Danish potato grower Henning Thybo has a keen interest in developing specialist equipment for his own farm and has joined forces with manufacturers to find machinery solutions for the crop against a background of increasingly restrictive legislation in his country.
KEEPING IT BRIEF
- Adapting and developing machines to better suit the farm.
- Jointly developed a 12-row planter to match 12-row mechanical weeding
- Potatoes are grown for processing for starch production
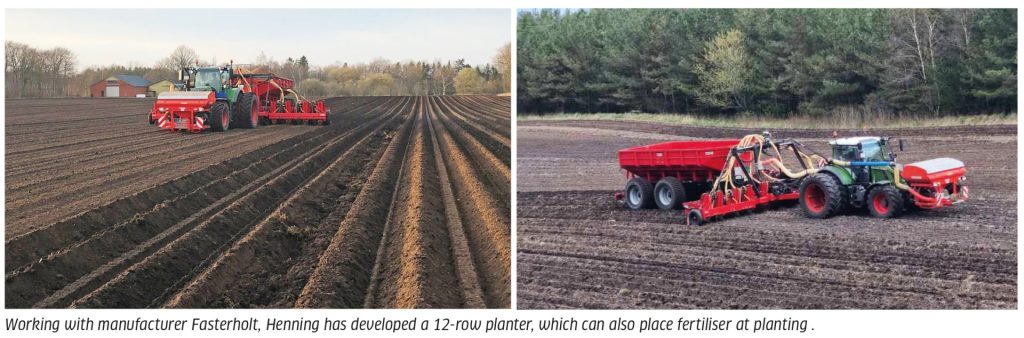
At Arnborg, 15km south of Herning, Henning Thybo crops 900ha, 320ha of which is potatoes, 70ha grass seed and the remainder malting barley; he is also vice chairman of the AKD Danmark potato starch factory and board member of KMC, a potato-based food ingredient co-operative.
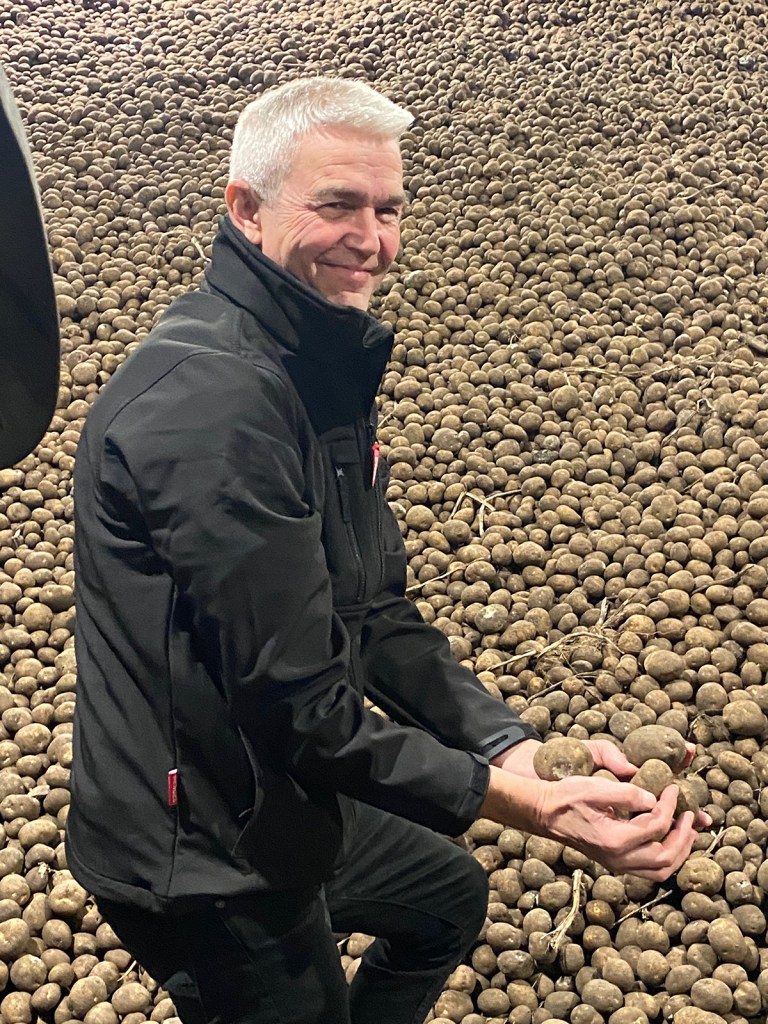
“My father was a dairy farmer, but I worked outside the industry until 1986, farming land that I’d purchased at Baektoft in my spare time. The opportunity came to buy more land and in 1996 I became a full-time farmer.”
Joining the board of the KMC co-operative, he saw the opportunity to specialise in the production of potato starch, the sandy soils and emerging processing facilities in the Herning area favouring this line of business. An increasing range of potato starch-based products on the market means growing demand, increasing the opportunities going forward.
The majority of the land is rented, with 200ha owned and there are six members of staff, more than he would like, he comments, but necessary due to the distances between some parcels of land. Pressure on land availability means that fields are cropped for potatoes one year in three.
“It was common to grow potatoes on the same land every year in this area, but disease became a problem, so it was extended to every other year and now every third.”
