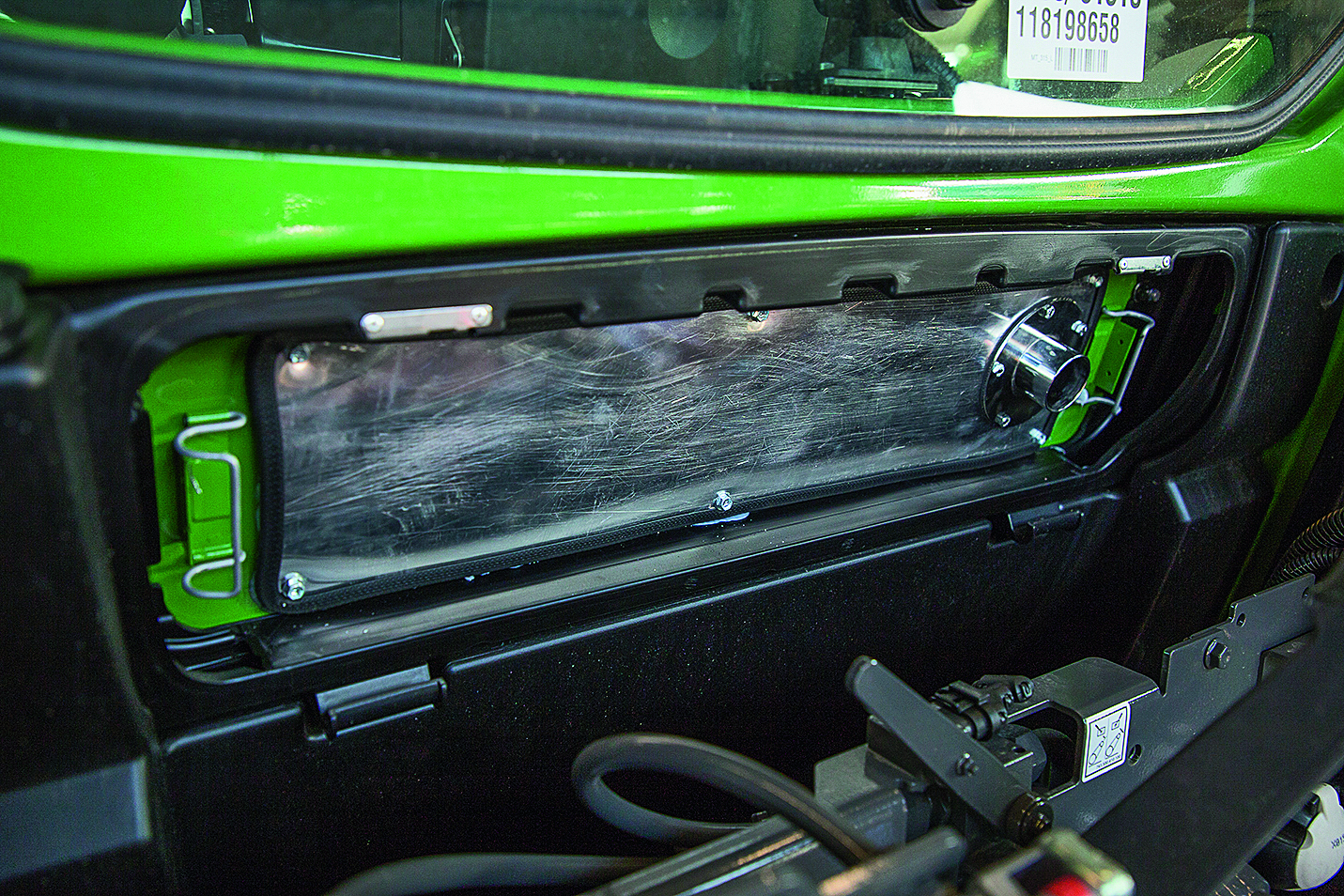
Filtered air under pressure goes into the cab at an existing filter housing. So out go the original elements(s), then the housing gets a thorough clean. Seka’s sealed blanking plate(s) will replace the original housing door; a stub inlet for the connecting hose can bolt anywhere on a plate, with a matching hole drilled to suit.
