The telehandler is an unmissable tool for UK farmers and contractors, and the Loadall is one of the most commonly seen handlers across the country. We’ve been to Rocester to see how they are made.
LOADALL PLANT FACTS:
- When the plant produces up to 130 machines per day it consumes the equivalent of 5.5 Eiffel Towers of steel a year.
- The manual weld bays alone consume up to 200t or 14,000 miles of weld wire a year.
- It takes just four minutes to pain each product. Loadall production consumes over 165,000l (36,300 gallons) of paint a year.
- From sheet steel to final sign out takes five days (three days through manufacturing and two on assembly).
- Loadalls not only made for agricultural and construction markets, but are also sold to Formula 1, mining, police, military and even the film industry.
- The 532-70 and 540-70 are the most popular Loadalls for the agricultural market.
- Precise numbers are off limits but we reckon the plant currently makes 25,000-30,000 machines a year. More than 350,000 units have been made since 1977.
- The first telehandler, the 2wd 520 (2.25t, 6.40m), was launched in 1977. The heavier lifting 525 was added in 1980. Maximum lift capacity of the current range is from 1.4-6.0t with engine power up to 129hp.
Globally, JCB reckons to be number one for telehandlers, accounting for more than one in every three units sold. Peak demand for ag machines is highest at harvest, but the popularity of the British designed and built Loadall is not limited to the farming community, construction models account for up to 70% of production.
JCB also has a Loadall plant near Delhi, India, but all machines for the UK, European and North American markets are made at the firm’s world HQ at Rocester in Staffordshire. This is also the home for backhoes and site dumpers, but the focus of our visit was squarely on the Loadall.
Big bits in-house
Valve blocks and electrical harnesses are outsourced. So too are radiators, cooling packs, fuel tanks, mudguards, etc, but all-important key components are manufactured at JCB plants in England. The axles and transmissions are produced at a facility in Wrexham, the cabs and attachments in Uttoxeter, and the engines are from JCB Power Systems. All hydraulic cylinders are made at Rocester, as are two other crucial telehandler components – the main frame (chassis) and telescopic boom. Both are fabricated inside a 20,000m bay next to the assembly area.
I joined Shaun Connolly, head of manufacturing and engineering for Loadalls and backhoes, for a tour of the beating heart of the production process.
The making of a main frame and boom begins with the four lasers that cut 3.0-20mm flat sheet steel into jigsaw pieces. Not far away, four plasma cutters tackled thicker steel (25-45mm) for the frames. Next, we saw a 650t press bend 6.0-15mm flat steel into the required box shape sections for the first part of a telescopic boom.