Growing nematode-resistant varieties is also a necessity in the tight rotation, rather than using chemicals, he notes. Yields are around 50t/ha, of which 9-10t/ha is starch, although wet conditions in 2024 have hit starch values.
No-plough
“We no longer plough potato ground but use deep harrows and incorporate slurry from pig farming neighbours,” Henning explains. “We also apply protamylasse, a waste water product from starch processing which offers 4-5kgN/tonne, 3kg P/tonne and 43kg K/tonne. This is put on with a 25,000 litre capacity tanker applying between one and five tonnes/ha with 24m boom. NH3 goes on via a 10 tonne bulk applicator with 7.5m spread width at rates up t 125kg/ha.”
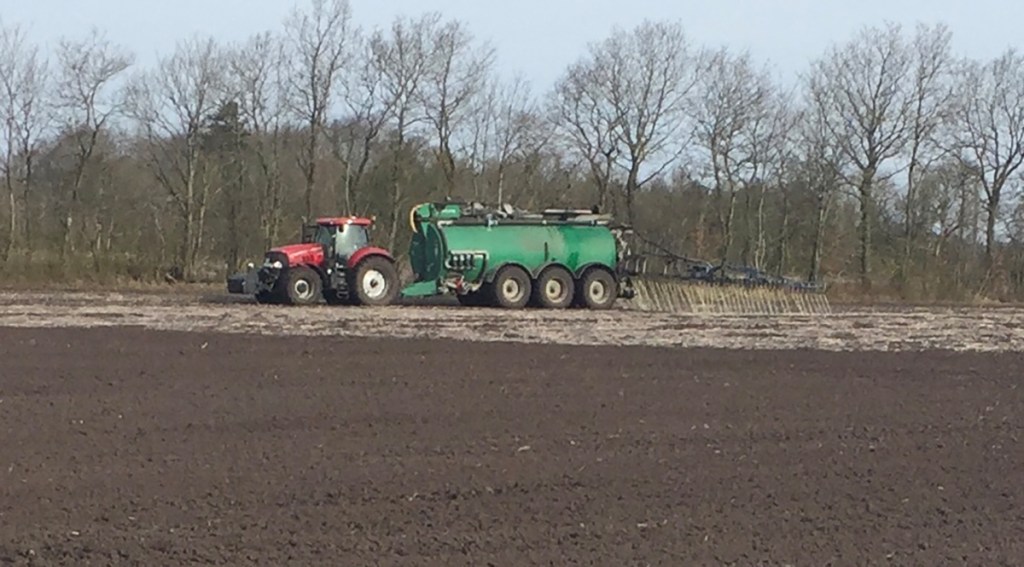
Some of his innovations are simple and practical – an 18 tonne trailer towed behind the spreader tractor and fitted with its own loading crane means less downtime and labour.
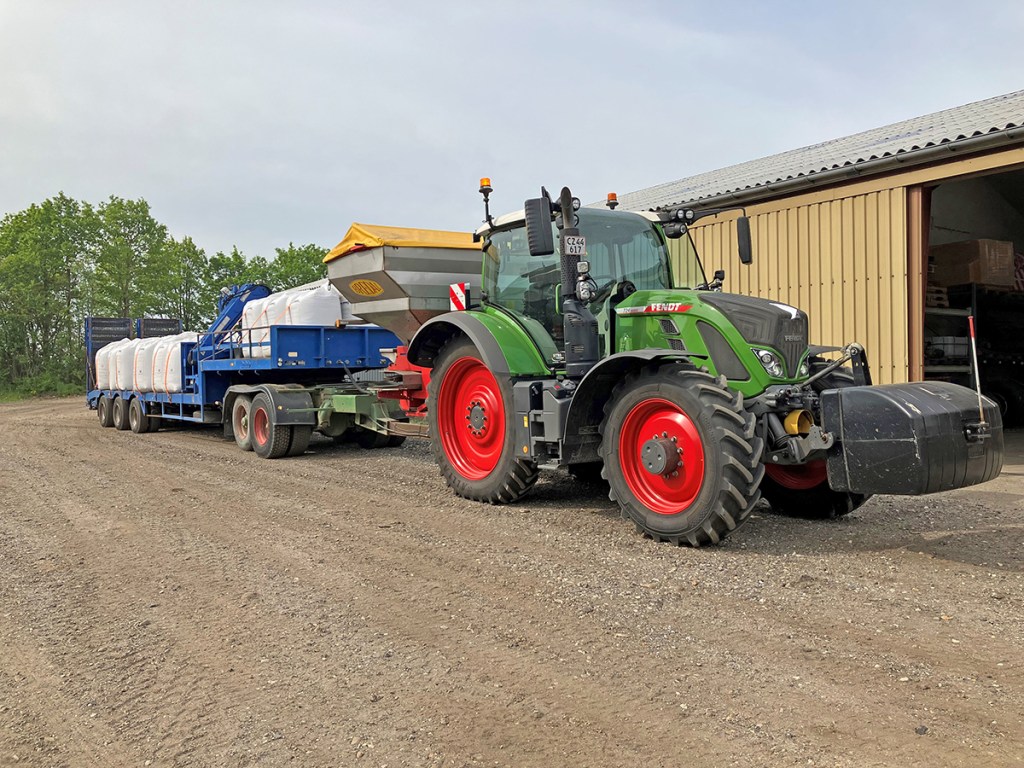
A 20:18:0 fertiliser product is also placed at seeding using a front mounted tank on the planter tractor at rates of 125kg/ha; Henning was an early adopter of autosteer using a satellite receiver on the planter itself for greater accuracy.