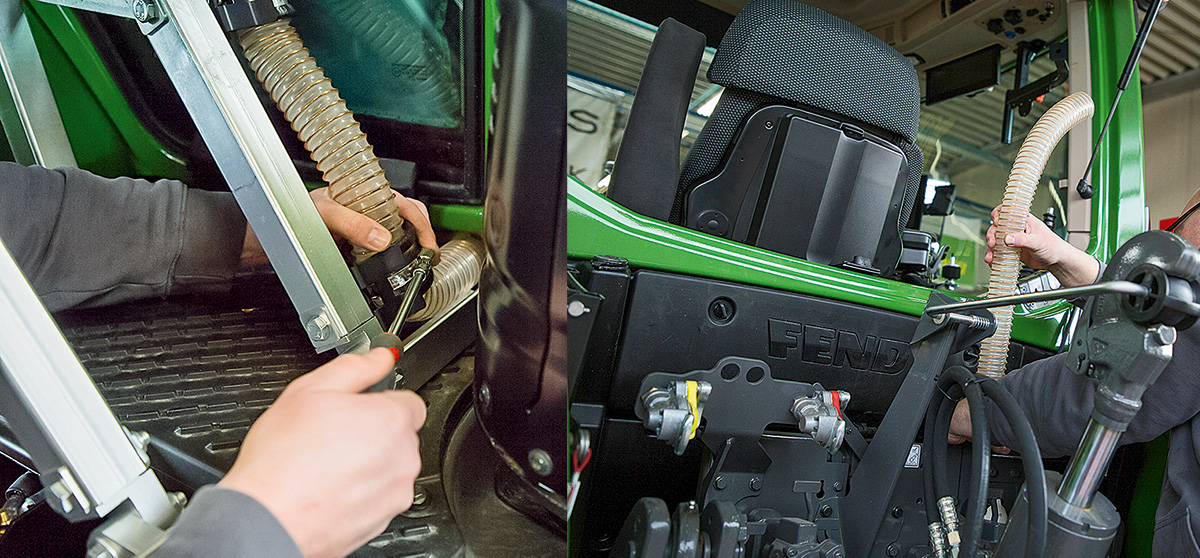
Next step is to route the reinforced 65mm ID feed hose between the external filter housing and the new stub, again thinking about cab movement and avoiding sharp bends.
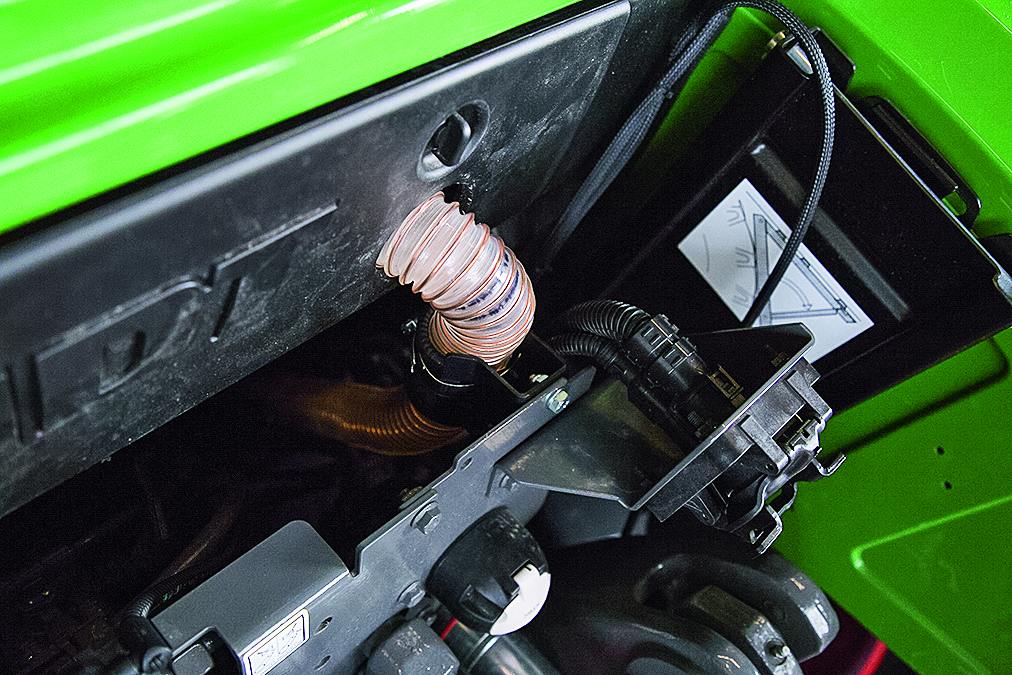
Trimmed to length and routed so it’s not flattened, the hose gets supports and clamps.
