Having shown a prototype version of its Aura autonomous diet feeder nearly four years ago, Kuhn has announced that it is now due to enter production. Keep reading to find out about the experiences of the test farms and what owners can expect.
KEEPING IT BRIEF
- Aura production is starting now at Kuhn’s La Copechagniere plant in western France.
- Unlike other feeding robots, the Aura can load itself directly from the silage clamp.
- Farm layout needs to be surveyed to assess suitability.
- Kuhn is working on a version with electric drive and possibly a fleet solution for larger farms.
- Labour saving is the biggest benefit for the owners we spoke with.
With production of the autonomous Aura diet feeder now underway, Kuhn is ushering in a new era. Not only does Aura mix and feed autonomously, but it can also drive around the yard to the silage clamps where it can load forage directly from the pit face. This means you no longer need to load feed bunkers or store blocks of silage in a feed kitchen.
This not only saves cost on initial additional construction, but in the long term it also saves on valuable time. Speaking to a couple of French farmers who have been operating pre-series versions, they also reported several other advantages. They also noted, however, that the Kuhn Aura will not be suitable for every farm … but more on that later.
Years of development
Kuhn first presented the Aura at the French livestock exhibition, Space, back in 2021. We caught up with one of the prototype units in our 03/2023 issue to learn a little more about the Aura project.
Meanwhile, Kuhn has built more machines to expand testing under close supervision on carefully chosen farms within France, Kuhn’s homeland. After 40,000 hours of testing, the company believes the time is right to start production.
The target group
According to Kuhn, the 3.0m3 mixer wagon is best suited to finishing units and dairy farms with 90 to 280 milking cows plus offspring. That is a big variation, but the reason for this range depends on the number of feed groups, how often they are fed and the distance the robot has to travel. In broad terms, the Aura is suitable for farms with two to four milking robots.
For larger farm units, Kuhn is working on a connected fleet solution, where several of the robots will work together. But that is all the manufacturer wants to reveal about its future developments.
Safety first
The empty 5.9t Aura drives autonomously across the farmyard, automatically opening doors and gates and even flashing its lights before turning. It follows a default route of travel with an accuracy of +/-2cm, courtesy of a sophisticated navigation and safety system.
Before committing, the first step is to have a surveyor map out the farmyard and buildings. This map shows all of the routes, the clamps, stores for concentrates, the cow barns and every single trough/feed fence.
Navigating and positioning requires a Wi-Fi connection for the machine-based antennas to connect to GNSS satellites. For seamless navigation in the open you’ll need a number of Wi-Fi antennas spread throughout the yard to ensure a stable, reliable reception.
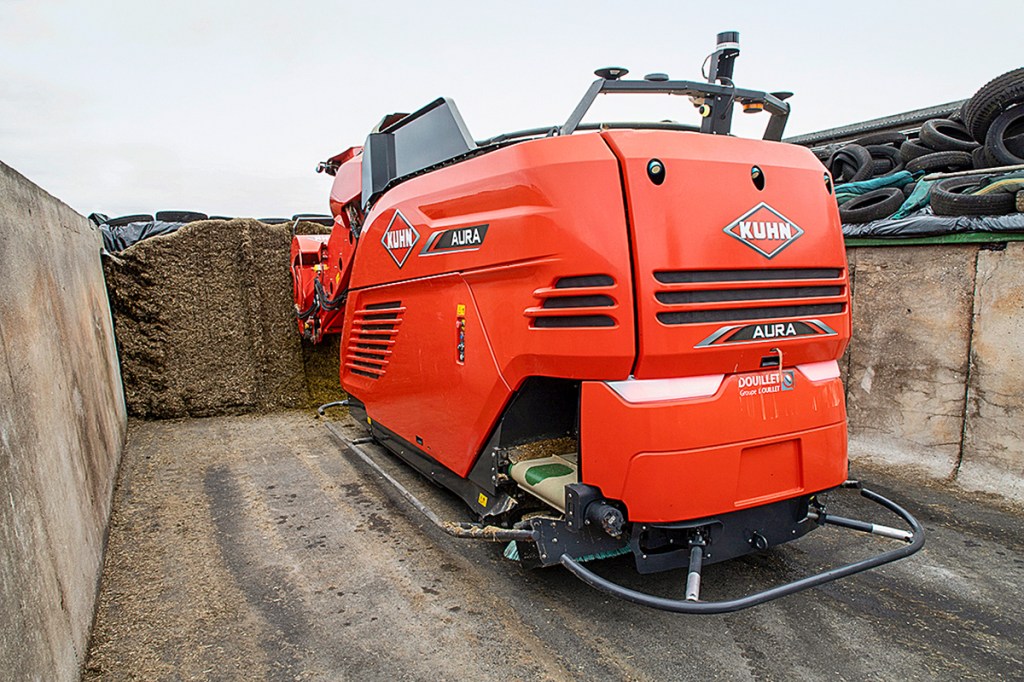
Should the machine lose the GPS signal when entering the barn, robot position is determined by measuring the distance (odometry). At the same time, a LIDAR sensor (Light Detection and Ranging) verifies the current position of the machine. LIDAR uses an eye-safe laser to measure the surroundings at breathtaking speed and then creates a 3D map. Constantly comparing the old map with the new one, Aura can recognise its exact position and any obstacles in the buildings.