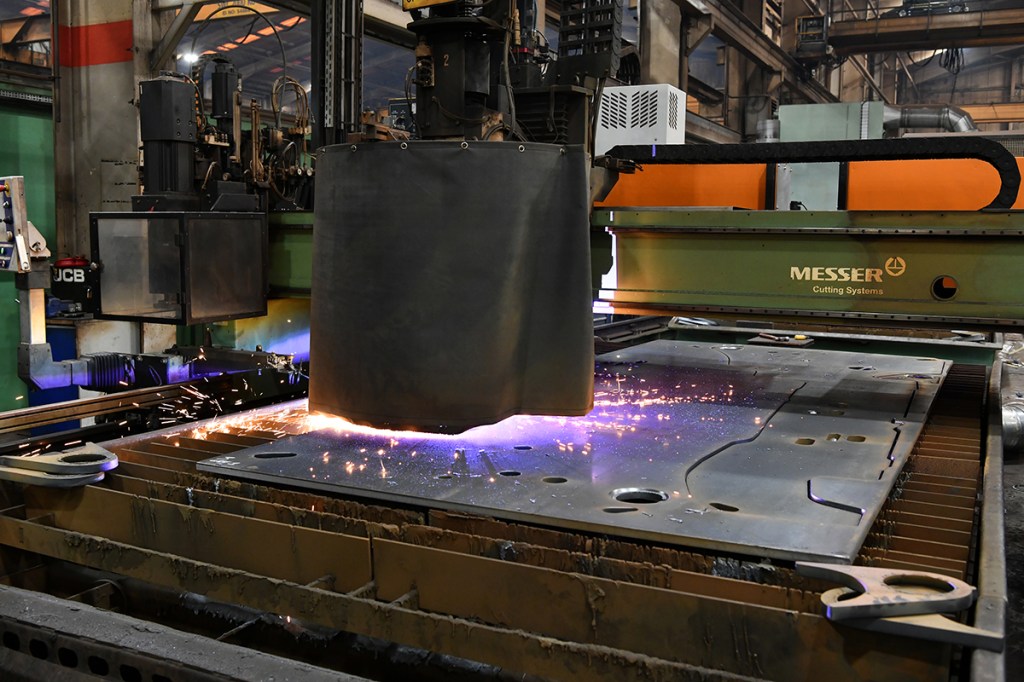
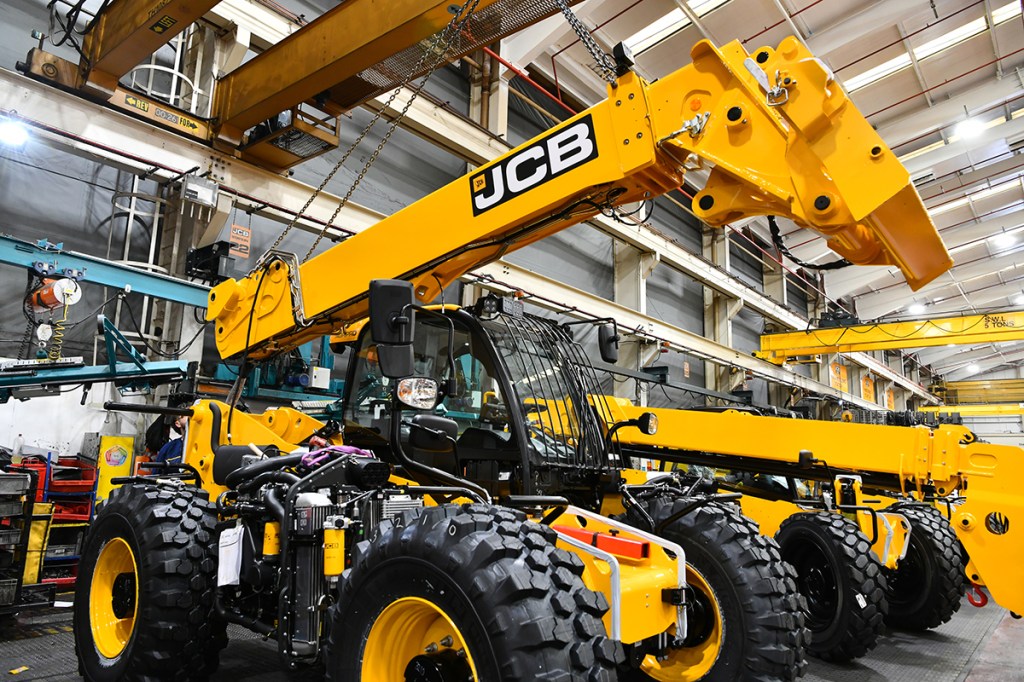
Holes are then milled into the side plates, after which the different sections are welded together. This is tasked to nine welding robots (booms welded by another six). Robots can only tackle around 80% of welds. Skilled operators tackle harder to access welds and 17 staff are needed to finish a main frame, and another 18 for the boom. Pivot bosses on the booms and mainframe are then bored in the machining area. There are six milling machines (two for the boom and four for the frame).
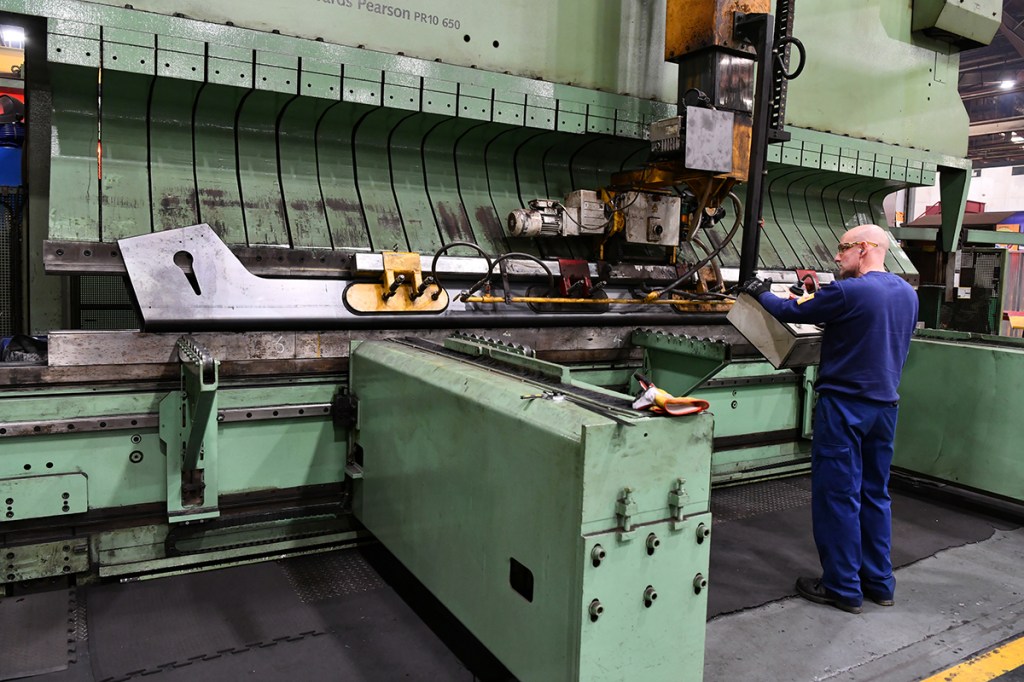
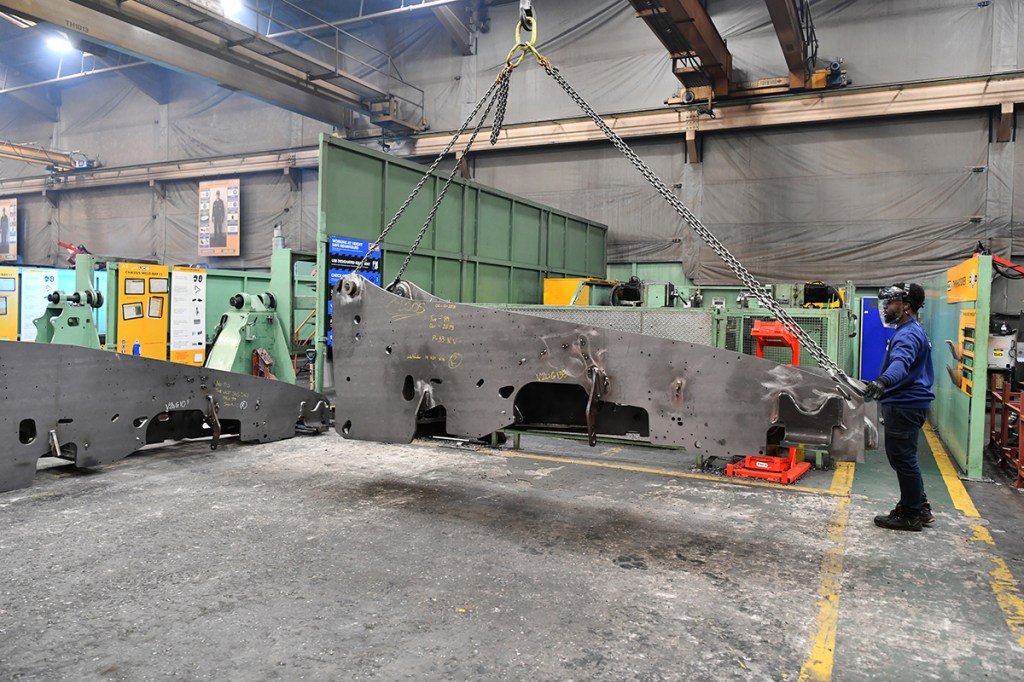
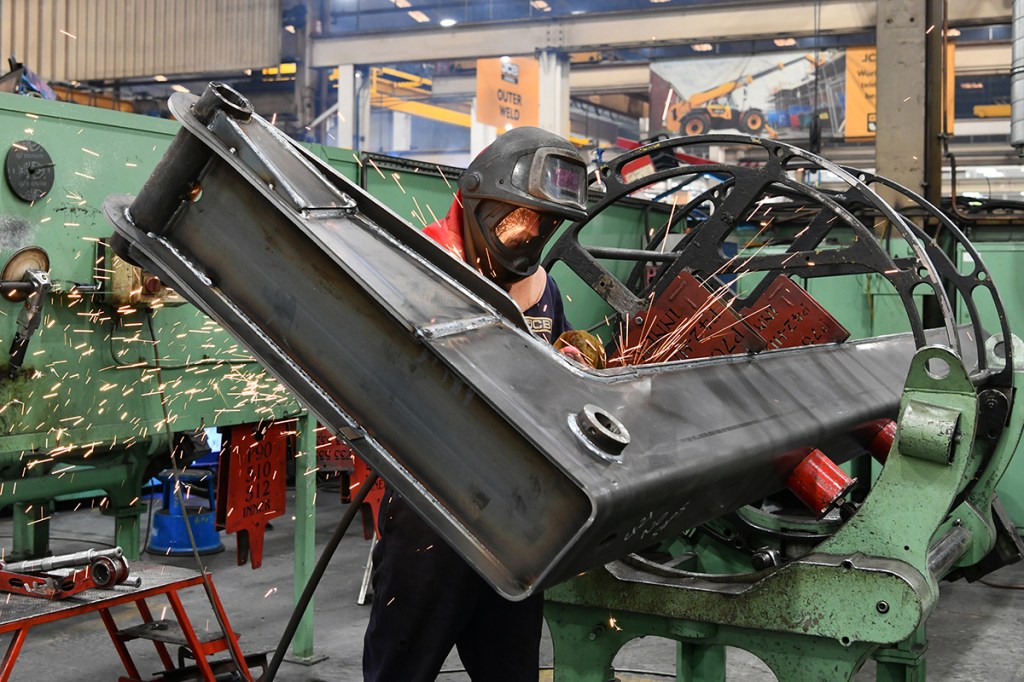
More than a third of the 4,500 employees at Rocester work for the Loadall division. Over 500 of these are in the manufacturing building, where cutting, bending, welding and shot blasting machines work day and night 24/7, even at weekends.
Up to 130 machines a day
At the end of the building, booms and chassis are shot blasted and primed before entering the paint shop, another area that works around-the-clock. Painted components emerge inside the adjacent assembly building where the axles and wheels are secured to the chassis, which is then hoisted onto the 120m-long main assembly line.