4) SORT THE WIRING
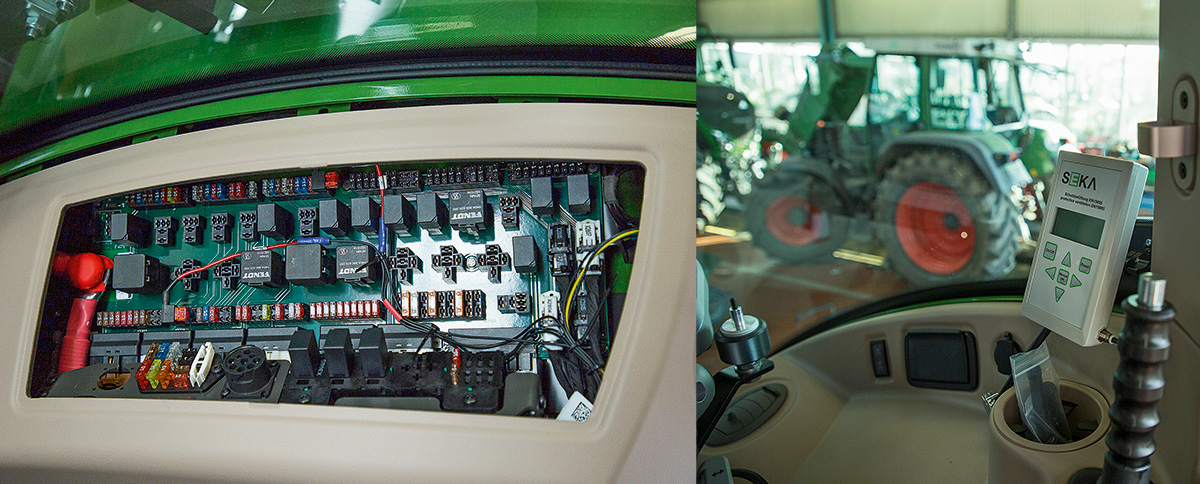
The cab display needs two 12V feeds — one permanent, the other controlled by the keyswitch. These came from the machine’s power distribution panel(s). Where this isn’t an option the new feeds must be fuse-protected, with any joints either soldered and shrink-wrapped or crimped with the proper tool.
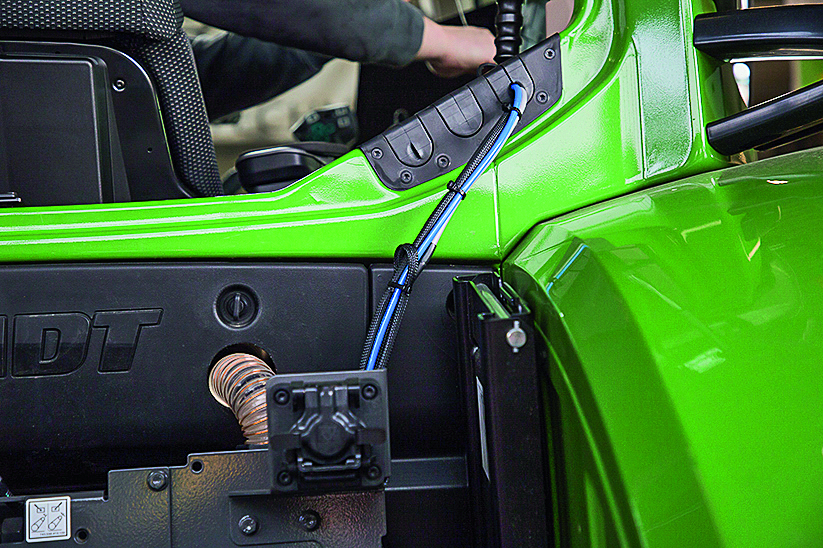
On this Fendt, the wiring harness runs from the cab to the filter housing through the rear window’s cable port. The blue item is a small bore hose communicating ambient air pressure to the cab display, allowing relative cabin pressure to be calculated.