Kuhn combines LIDAR with several other safety systems, which consist of ultrasonic sensors front and rear to detect obstacles at a distance of up to 10m. Lasers on the silage milling arm check whether anyone is on top of the clamp or between the pit face and the machine. And another laser positioned lower down on the machine, close to the ground, scans the area ahead at a 240° angle. Any objects that are taller than 30cm and longer than 60cm are identified as obstacles.
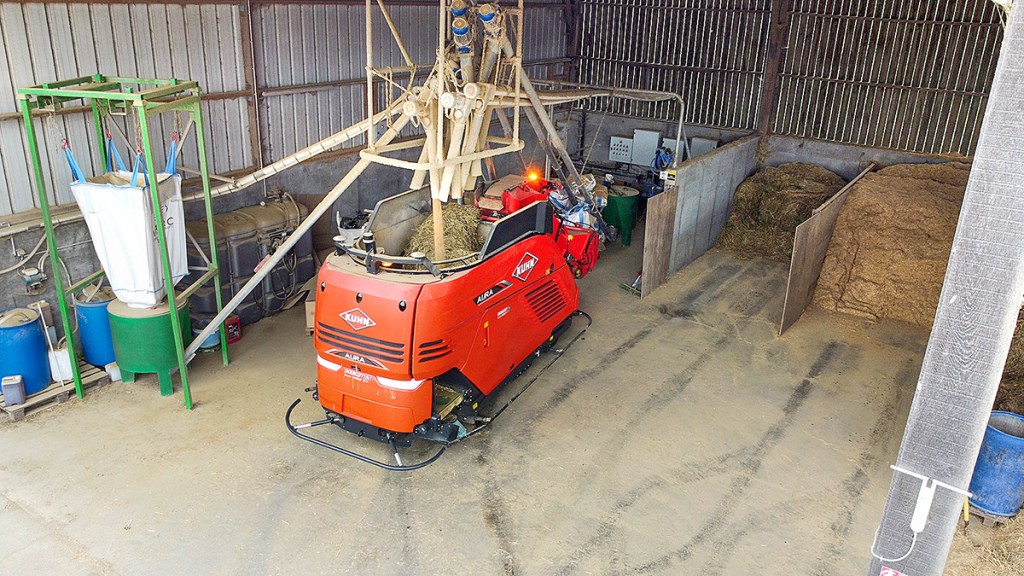
Depending on the obstacle identified and the situation, the safety system duly responds in various ways. If, for example, after a certain time the dog still refuses to get out of the way, or if the safety rail that runs around the robot 15cm above the ground is triggered, then the machine stops completely. In this case, the farmer gets an alert on their smartphone and has to walk over to the machine and start the engine manually.
The good news: we feared the cows could trigger the emergency stop safety rail as the machine drove alongside the feed fence, but this doesn’t seem to be an issue.