He comments that he would like to make more use of variable rate fertiliser application but feels that the technology is not there yet for potatoes. “However, we do take advantage of SEGES CropManager software which uses satellite imagery showing where more fertiliser should be applied for yield/ take-off from the preceding crop.”
Tailoring machines
In 2022, Henning worked with potato machinery specialist Fasterholt to develop a 12-row potato planter, complete with GPS on the planter to give the precision for easier weeding.
“We had a four-row planter and a 12-row weeder and they were impossible to get to work together, so I decided to design my own machine.”
Capable of planting 30-35ha/day, the 9.81m wide planter uses discs to control seed placement depth and has camera monitoring for blockages or skips. Seed potatoes are transferred from the 15 tonne hopper to the cups via a cross conveyor and fertiliser is blown from the front tank mounted on the 240hp tractor, which is shod with dual wheels.
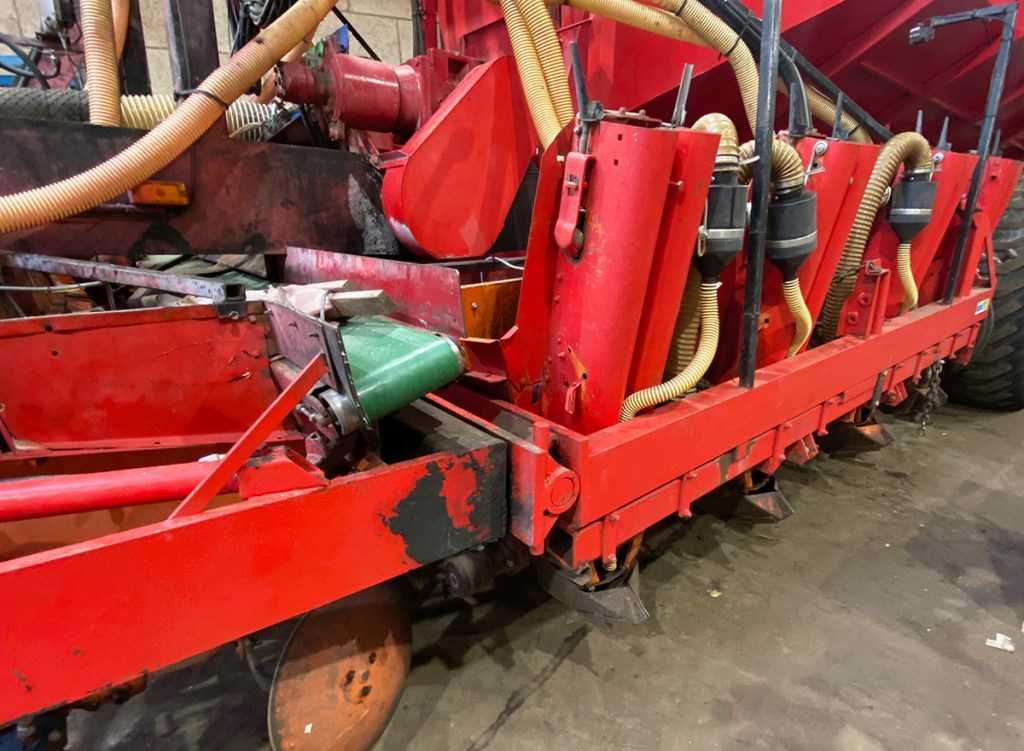
The planter folds to 3.9m for the road – in two minutes, says Henning – using a patented mechanism which places the planting elements alongside the hopper. Danish road rules allow a wider transport width compared to most of Europe.