5) FILTERS IN
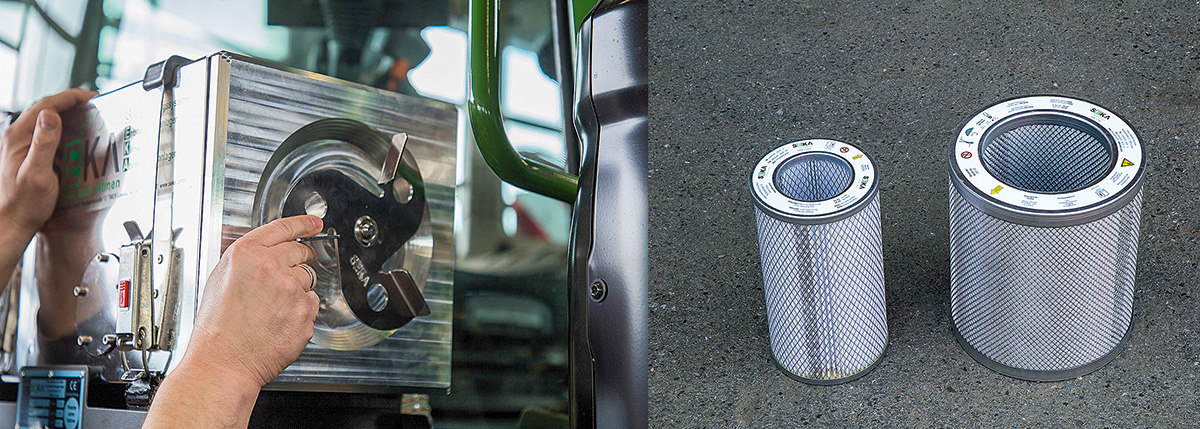
Two filters live in the housing. The outer deals with vapours, gases and bad smells; it’s filled with 4.5kg of activated charcoal granules. Storage life is up to two years in the original shrink-wrap, but once this comes off the filter should be installed right away. The inner filter takes out very fine dust, and must not be cleaned with an air line.
6 SEAL THE CAB
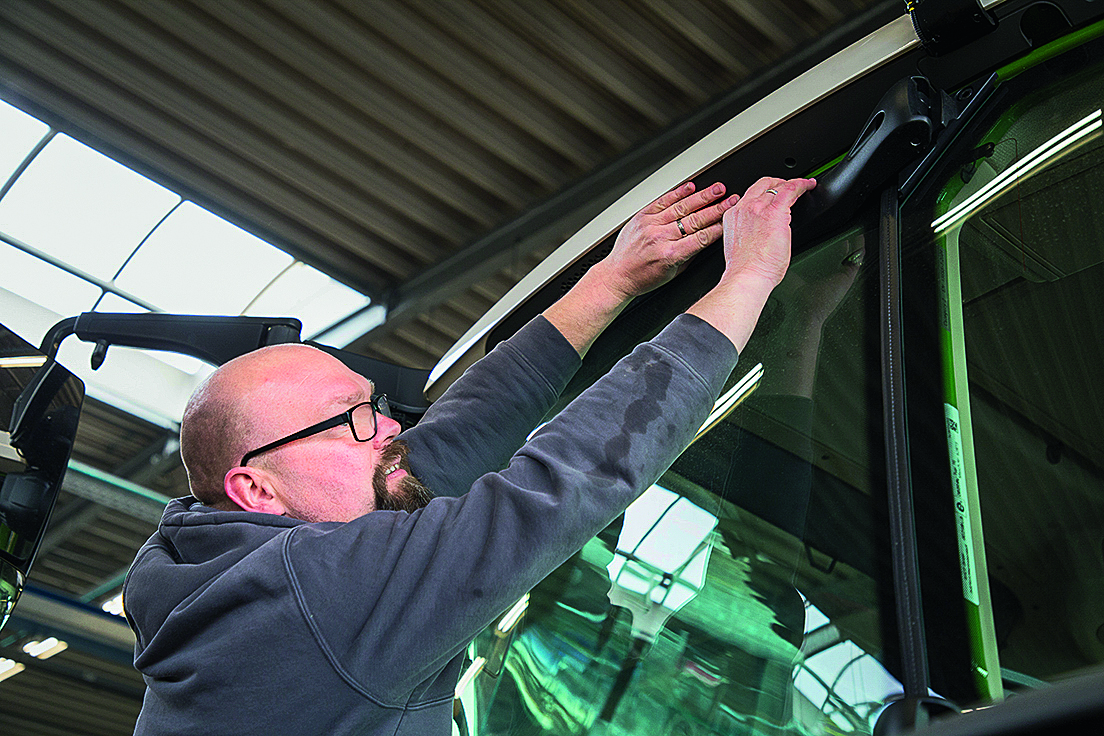
Seka finds that after an initial test, most cabs need further sealing. This is confirmed when either cab pressure takes too long to build or the fan has to work hard to hold positive pressure. Seka’s installers can usually find leaks rapidly, as air tends to leave from the same places.