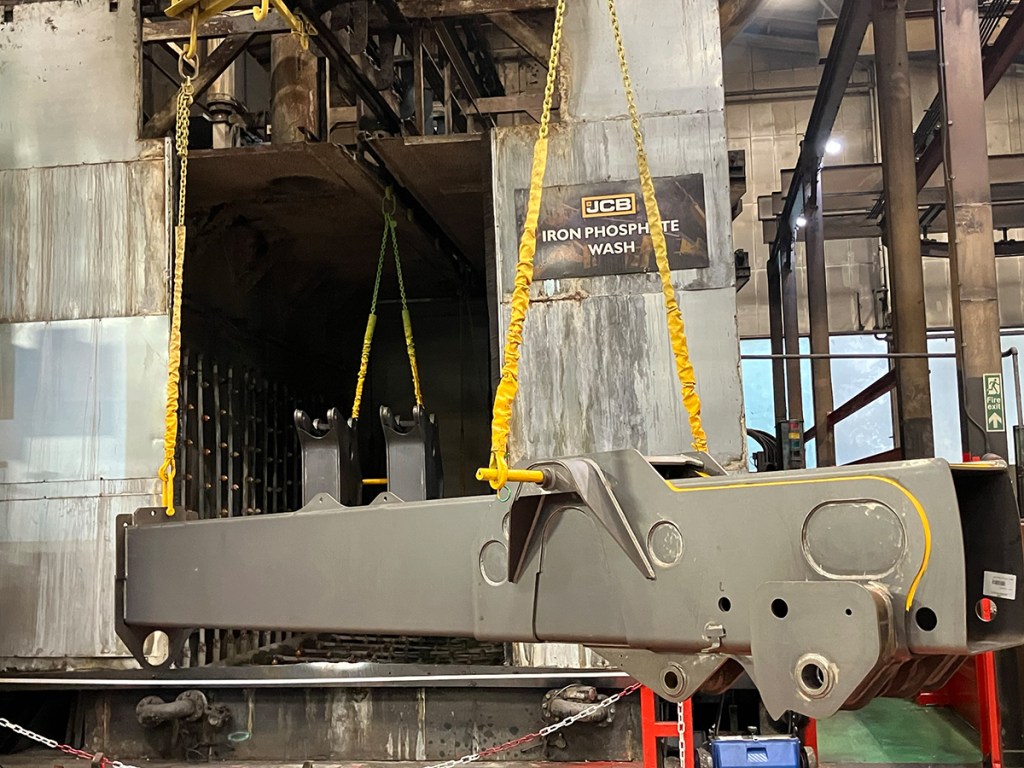
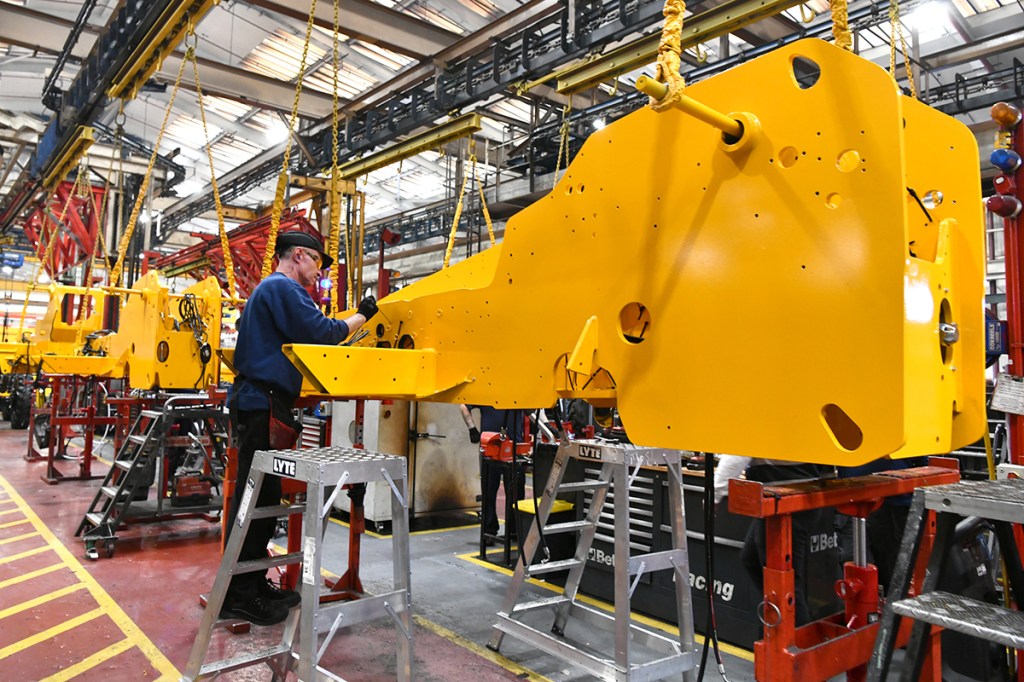
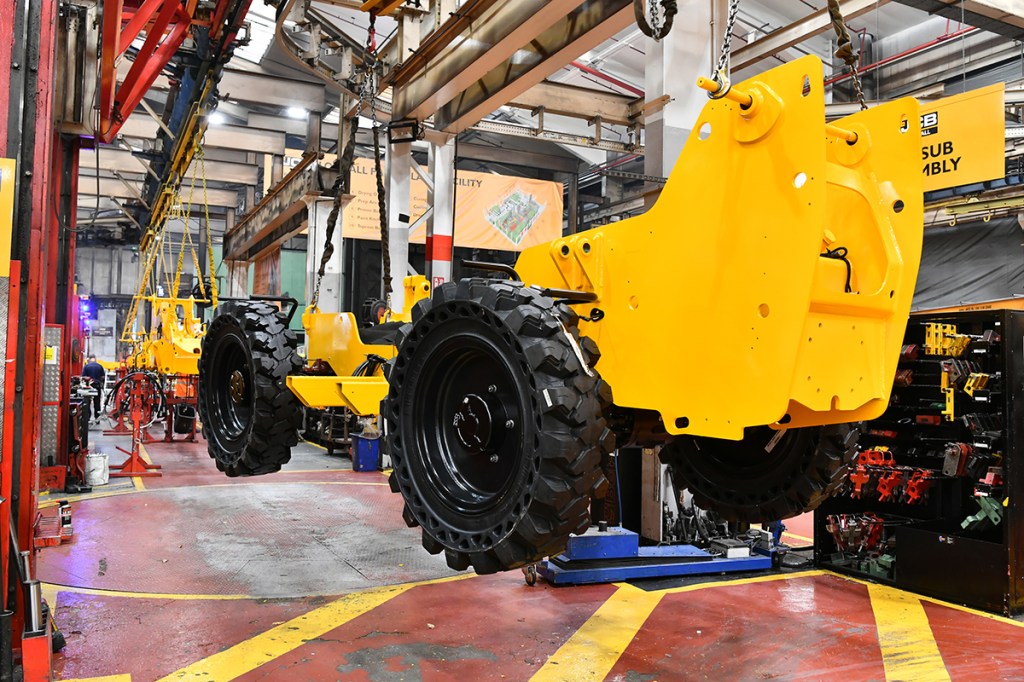
The assembly line, or track, runs on weekdays from 6.30am to 4.30pm, followed by a night shift from 6.00pm to 4.30am. It shuts down at the weekend, and for six weeks a year (one at Christmas, one in May, three in the summer, and one in September). There are 40 assembly stations. Several staff work on some, but regardless of the numbers, all stations have precisely eight minutes to complete a task.
There are major differences between Loadalls for ag and construction markets. Construction machines are required to lift heavier weights to much loftier