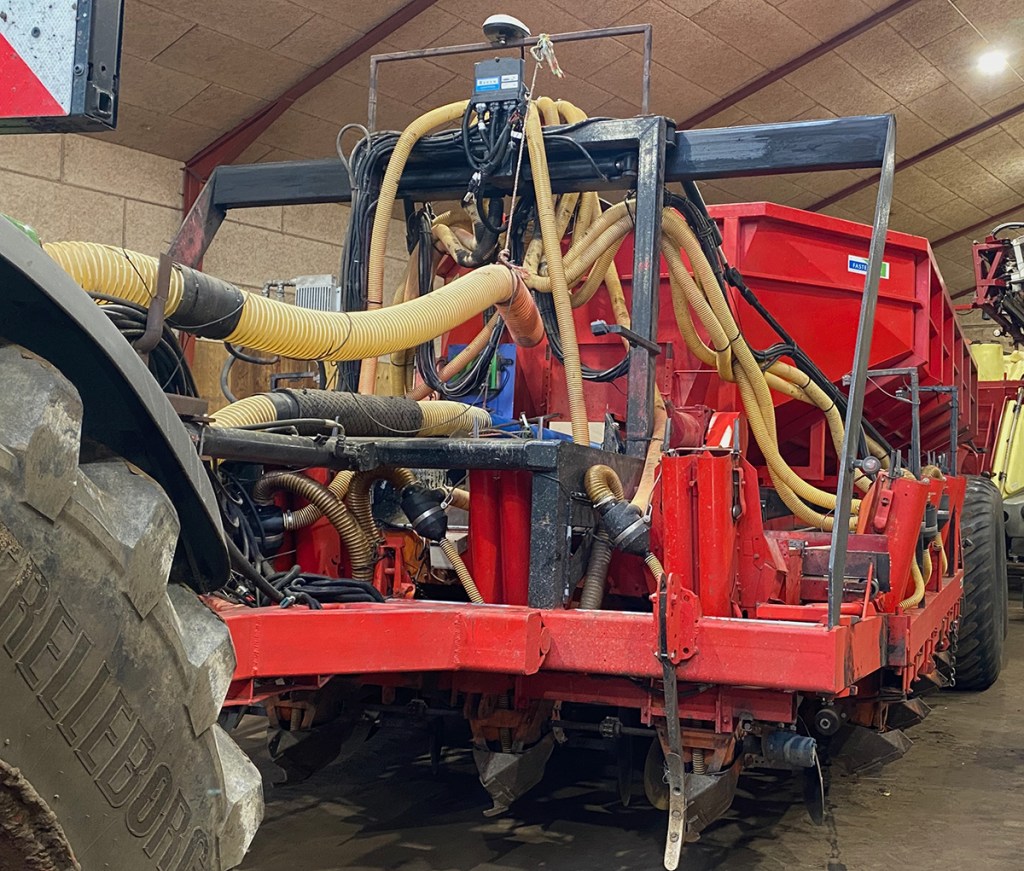
Mechanical weeding
Henning has also moved increasingly towards mechanical weed control, starting with a tined weeder which has been superceded by a more specialist implement. He is a partner in MSR Plant Technology with engineer Michael Stolbert-Rohr and Fasterholt and the company’s innovations have won several accolades at the international Agromek exhibition.
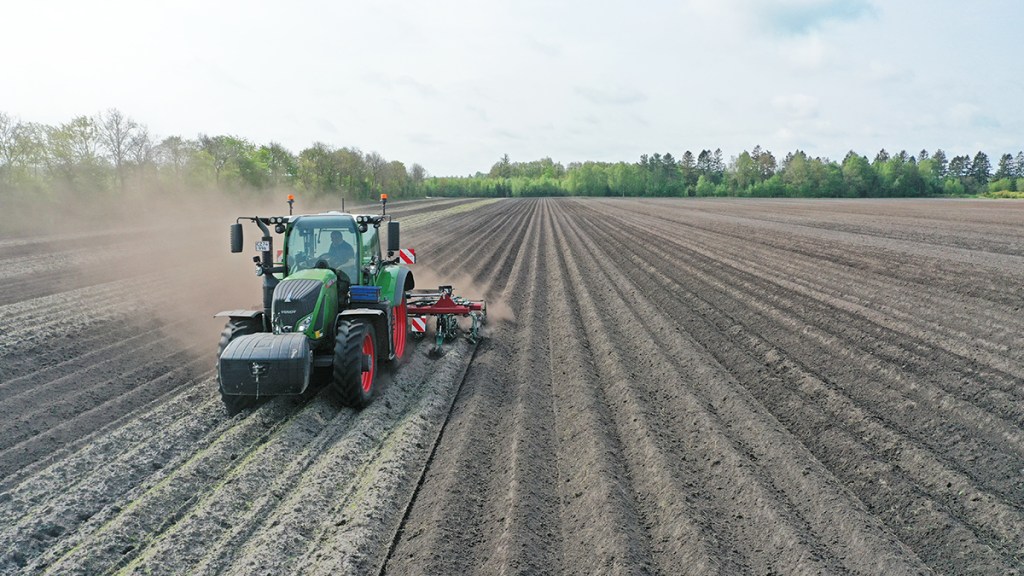
The Opti Weeder was developed specifically for weeding potato crops, and can be used throughout the growing season, tilling the entire ridge at 1-2cm depth before sprouting. It uses finger wheels and shares to weed between the ridges in the established crop, working to 1cm from the plants.
Updates to the machine since its launch in 2018 have seen the addition of fixed and flexible frame versions, the latter capable of weeding on slopes and around curves, and working widths up to eight rows. Capable of operating at speeds up to 20km/hr, the Opti Weeder offers high outputs where spraying is not possible or is ineffective.
“We can still spray but in 2023 we only used a small amount of glyphosate and this year (2024) no herbicide at all,” he explains.
Two passes are made before emergence, and he comments that 220ha weeded in 2024 were clean, but he saw the difference on 14ha where the weeder was used too late.
“It’s more flexible than spraying when you come towards harvest; when using chemicals we had to be aware of the withdrawal period but applying later fertiliser meant a weed flush just before harvest, which affects the lifting efficiency.”