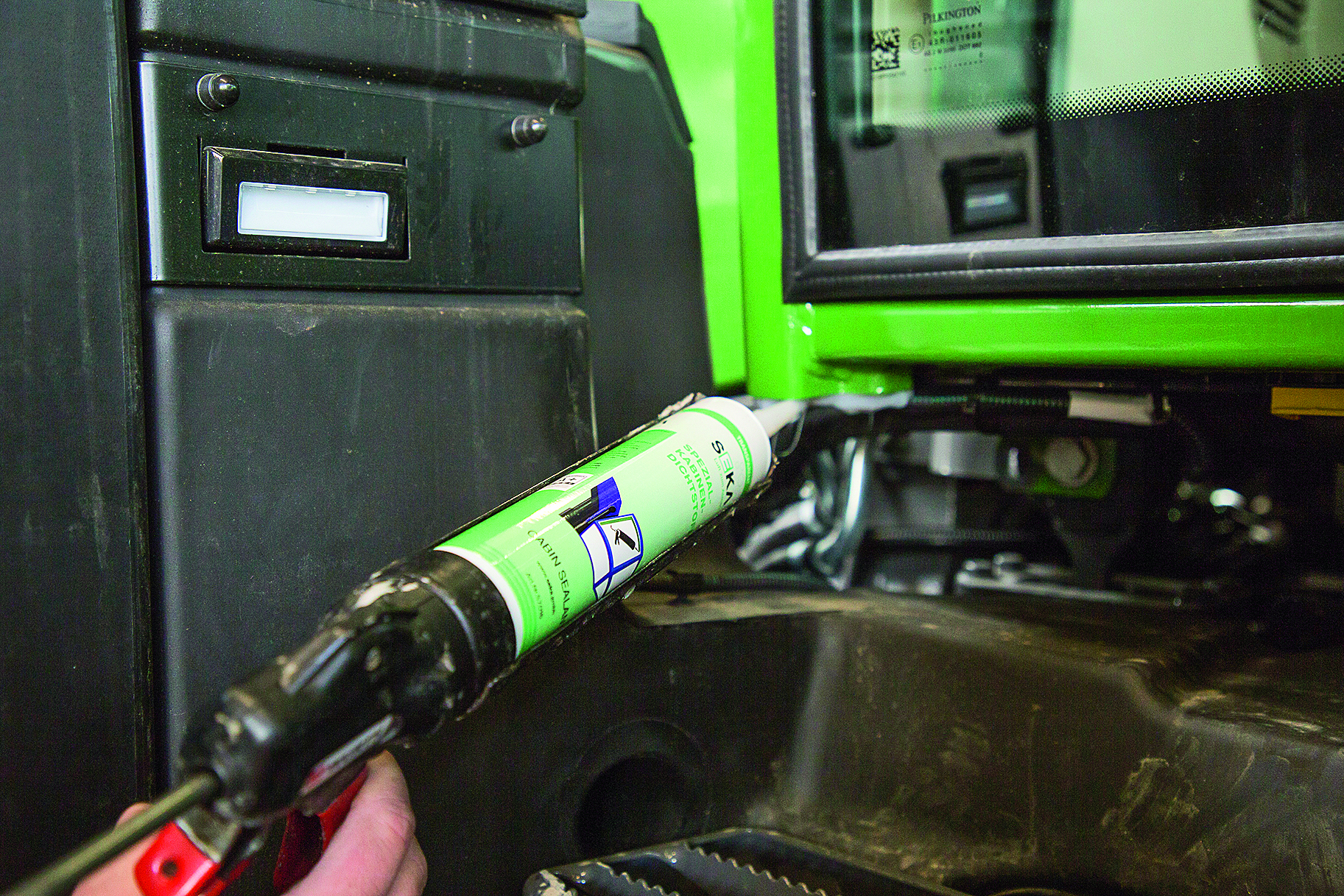
Seka uses a sealant that, unlike silicone, doesn’t smell or degas. Typical application points are around the cab posts and this cab’s pressure-equalising flap. After sealing, it’s likely that the cab door will be harder to close: a tip is to click it on to the catch’s first stage, then pull hard to fully close the door.