heights, while ag machines are physically smaller and need increased manoeuvrability for working in confined spaces.
Despite these conflicting contrasts, both types are built on the same assembly line. With 10 base agricultural models alone, there are 1,000 different ag and construction machine configurations, ranging from engines to hydraulics and wheel rims to work lights.
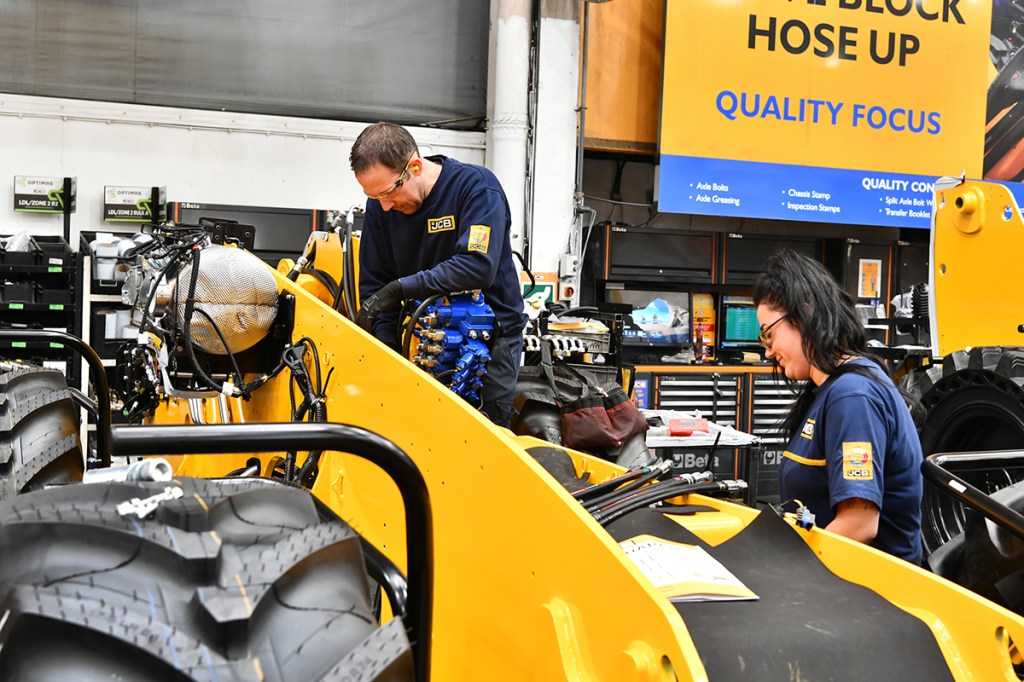
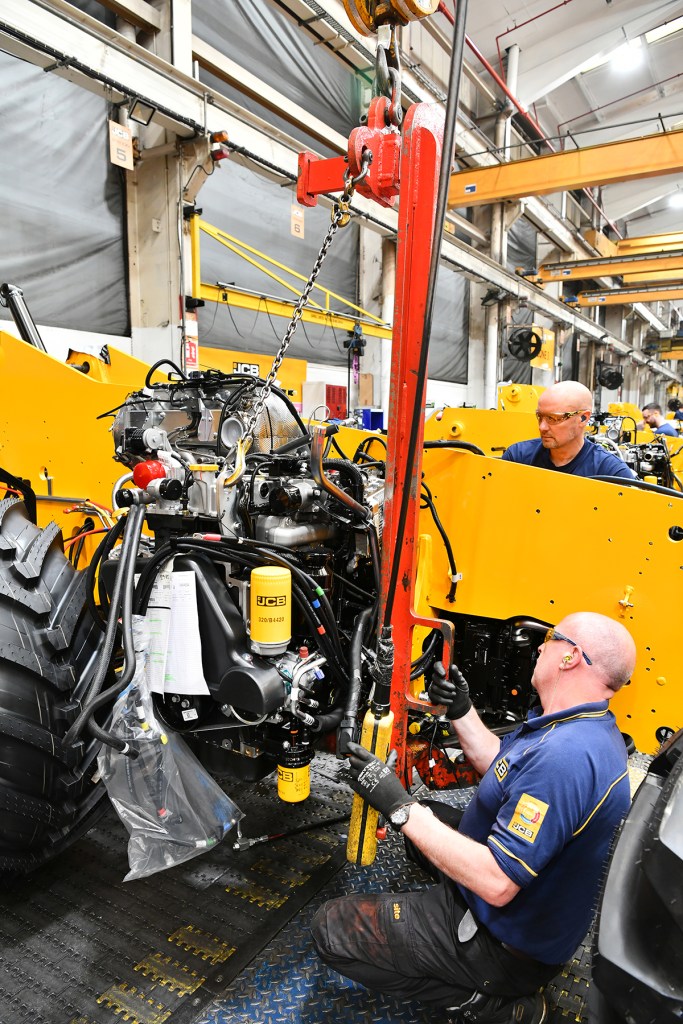
Pre-assembling engines and transmissions ensures that the main line works as efficiently as possible and adheres to the eight-minute deadline. With 100 staff on the line per shift, all 40 stations are important, but the three main ones involve fitting the engine, cab and boom.