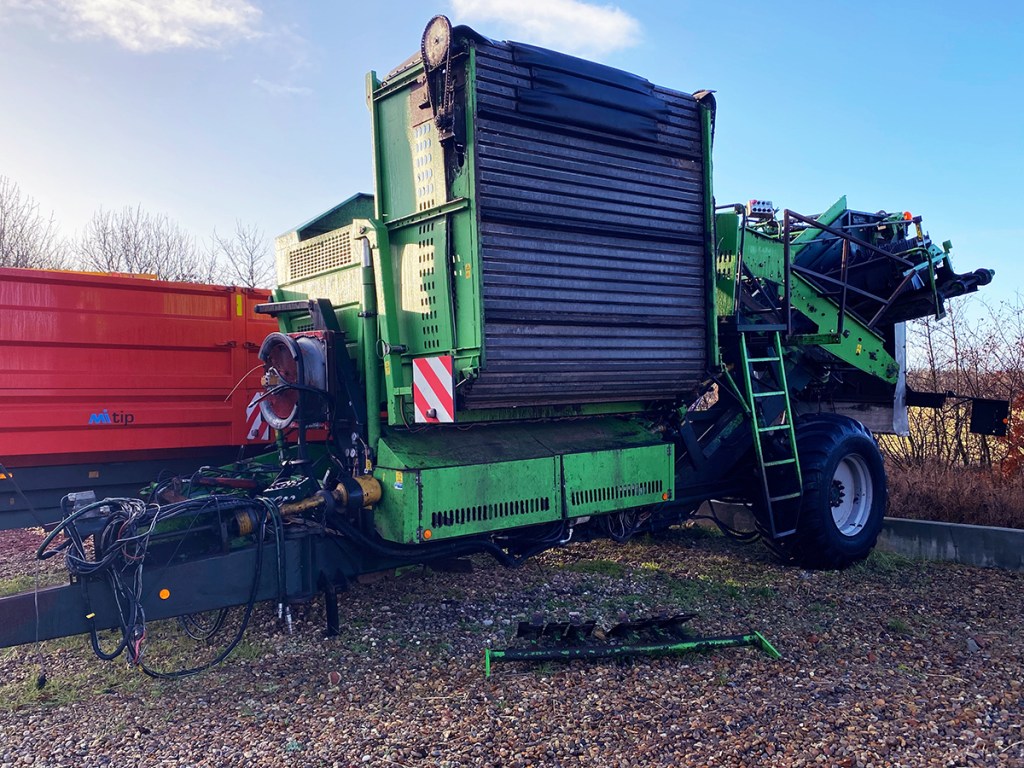
Making it rain
With such a large acreage of potatoes on sandy soil, irrigation is an important consideration, and the business owns 41 irrigators and rents a further 15.
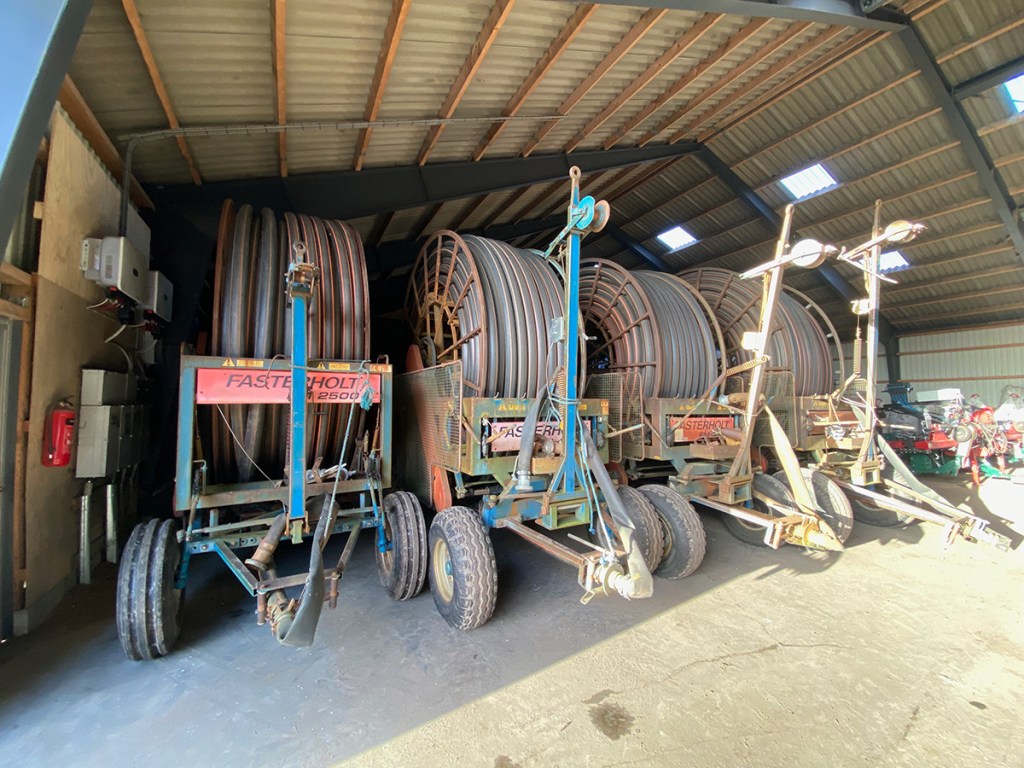
They are operated via the Raindancer GPS irrigation control system which switches on pumps for 18 of the irrigators as required while SEGES software offers monitoring of application plus recording of applications over a five day period to meet government traceability requirements.