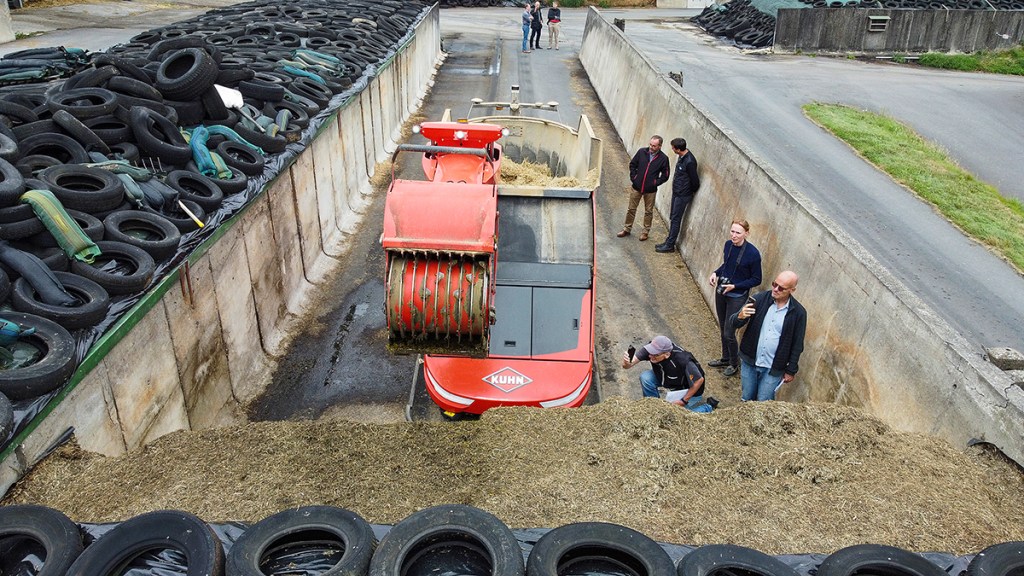
Clamps only
Speaking of safety, Aura does require a few things from the farm. For example, for the milling head to start, the machine must drive 2.0m into the clamp. The sides of the silage pit must be at least 1.80m high – this is to prevent people reaching over the wall and getting hurt by the mill.
After Aura arrives at the clamp face, the mill moves into its previously saved working position. Then it starts loading the silage, cutting pass after pass, leaving a clean pit face so no forage is left to spoil. The robot also memorises the height of the pit so the boom doesn’t always extend to its max working height of 4.0m. For smaller silage clamps for example, it only raises the arm to 1.50m, which saves time, fuel and machine wear.
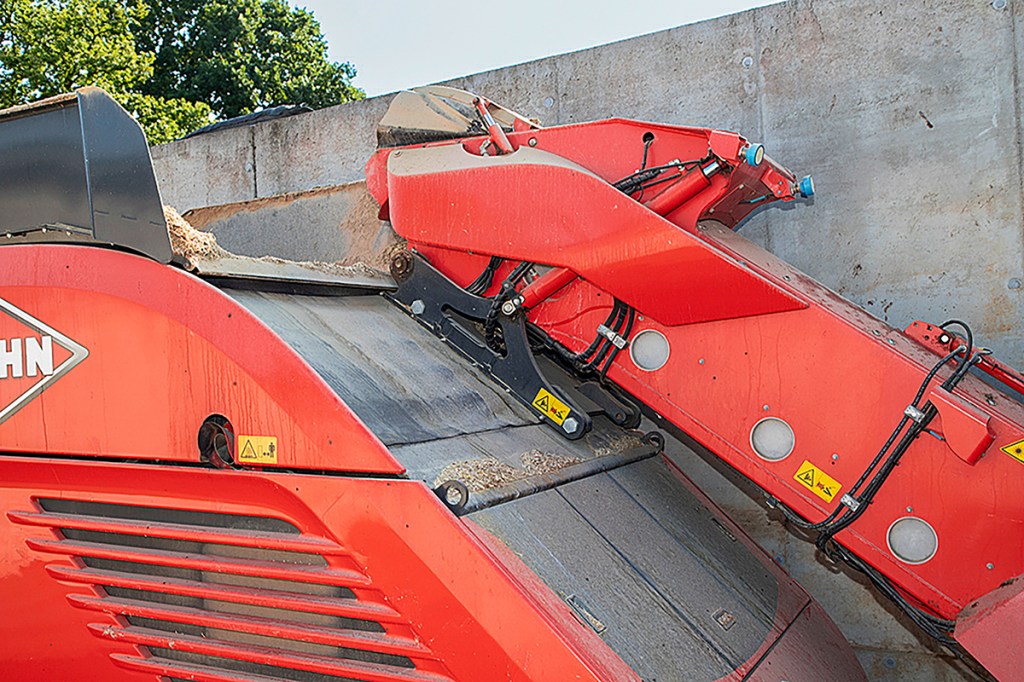
The robot doesn’t have any sensors to detect changes on the pit face. This is not an issue if the Aura is doing all the feeding, but if you are removing silage for feeding stock away from the main yard or a biogas plant, then ideally this silage needs to be in a second clamp; otherwise the robot could become muddled.