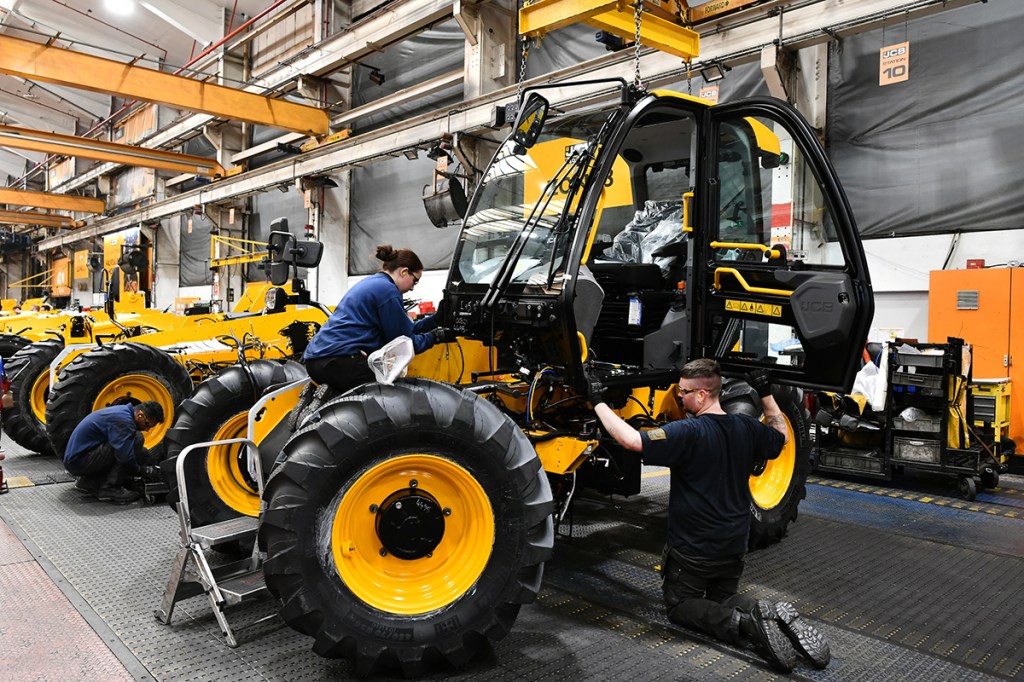
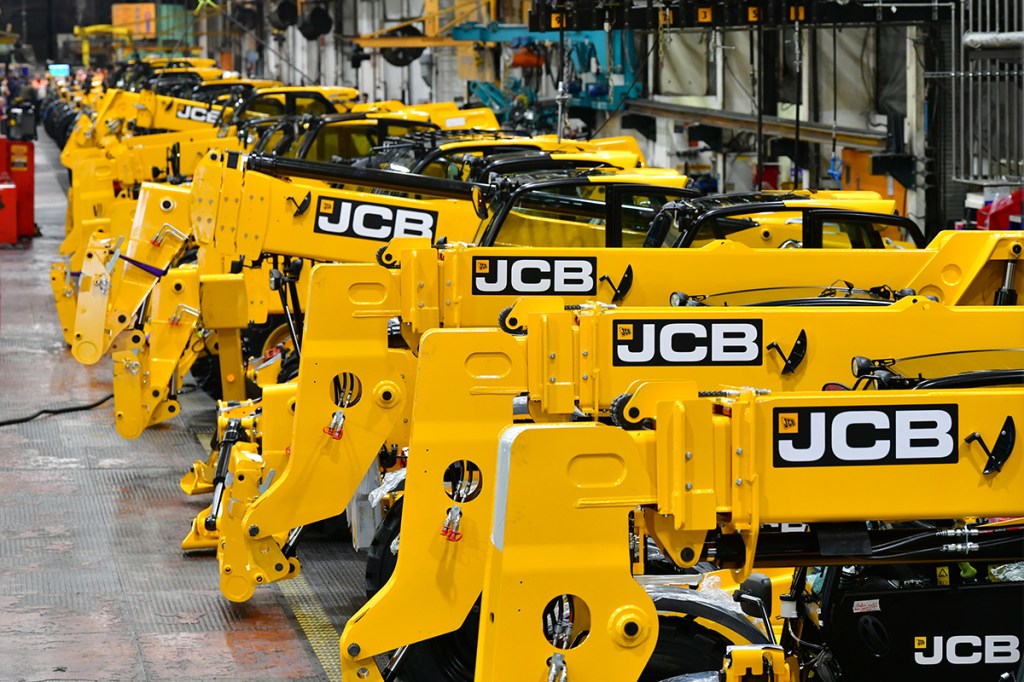
The pre-assembled engine/transmission joins a machine at station five, followed by everything that needs to go on before the cab is lowered onto the chassis at station 13, and while eight minutes does not sound long to fit the cab, it is secured by just four bolts.
The boom is craned onto its host chassis at station 20, although it is not possible to fit it and connect up all the hoses in eight minutes. The process takes 16 minutes so two teams ensure that one machine is ready every eight minutes.
Ready to roll