“We use groundwater and have more than we need, but precision is still important – if we use too much, we lose fertiliser and if not enough, lose yield. We can also apply water variably according to the individual requirements of a particular sector.”
Henning has also worked closely with SEGES to fine tune the software to meet his needs on the newest machines but admits it’s still a work in progress.
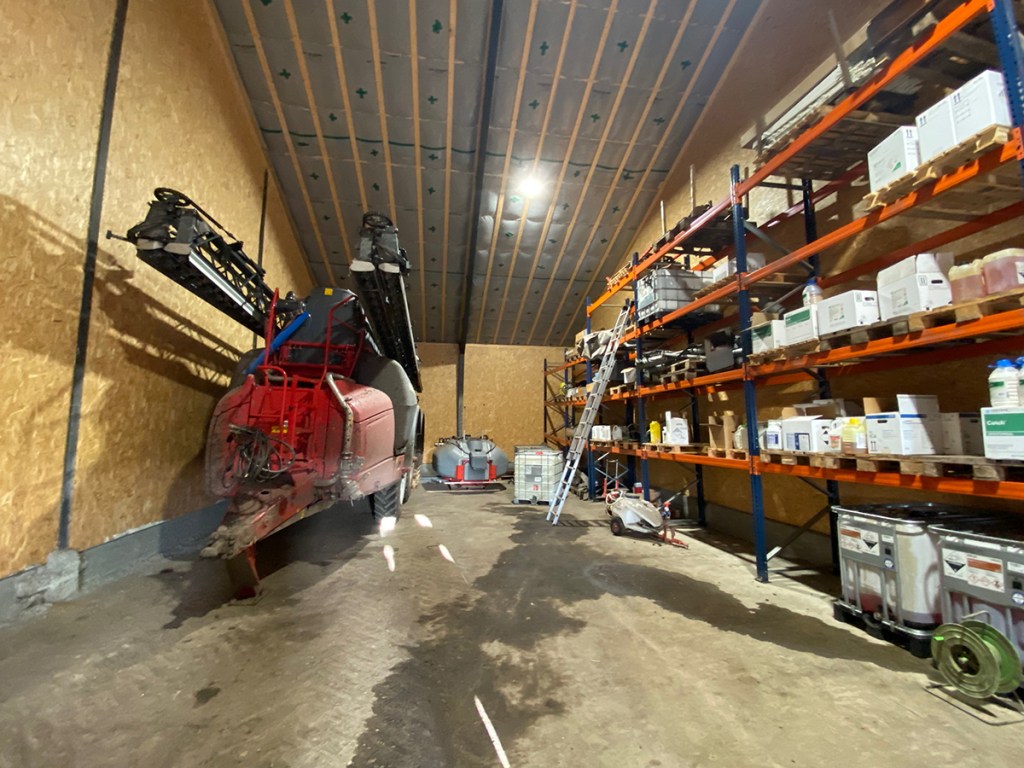
Under cover
A covered spray store is a relatively recent development, offering safer filling of the 36m Horsch trailed sprayer to meet new legislative controls against filling sprayers in the field and easier access to an adjacent 25,000 litre water store. Henning is keen on-site specific spraying but comments that the technology is not there yet.
“We are working with control of 3.0m sections which is not precise enough. I can see the benefits for cereals, but it only seems to be effective post-harvest at the moment. We’re looking at camera vision systems for next season, and we’re looking at any possibilities to reduce chemical use.”
He has also trialled fitting a weed wiper boom to the sprayer for applying Roundup for tall weeds in grass seeds after potatoes.
The business venture with MSR brought a second useful product: the Crowncrusher, which Henning helped to develop. He has 18 hectares of potato trials, ranging from trials of genomic techniques for disease resistance and nutritional value, starch work for KMC to Tystofte (variety testing). The trial plots also allowed Henning to study the comparative benefits of electrical destruction, burning and chemical products, before looking at mechanical solutions, which found most favour with him.
In a single pass, rotating blades cut and crush the haulm, placing it on top of the ridge or spreading across the ground as required. Models up to six rows are available, with output up to 4ha/hr.
“It cuts the top right at the soil surface, and the trick is to cover the green part with soil again, so the plant doesn’t continue to grow afterwards,” he explains.