We were impressed with the cleanliness of the pit. Most of the fallen feed is gathered up; the machine reverses after each milling pass and then picks up the loose silage as it moves forward again.
To avoid hitting the wall, Aura approaches the pit face nearest the edge sideways by utilising its crab steer mode. As the boom is able to move hydraulically 75cm over to the side, the machine doesn’t need to reposition for each and every cut. Downside is that a 20cm wide strip is not cut along by the wall, which needs to be removed separately. If you use plastic covers on the wall, this too needs to be trimmed regularly; otherwise the sensors may mistake it as an obstacle and stop.
Fuel-powered but a battery is coming soon
Providing the power is a three-cylinder diesel Kohler Stage V compliant engine producing 42kW/57hp. Average fuel consumption from all of the test farms was exactly 3.5l/hr, says Kuhn. The tank holds 200 litres.
Kuhn is also working on an electric version that could be charged by utilising on-farm generated solar power. This was all Kuhn was willing to disclose on this new power source. It also remains to be seen whether the firm will retain the hydraulic drive. The hydraulic system currently powers the mill, the two mixing augers, the 40cm wide feed belt and all four wheels including hydraulic steering. Maximum forward travel speed is 7.2km/hr.
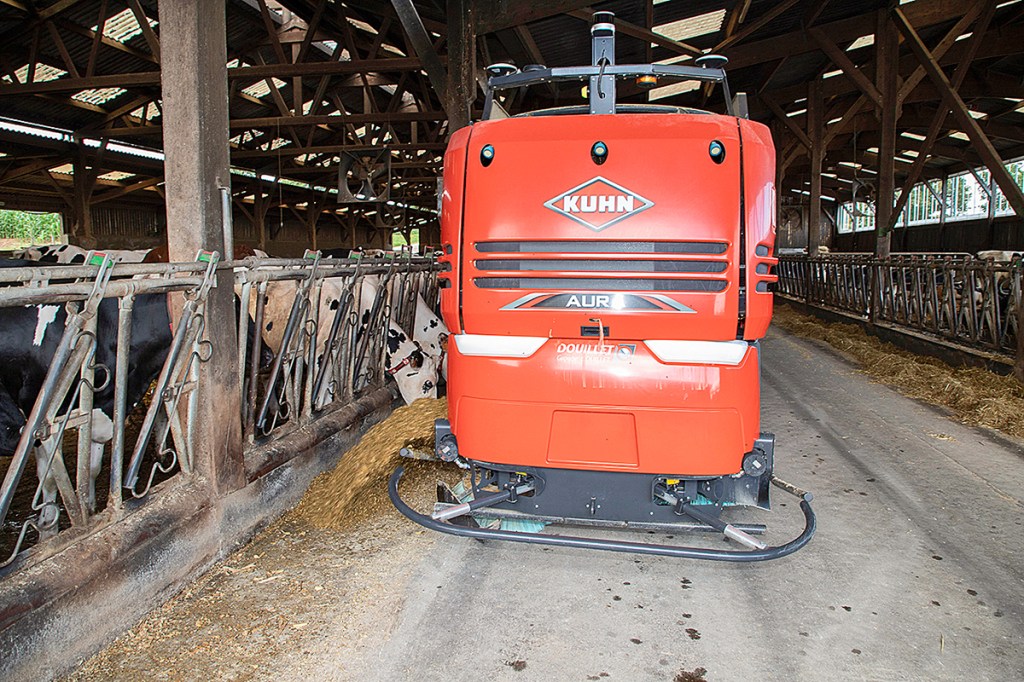
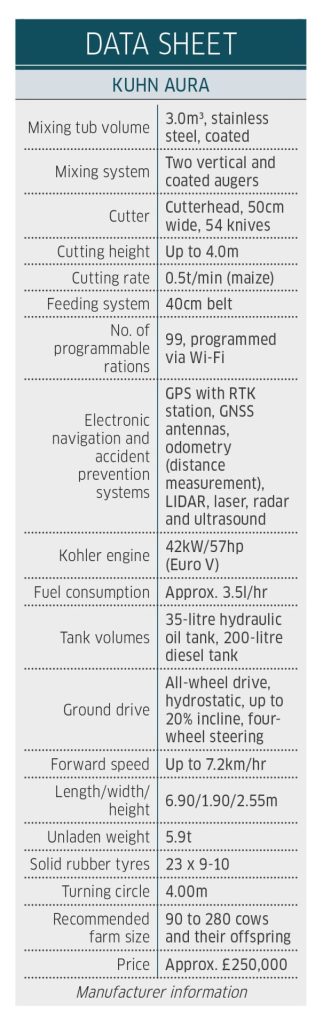
What users say
We were able to discuss the feeding system’s on-farm performance with the test farmers in Normandy.
First up are Nicolas and Anthony Maillard from Saint-Bômer-les-Forges, who took over the family business in 2007, farming 250ha, 110 milkers, 25 dry cows, 115 heifers and 250 bulls as well as operating a 250kW digester. The cows produce 1.1 million litres of milk per year through two robots.
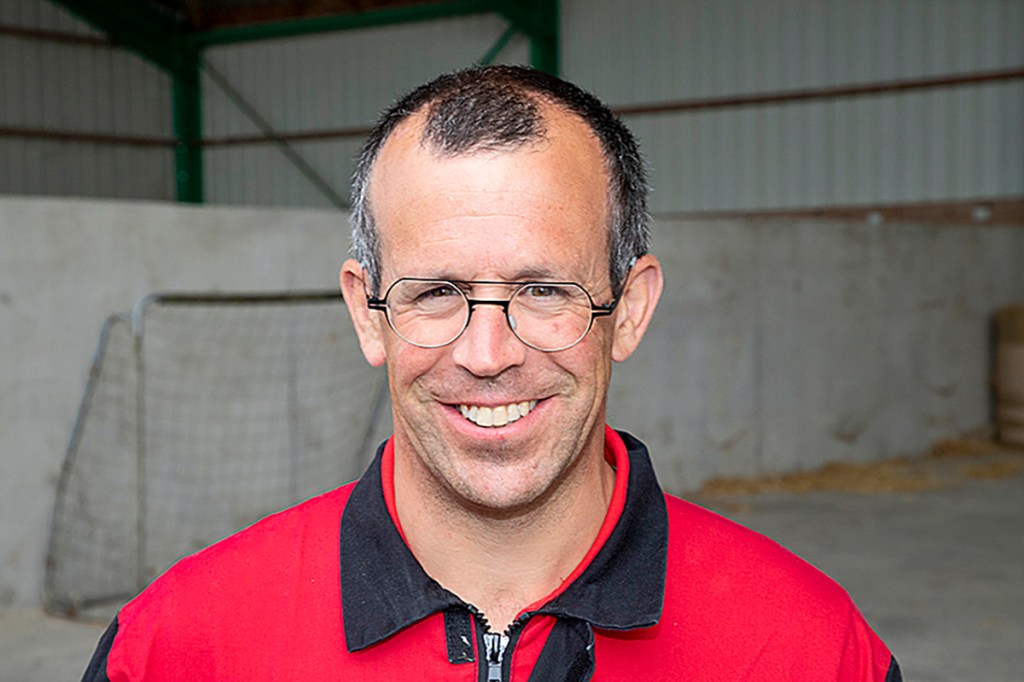
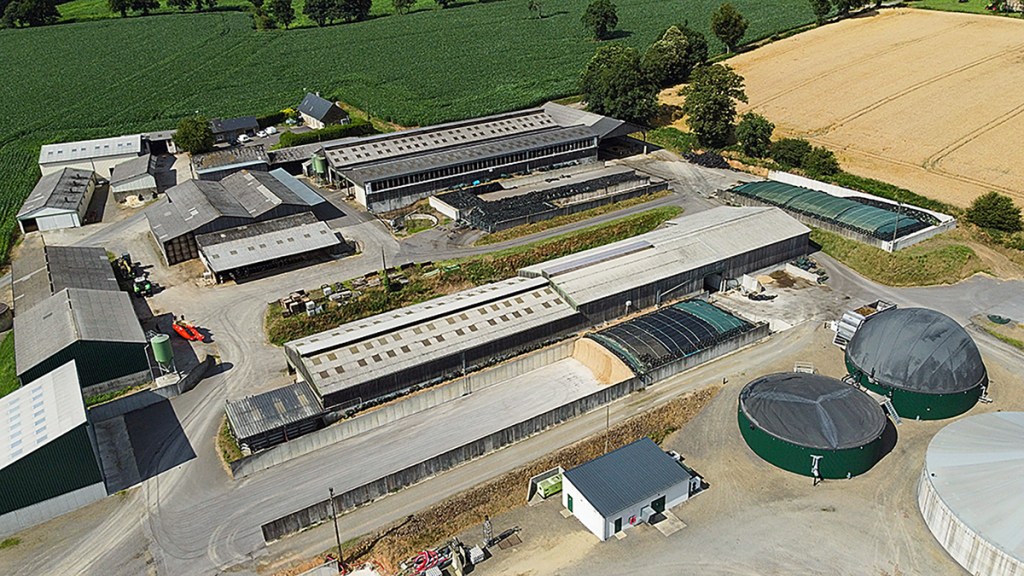
Since Kuhn’s Aura autonomous feeder was commissioned in 2022, the daily output per cow has increased by nearly 3kg to 31.2 litres. Average visits to the milking robots have also increased by 0.2. Meanwhile the dead weight of the bulls has increased by 15kg.
However, the main reason for purchasing the autonomous machine was to reduce labour. Previously feeding the animals with a Euromix 3 took almost four hours per day. Now it takes an average of 50 minutes, so Aura is saving the Maillards around 2.5 hours every day. The remaining work includes pulling back the cover on the clamp and removing the strip of silage alongside the wall.
So far, their Aura has clocked 13,000 hours without any problems worth mentioning and consumed an average of 3.5l/hr of diesel. Changing the engine oil every 500 hours is no problem, whereas the 1,000-hour service requires an appointment with the dealer.
When asked what areas need improving on the Aura. Anthony has just the one wish: “A NIR sensor inside the tub that measures moisture, crude protein and crude fibre would be great.”
On work peaks
The second business we visited belongs to siblings Etienne and Adéle Salles from Saint-Hilaire-de-Briouze. With their parents and three employees, they farm 240 hectares of land, 130 cows, 100 heifers, 25 dry cows, 180 Charolais beef bulls and also operate a 250kW biogas plant. Milking is done by two robots that were installed back in 2007. Annual milk production stands at 1.4 million litres.