The entire assembly process takes five hours, after which Loadalls are driven onto a rolling road test bay and on a dyno to check the powertrain and brakes. This also takes 16 minutes, so two test bays are needed to match the pace of the assembly line.
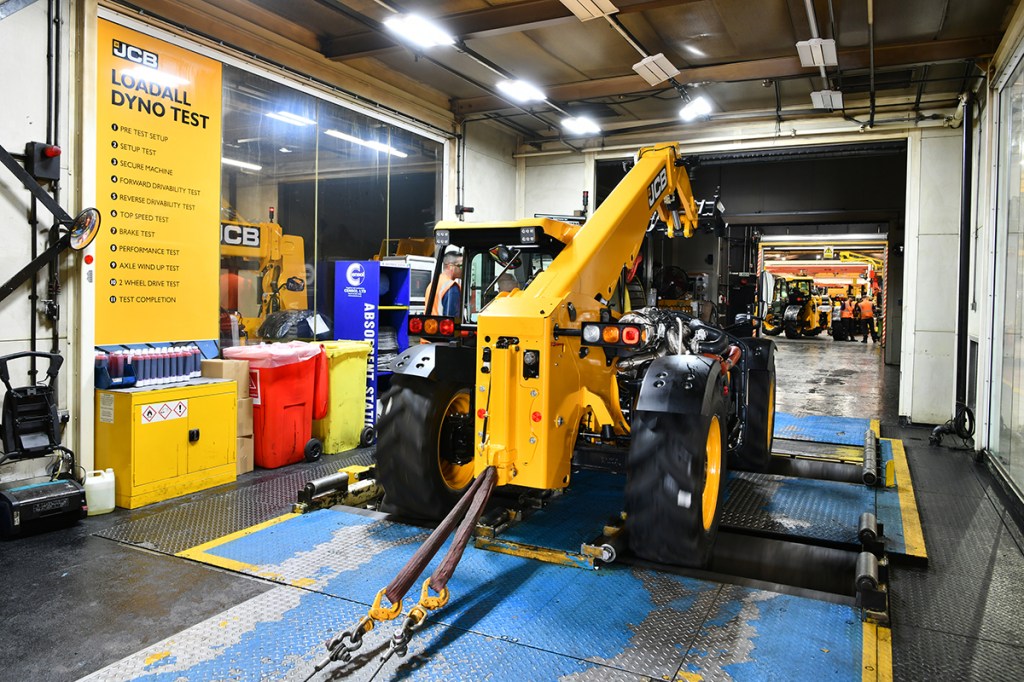
Machines are then driven to one of two final lanes where bonnets are fitted, pins are greased and lights are tested, before a machine is ready for the outdoor test phase. Outside, the first job is to heat up the oil, after which every handler must hold a weight with the boom fully raised and extended for 10 minutes. There is also a drop test where the weight is lowered slowly to stretch each machine to the limit.