7) …AND TEST
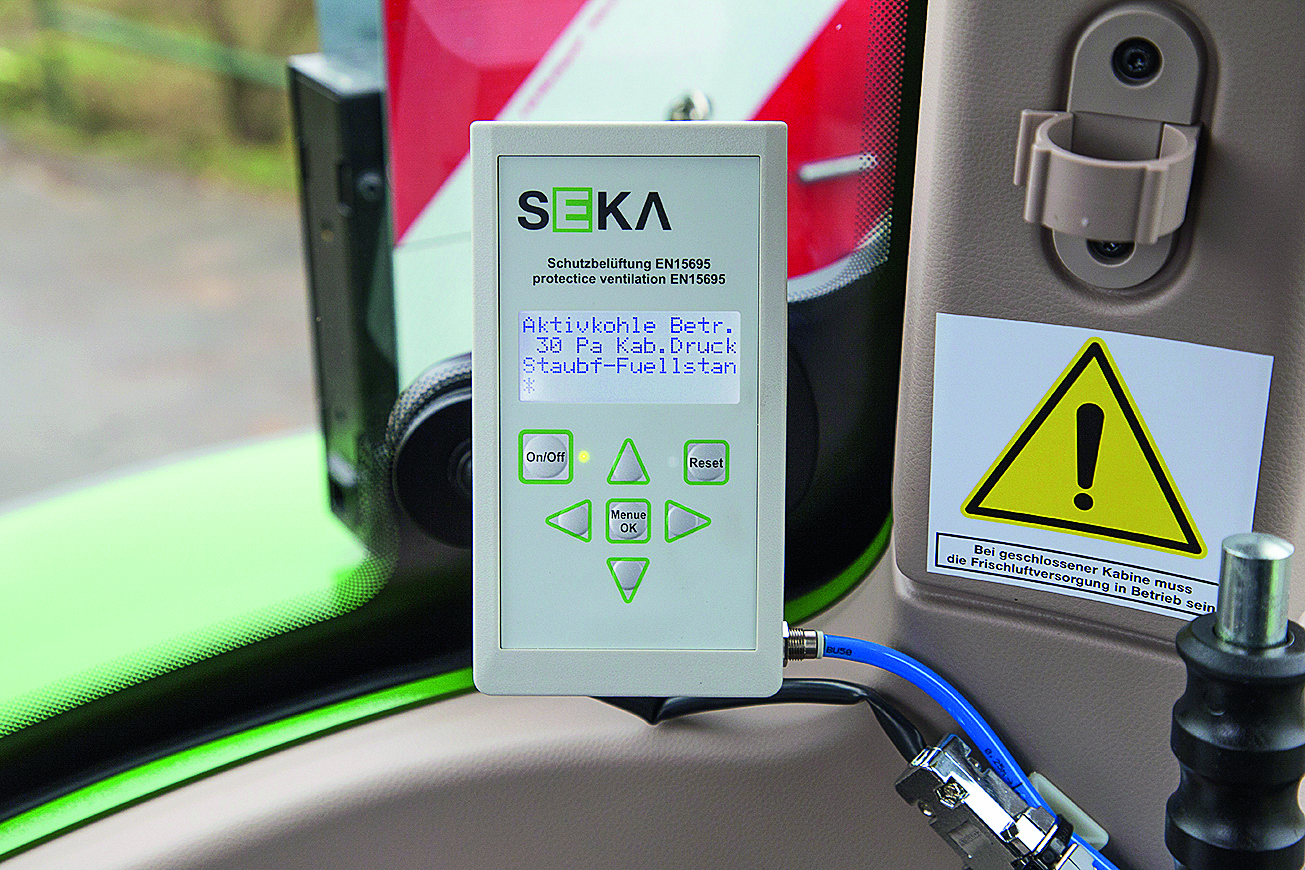
In this case the cab display confirms successful sealing, showing 30 Pa positive pressure. Should this suddenly drop the display will warn the operator. Tracking fan speed over time monitors filter condition — it rises to maintain cab pressure as the filter(s) fill.