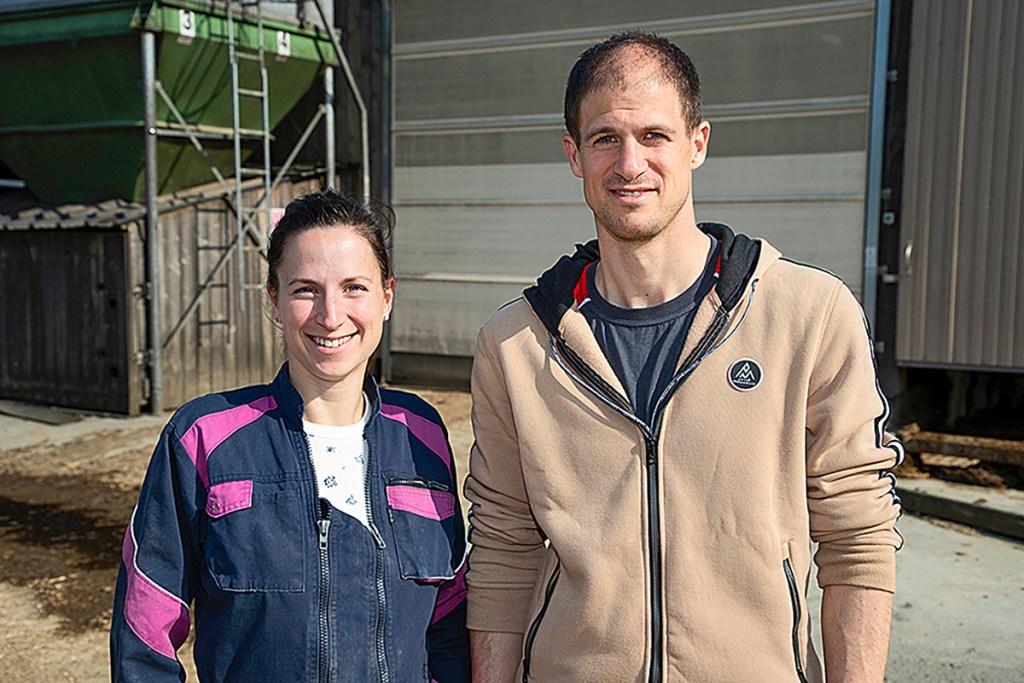
Animal performance increased slightly with the Aura, but Adéle does not attribute the increase to solely the autonomous machine. However, they would both choose the Aura again. “Timewise, we are at the limit, and without Aura we would have to give up the bull finishing business,” explains Adéle.
“Taking the feeding off the chore schedule is an enormous relief for us, and we have more time for our private lives, especially at the weekend,” adds the cattle farmer.
Although they did use a self-propelled feeder before purchasing the feeding robot, they are now saving two hours every day. “When Aura is at work, one of us is at the farm. This way, nobody has to drive to the farm if something should happen,” adds Etienne.
“Although our Aura has been in operation for only 18 months, we’ve already got so used to it that we once forgot to refuel it,” Etienne tells us with a smile on his face.
Today, Aura sends an alarm to the farmers’ smartphones when the fuel level is low. Also, a signal always lights up as soon as the tank is on reserve.
“Whoever sees the signal, fills up the robot immediately,” explains Etienne.
Currently, Aura takes twelve hours/day to feed the animals, using 3.3l/hr. At the time of our visit, it already had 7,000 hours on the clock, but it was still on its first set of solid rubber wheels, which measure 23 x 9-10 and require firm ground.
Again, we asked what could be improved. The initial reaction of both was a shrug. Even our own suggestion, that some form of network connection between the milking robot and the feeder would be handy, was not met with any enthusiasm. “When I move animals to another group, it merely costs me a tap on my smartphone with Aura,” Adéle countered.
On productivity
The investment costs of an Aura, including the full yard survey and a WiFi network, are around £250,000 — with a (guaranteed) residual value of around £67,500 after having clocked up 30,000 hours. Kuhn reckons the working life is eight years if catering for 180 cows plus followers, which equates to around ten hours per day.
This results in an estimated annual cost of £23,300 for depreciation, £7,500 for service and repairs (3%), £8,311 for diesel (3.5 l/hr, £0.66/litre) and £7,500 for interest (6%). That makes £46,611 or £127.70/day.
The potential wage saving amounts to around £14,600 (two hours per day at £20/hour times 365 days).
Summary
After years of trials Kuhn has announced the start of series production of its autonomous mixer wagon. Following a precise route on a map and powered by a diesel engine, Aura can automatically cut the required amount of forage directly from the pit face and load it into the tub, which then mixes and feeds out the ration.
Kuhn has no time to spare, because, by the time the machine goes to market in the UK and Ireland, it has to have set up service teams and convinced its dealers. We are also keen to see a new battery-powered Aura and fleet options for herds larger than 280 cows. Watch this space!
Martin Zäh
For more up-to-date farming news click here and subscribe now to profi and save.