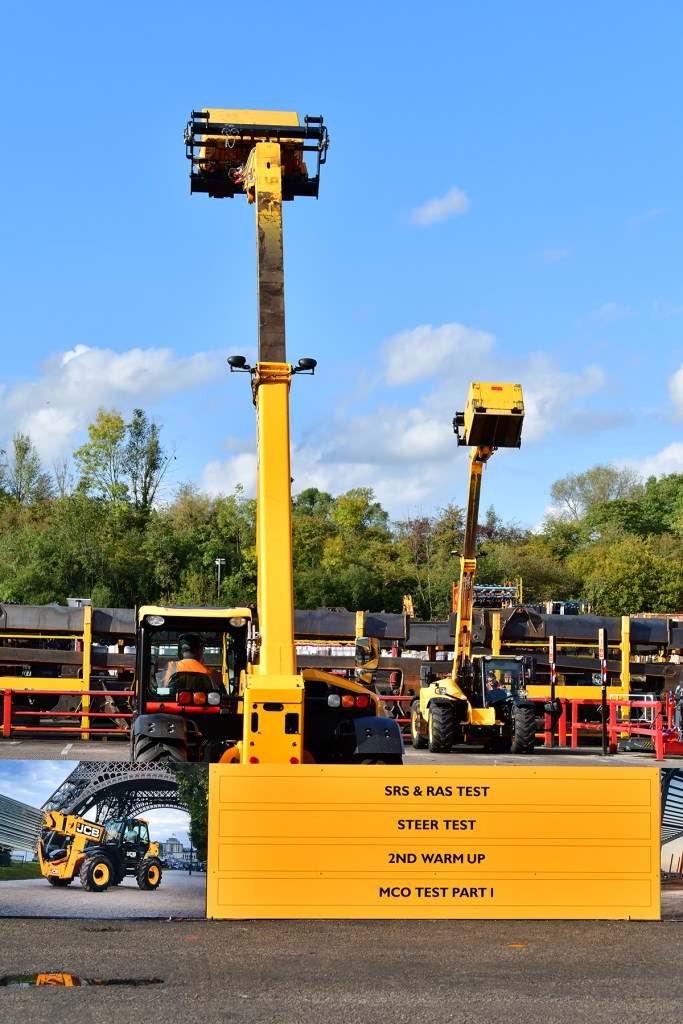
All handlers must then complete another 11 outdoor tests. These include a rumble track, where each handler picks up a weight to test that the SMS (Smooth Ride System) works correctly. Plus, there are steering as well as two and four wheel drive tests. Each operator remains with one machine for the full duration of the tests, which takes up to two hours.
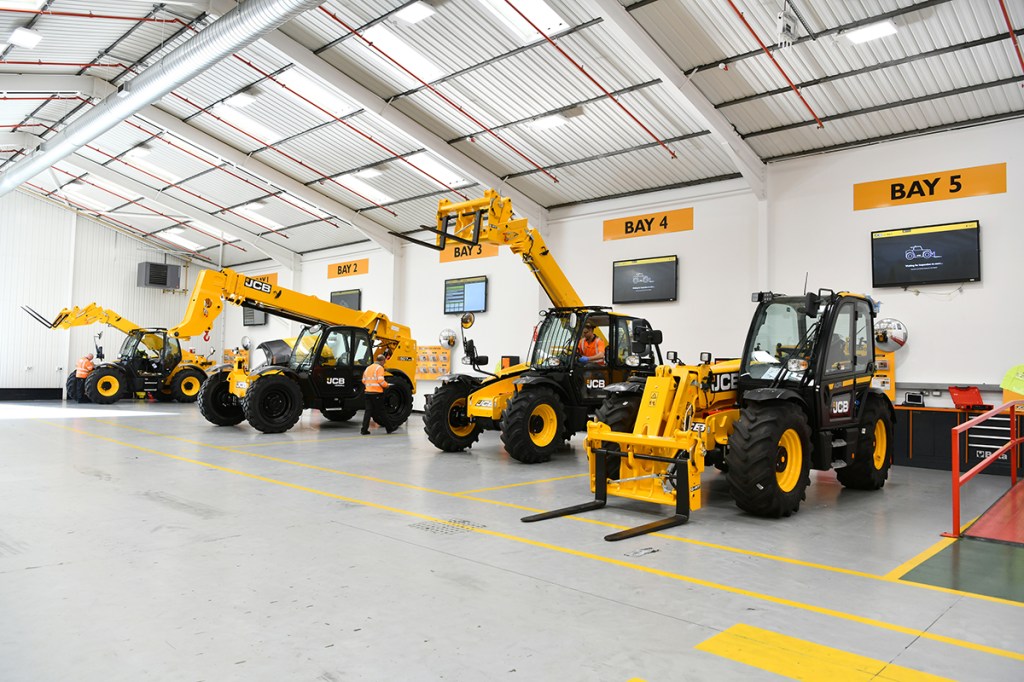
When finished, each Loadall is driven to the PDI building. A series of photographs are taken of the serial plate as each machine leaves the building. Pictures are also snapped from different angles to confirm that everything is on it and that there are no scratches to the paintwork. From here, it is off to the dispatch area, and ready for delivery to a dealer.
Steven Vale
For more up-to-date farming news click here and subscribe now to profi and save.