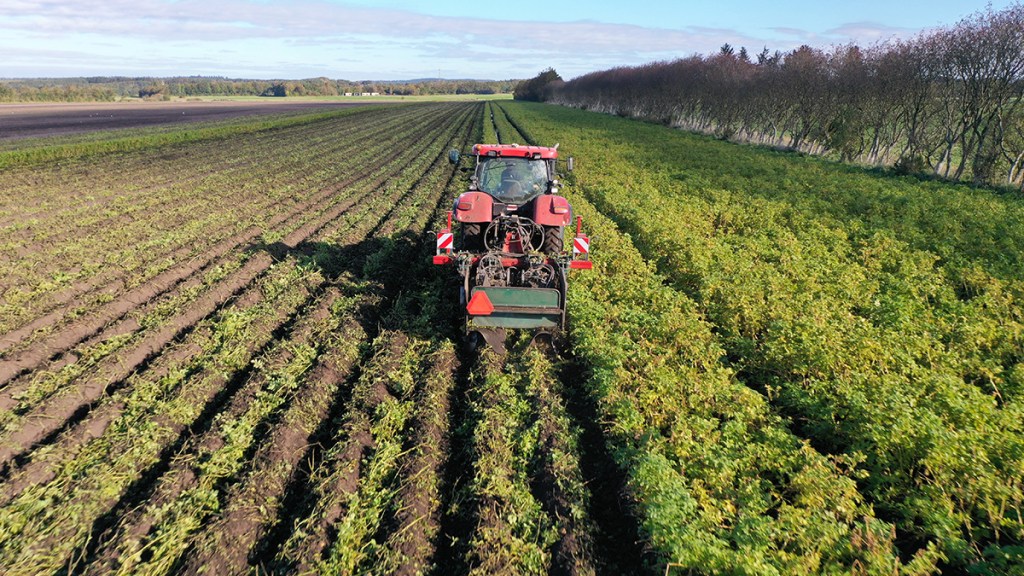
The Crown Crusher can also be used in conjunction with the Opti Weeder where the field has become weedy ahead of harvest.
Out of the ground
Potatoes are delivered 20 weeks of the year to the factory for starch, and the harvest extends from September to the first week of November, ahead of the worst of the weather.
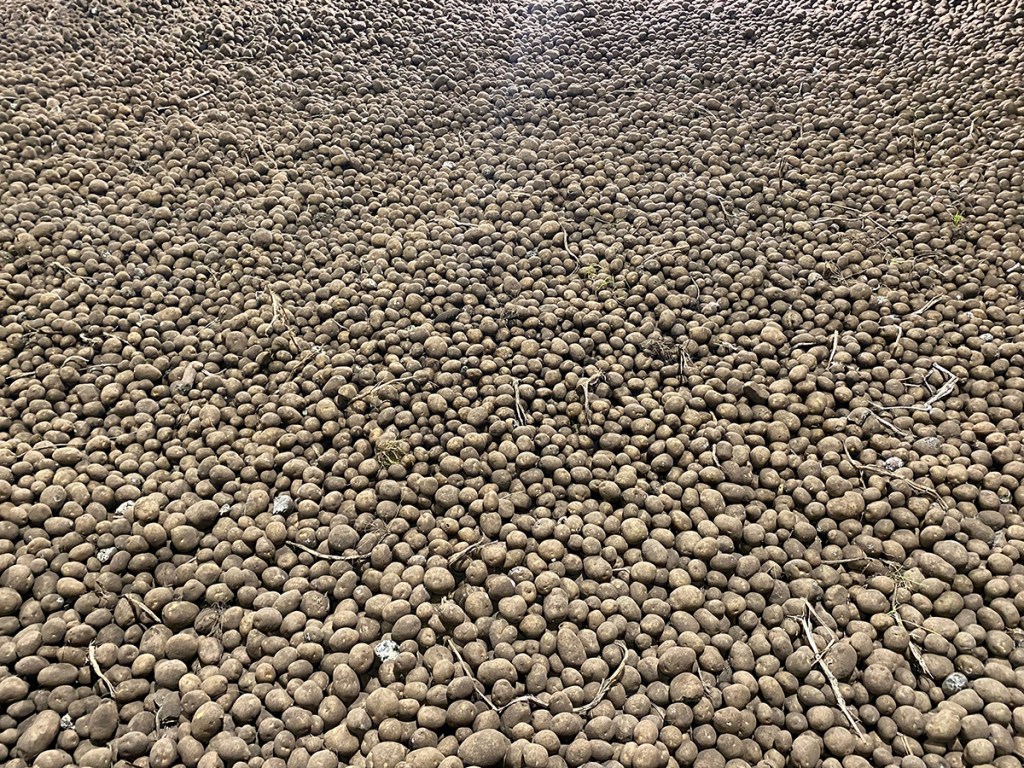
The business uses three trailed bunker harvesters, including a 2023 AVR Spirit 9200 with dual wheels and a hydraulically driven axle for improved performance in wet conditions. Often the three are used together to lift potatoes before it becomes too wet to go in the field.
A number of different approaches have been trialled for ensuring a clean crop to the factory, he explains.