Sprayer mounting an alternative
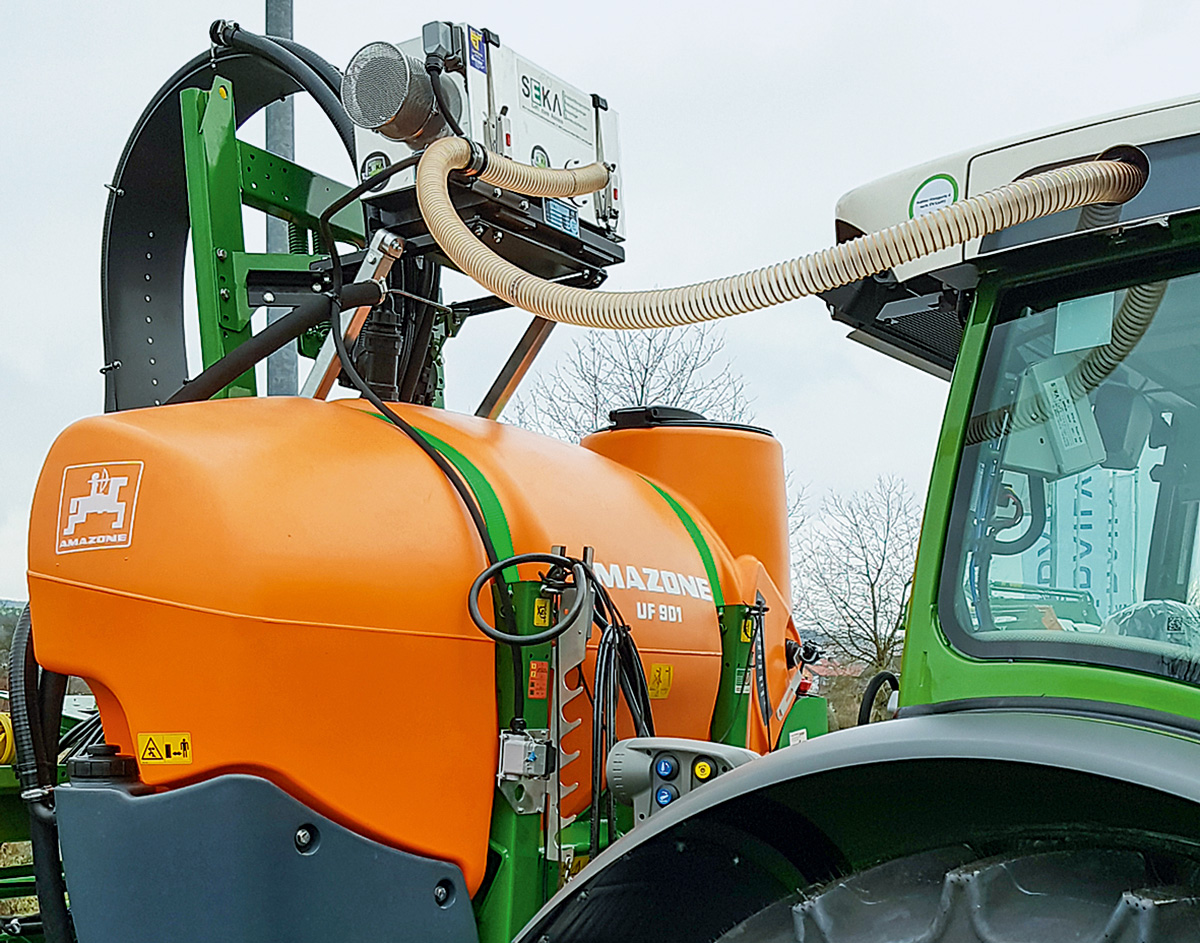
If you like to swap spraying tractors, the external filter unit can stay on the sprayer — although each cab will still need to be set up to take the system’s cab monitor and air/electrical connections.
This article was taken from the 01/2022 issue of profi. For more up-to-date farming news and reviews click here and subscribe now to profi and save 47%.