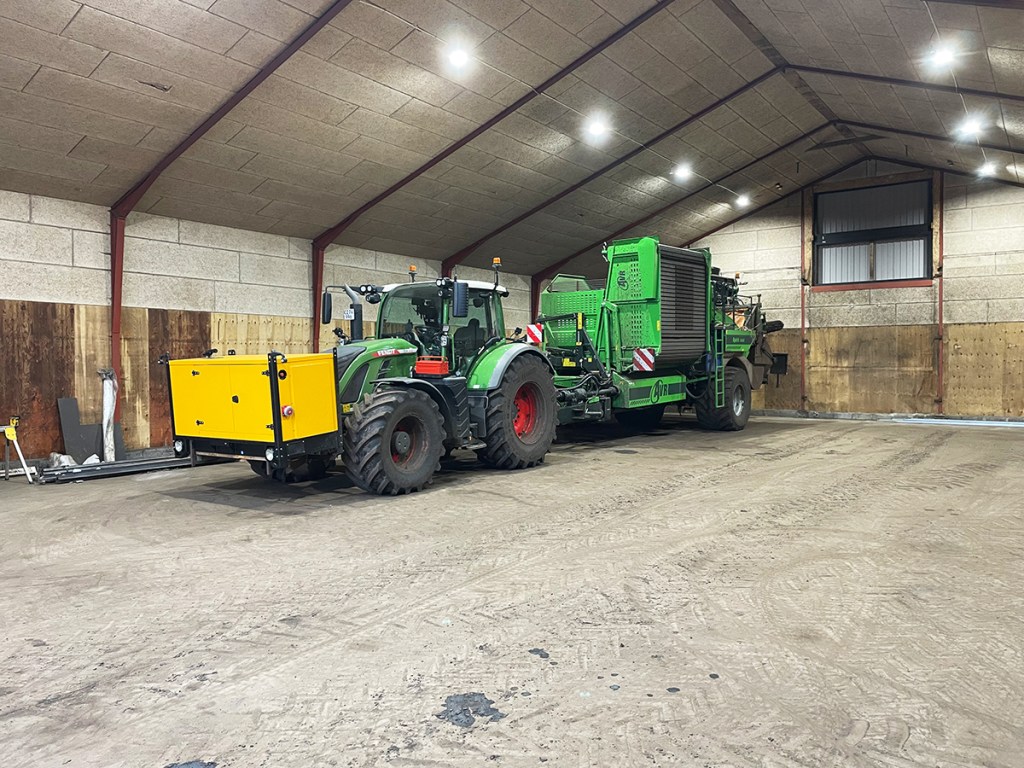
“Before 2010 we destoned the ground, a practice that we returned to in 2024. In 2011 we began to wash the potatoes if there were stones, but in 2017 we built an air destoner, and last year added a second hand Spudnik air destoner.”
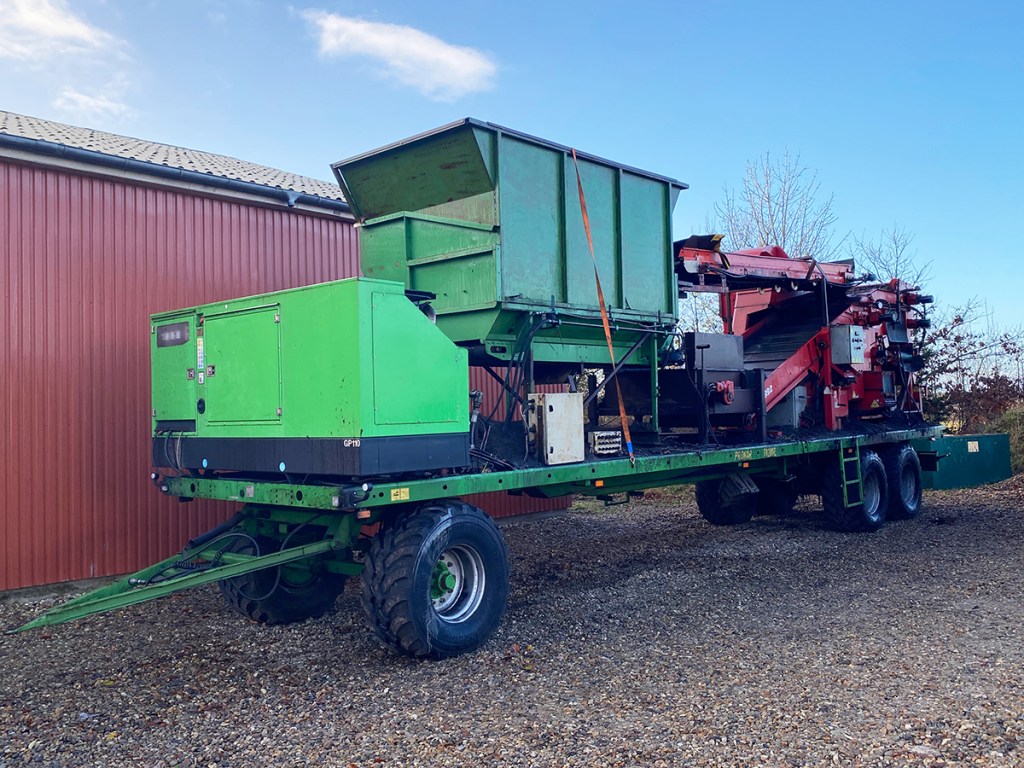
Other developments have included a rewinder to gather up plastic used for covering ridges, fibertex and nets from the field, with the coverings rolled up and re-used. Initially it was just a time-saver, but now also demonstrates good stewardship.
“Today, new plastic only goes on the potatoes that need to be stored the longest,” he says.
It might seem a lot of work for an already busy farmer and businessman to get involved in developing equipment, but Henning says: “Potatoes are still a relatively niche market so many manufacturers are not interested in new technology, so we have to make our own.”
And where he has formed partnerships with established innovators in the industry, he continues to push the boundaries. “The planter challenges the isobus system on my tractor because it is required to control the fertilser placement, in-row spacing for the seed potatoes, monitoring seed placement over 12 rows and steering the axles. So I asked for more processing capacity, only to be told that I already have more than other customers. But I still want more! It is improving now and worked well last season.”
Jane Carley
For more up-to-date farming news click here and subscribe now to profi and save.